As you can see by this issue’s cover feature, manufacturing, especially in the US, is embracing the advantages of laser additive manufacturing (LAM). Readers of ILS and our web site already knew this because the pages of the magazine have featured editorial on 3D printing, AM, and LAM, and our site posts News items every month on these subjects.
Unless you’ve been living in a cave without Internet access, you have been bombarded with news of applications for 3D printing, much of it seemingly generated by engineering students and ‘would be’ manufacturing engineers who have the wherewithal to purchase a 3D printer from Staples.
Unless you think this is a derisive slap at the above, nothing could be further from the truth; every 3D printing news item is a boost for laser additive manufacturing. The reality is that the 3D processes getting all the headlines don’t actually use lasers, but those reporting usually mention the other laser applications such as selective laser sintering (SLS), direct metal deposition (DMD), and other processes as further examples of how 3D can be extended into ‘real’ additive manufacturing.
For this, I am personally grateful because any publicity for an industrial laser application is good and we, the industrial laser community, thank the 3D printing equipment suppliers and process developers for raising the attention of the manufacturing world, and the President of the US, to the advantages of additive manufacturing. By so doing, the suppliers have given a decided boost to the fortunes of the makers of LAM equipment and the process developers such as the GE engineers who authored the cover feature.
For the first time in this writer’s recall, laser material processing is the recipient of volumes of continuous publicity simply by riding on the coattails of an allied application. It now seems that SLS, SLM, DMS, and other LAM applications are appearing routinely in almost every publication serving the manufacturing sector.
At the recent ICALEO in Miami, more than 15% of the papers presented in various sessions described LAM in one process or another. ICALEO has a reputation for presenting advanced material processing applications as they position for transition into industry so the many papers on the subject give further credence to LAM’s rapidly increasing acceptance by industry. During the Q & A session of the Business Forum held in conjunction with ICALEO, the speaker panel was asked to select the most important future industrial laser application. I selected LAM and was pleased to see most of the attendees nod in affirmation.
At the ICALEO opening Plenary session, Dr. Xiaoyan Zeng (Huazhong University, China) spoke on challenges and opportunities for LAM. He introduced his talk with slides showing his government’s funding for this process development. As a driver for China’s increased funding for this work, President Obama’s support for the National Additive Manufacturing Initiative (www.namii.org) has been a key for the future of manufacturing in the US.
Dr. Zeng showed a large 5 kW CO2 laser powered gantry system capable of building large titanium structural components that are equal in quality and operational performance to those manufactured using die stamping processes that require complex dies that can take up to two years to design and manufacture. The LAM process takes only 55 days. Attendees were very impressed by the size and complexity of the parts being used in the manufacture of new Chinese commercial aircraft.
Thus, LAM has vaulted to a position of prominence in manufacturing for the future and, setting aside the obvious advantages of the processes, we can thank 3D printing for attracting the attention of the world’s industrial sector.
About the Author
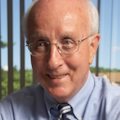
David Belforte
Contributing Editor
David Belforte (1932-2023) was an internationally recognized authority on industrial laser materials processing and had been actively involved in this technology for more than 50 years. His consulting business, Belforte Associates, served clients interested in advanced manufacturing applications. David held degrees in Chemistry and Production Technology from Northeastern University (Boston, MA). As a researcher, he conducted basic studies in material synthesis for high-temperature applications and held increasingly important positions with companies involved with high-technology materials processing. He co-founded a company that introduced several firsts in advanced welding technology and equipment. David's career in lasers started with the commercialization of the first industrial solid-state laser and a compact CO2 laser for sheet-metal cutting. For several years, he led the development of very high power CO2 lasers for welding and surface treating applications. In addition to consulting, David was the Founder and Editor-in-Chief of Industrial Laser Solutions magazine (1986-2022) and contributed to other laser publications, including Laser Focus World. He retired from Laser Focus World in late June 2022.