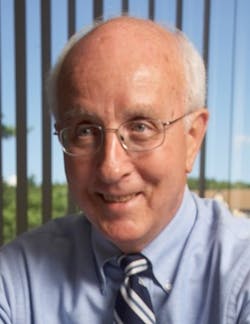
Several decades ago, I entered the industrial laser business with an interest in lasers’ possibilities as a welding process. This was the early days for lasers as an economic alternative to similar processes like electron beam and tungsten inert gas (TIG). My background in welding included these two, plus resistance-spot and flash-butt welding—so I knew a little about joining metals in an industrial environment. Then, the workplace environment was one of the key factors for a cool reception from welding engineers.
In the 1970s, the nascent industrial laser industry was trying to convince the market that laser technology was suitable as a factory floor process. The products were transitioning scientific devices, not even dressed up to compare to a conventional welder. Then, I had the hutzpah to walk the floor in a plant with a welding engineer pointing out the joining operations that could be replaced with a laser.
Looking back, I know why the few applications that made it then were accomplished with the unwavering support of a few laser welding industry pioneers—called ‘risk takers’—ready to defend this new technology within their companies. I’d like to construct an honor roll of these prescient engineers. If any of you are reading this, consider this as a big pat on the back.
Today, laser welding is an accepted industrial process in plants around the world, in the auto, energy, aerospace, medical devices, agriculture, and heavy equipment industries, to name a few. In this issue, with its Hot Applications and Welding Advances themes, we will be featuring joining opportunities for a new crop of industrial lasers, led by fiber lasers.
Starting our series on laser welding is the cover feature of this issue contributed by Tomáš Mužík, who describes the laser welding of brass musical instruments at venerable Amati-Denak in the Czech Republic (see article). Formerly soldered by craftsmen, the formed blanks are now laser-welded. Jarno Kangastupa from Coherent-Finland shows how a new fiber laser technology overcomes the prior limitations of fiber lasers in welding zinc-coated steel and aluminum, both of which are susceptible to spatter from fusion joining processes (see article). And Ryan Forsell (Superior Joining Technologies) profiles Teresa Beach-Shelow, who established Superior Joining Technologies 25 years ago in Machesney Park, IL, with her husband Thom Shelow. She noticed lasers as the next big thing in manufacturing and knew her business, of which she is president, needed these advanced processing tools. Their first laser was purchased for micro-welding applications and soon demand produced the need for a second micro laser. Today, the company has four laser welders and is about to add another (see article).
On other topics, solar photovoltaic cell expert Finlay Colville is back with us, who presents his view on the key drivers behind end-market deployment within this sector and the uptick in the use of laser-based tools for rear-side contact openings as part of passivated emitter rear contact cells (see article).
Laser cladding consultant Roger Kaufold describes how laser cladding technology is being used in the repair and reconditioning of all types of mechanical components in a great primer and update on the process (see article). And finally, as Bob Kolcz (Prima Power) writes, the RV industry is showing impressive growth, so one supplier, Rock Run Industries (Millersburg, IN), purchased a fiber laser with a 10-station tower that cuts up to 20 mm of mild steel, with efficiency and quality (see article).
About the Author
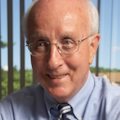
David Belforte
Contributing Editor
David Belforte (1932-2023) was an internationally recognized authority on industrial laser materials processing and had been actively involved in this technology for more than 50 years. His consulting business, Belforte Associates, served clients interested in advanced manufacturing applications. David held degrees in Chemistry and Production Technology from Northeastern University (Boston, MA). As a researcher, he conducted basic studies in material synthesis for high-temperature applications and held increasingly important positions with companies involved with high-technology materials processing. He co-founded a company that introduced several firsts in advanced welding technology and equipment. David's career in lasers started with the commercialization of the first industrial solid-state laser and a compact CO2 laser for sheet-metal cutting. For several years, he led the development of very high power CO2 lasers for welding and surface treating applications. In addition to consulting, David was the Founder and Editor-in-Chief of Industrial Laser Solutions magazine (1986-2022) and contributed to other laser publications, including Laser Focus World. He retired from Laser Focus World in late June 2022.