Industrial lasers continue solid revenue growth in 2016
Most of the world's economies decreased in gross domestic product (GDP) in 2016, leading to unsettled times for the global manufacturing sector. Setting aside the normal up-and-down cycles of manufacturing, a number of factors occurred last year that affected the manufacturing economy. Globalization hit a wall, with foreign direct investment in rich economies dropping 40% from peak and international lending down 9% in the past two years. This concerned the International Monetary Fund and World Bank as nations turned inward, potentially worsening global malaise in manufacturing—specifically in the U.S., where the presidential election results sent a message of rising protectionism. The World Trade Organization slashed growth in global trade volumes to 1.7% and negative signs appeared, such as shipping containers falling 4% after four decades of double-digit expansion.
Growth prospects for the global manufacturing economy continued to weaken, compounded by recent events such as the Brexit vote, terrorist attacks around the world, China's delays in restructuring, the rethinking of the Trans-Pacific Partnership, and the U.S. presidential election outcome, all of which created elevated levels of uncertainty for businesses.
Industrial laser revenues had traditionally been tracking the growth curves for the machine tool industry until recovery from the 2008-2009 recession had started. Then, led by pent-up buying demand for high-power fiber laser sheet metal cutters and high-volume smartphone component manufacturing using ultrafast-pulse (UFP; also known as ultrafast) solid-state lasers, the industrial laser community experienced rapid recovery from the recession, leading to substantive growth in annual revenues.
The past two years have seen industrial lasers outperform the machine tool sector, with solid single-digit growth in annual revenues. This report will again show strong growth, which runs counter to more modest gains reported in the global machine tool sector. There are valid reasons for this: strong double-digit sales of high-power fiber lasers, a surge in excimer laser processing of new model smartphone displays, expanding laser additive manufacturing of aircraft engine components, and significant rises in microprocessing using UFP lasers are major examples.
Industrial lasers are key components in automated material processing systems. As the manufacturing sector turns more toward Industry 4.0, shifting from centralized to decentralized manufacturing, production methods need to automatically adjust to fluctuating supply chain demands. State-of-the-art processing equipment, controlled by sensors and computers on the Internet, are now being implemented, and lasers, by their very nature, will likely be the adaptable energy source of choice. ILS readers are already aware of this through published editorial.
Laser market overview
This year's market report is positively impacted by exceptionally large revenue growth in the microprocessing segment, resulting from major orders placed with one laser supplier. As described in a feature article in this issue (see p. 14), the use of polycrystalline silicon as a thin-film transistor material enables fabrication of organic light-emitting diode (OLED) displays with improved appearance, higher speed, and lower power consumption. The most effective means of transforming amorphous silicon into the polycrystalline form is through the use of excimer laser-based, low-temperature polysilicon annealing. Coherent (Santa Clara, CA) has received orders for a number of units powered by their excimer laser for deliveries through 2018. Extensive revenues for these lasers started with 2016 shipments, resulting in strong double-digit growth in the microprocessing sector. Also, higher-power lasers for rapidly growing additive manufacturing applications have increased growth rates in the "other" category.
TABLE 1 shows a 10.2% growth in 2016 revenues over the revised 2015 total (the rationale for this revision is covered in the sidebar). Significant changes in 2016 revenue growth rates are a drop of 4% in CO2 laser revenues, reflecting price drops in the low-power sector and a slight slowing of orders for high-power CO2 lasers used in sheet metal cutting for the market economics explained above.
Fiber lasers, which pushed through the billion-dollar level in 2015, experienced strong double-digit growth in 2016, a fact corroborated by more than half of the editorial published in ILS in 2016. Fiber lasers continue to erode the market share of other laser types, especially high-power CO2 lasers for sheet metal cutting. At two of the largest 2016 metal fabricating shows, EuroBlech in Germany and Fabtech in the U.S., among the dozens of high-power laser cutters on display, only one was powered by a CO2 laser compared to the previous year, where several high-power CO2 units were exhibited. Other than the random need for a user to cut non-metals, there are few remaining CO2 laser-powered cutters being sold compared to booming fiber laser sales. Today, potential buyers can shop more than 60 global suppliers of fiber laser-powered flat sheet cutters, ranging in output power from 2 to 12kW. At power levels from 8 to 12kW, the fiber laser is now able to cut with the quality of an equivalent CO2 laser, but at higher cutting speeds.
TABLE 2 clearly shows the impact on microprocessing revenues for 2016 by high-power excimer sales for the silicon annealing applications described above. Laser revenues for marking applications slowed in 2016 as increased competition pressured unit selling prices while unit sales continued on at strong pace, a trend that will continue in 2017.
In 2016, while macroprocessing continued as the highest (47%) revenue materials processing sector, it was being challenged by microprocessing at 35%, thanks to a more-than-estimated $190 million of excimer units shipped for the annealing application.
Laser market details
Through the years, marking (which includes engraving applications) has experienced annual growth since ILS started tracking this process three decades ago. Year-in/year-out, this sector grew regardless of economic situations because it is a process that is so ubiquitous that it has become a commodity akin to a copy machine. And like printers, the unit selling price has declined annually as more companies offer equipment globally. Although revenues have slipped into the minus column over the years (TABLE 3), unit sales continue to grow as applications such as marking produce and eggs claim new sales.
CO2 laser revenues for marking/engraving have also felt the pinch of new competition driving down unit selling prices. And low-power fiber laser gains (47% of the total) in the market have also impacted CO2 laser as well as solid-state laser sales, both of which fell into negative territory this year.
Last year, ILS published seven editorial features on laser marking, three of which dealt with marking highly reflective materials and two introduced UFP/ultraviolet (UV) laser marking of difficult materials. These new laser marking processes bode well for continued growth in the marking sector.
Microprocessing
Microprocessing revenues (TABLE 4) rose 23.5%, a disproportionate increase (102.8%) mostly attributed to the excimer laser OLED display annealing application described earlier. For this report, only shipments made in 2016, the beginning of a multi-year delivery schedule by supplier Coherent, were included. Without these revenues, growth in microprocessing in 2016/2017 would be positive in the low single digits.
Microprocessing, minus the laser annealing application, shows the fastest growth rate of the three industrial laser sectors in this report. The negative solid-state laser revenues in 2016 are an aberration resulting from a revision made in the 2015 number. This sector is comprised of countless applications for hundreds of industrial lasers that together generate overall expanding revenues, but the annealing process lacked a "killer" application—such as what sheet metal cutting provides for macroprocessing revenues.
Fiber laser revenues in 2016 continued to replace both CO2 and long-pulse solid-state lasers, with process developers using newly developed UV and 2μm fiber lasers that show promise for substantive revenue growth.
Looking more deeply into microprocessing processes (TABLE 5), the impact on current and future revenues is evident. The 105.4% increase in the display category is based on an analysis of 2016 quarterly reports, which accounts for shipments of excimer laser annealing systems this year. As shipments of these units increase in 2017 and further into 2018, they may dominate sales in this application sector.Fine metal processing, led by thin-strip blanking applications, and non-metal processing of reinforced polymer materials are revenue technologies expected to increase market share as industry acceptance grows. Additive manufacturing, with potential for "killer" applications, showed strong double-digit growth in 2016. As noted earlier, sales of higher-power lasers for this application are included in the "other" category in macroprocessing. And finally, solar processing opportunities were slow to proceed in 2016, resulting in a decrease in revenues.
Macroprocessing
The largest revenue stream in 2016 continues to be in macroprocessing (TABLE 6), where sales of lasers in excess of 1000W grew a respectable 4.5% in an important category that experienced a capital-equipment investment drought as emerging nation and BRIC economies were set back. In 2016, the macroprocessing category represented more than 47% of all industrial laser revenues, continuing a trend to a decreasing share started in 2015 as microprocessing grew revenues in expanding markets-for example, the OLED display sector.
In this category, growth of high-power fiber lasers—at the expense of CO2 lasers, primarily in sheet metal cutting operations—is evident, as fiber laser sales continue their dominance by 30% growth over CO2 lasers. Fiber laser revenues are fast approaching 50% of all revenues in the macroprocessing category as end users are increasingly using these lasers for welding and cutting applications, where they compete with equivalent-power CO2 lasers in terms of process speed and quality, while exceeding in operating costs and energy efficiency.
High-power and -brightness direct-diode lasers (in the "other" category) are gaining market share as more integrators are developing and introducing systems for brazing, welding, and cutting applications. At 2016 fabricating shows, Mazak Optonics (Elgin, IL) showed a new purpose-built direct-diode laser cutting system with power capability to 4kW. Several other system integrators are also introducing diode-powered cutters, and others are in the advanced development stage. Currently, high-power, high-beam-quality direct-diode lasers sell at a premium to equivalent-power fiber lasers—a situation that may change as orders increase.
TABLE 7 shows that the growth driver for macroprocessing revenues has been in metal cutting—specifically sheet metal cutting, where more than 7000 units that generated more than 76% of total revenues were sold in 2016, a year in which capital equipment investment was reduced in countries such as Brazil that would normally be expanding their fabricating industries. After a sputtering start, capital equipment sales in China perked up and finished the year on an upswing in government-sanctioned equipment investment. Asia continues to be the largest market for laser sheet metal cutting, with 38 domestic and 14 international companies supplying fiber laser-powered systems. Even so, metal cutting only squeaked out a modest 3.5% growth.
Stepped-up high-power laser welding applications, among them very high-power fiber laser welding on oil pipelines, helped grow the macroprocessing category. High-power lasers are also experiencing expanding use in additive manufacturing, where production demands are calling for higher laser powers in other applications such as cladding and paint stripping.
Conclusions on 2016
Marking revenue growth was less than forecast last year as a result of declining unit prices. Macroprocessing revenues were also less than forecast, partially because of uncertainty over the U.S. presidential election, Brexit, a general slowdown in capital equipment investment, and some unfavorable currency changes. Microprocessing revenues were higher than last year's forecast as initial revenues from record orders for OLED-display annealing lasers were recorded.
With the exception of these revenues, the industrial laser market experienced modest growth in 2016, a turbulent year for global manufacturing—taken together, market growth was 10.2%. This contrarian performance was supported by the production demands of key industrial sectors such as automotive, aerospace, energy, communications, and microelectronics, in which laser material processing is a significant contributor.
Outlook
Looking ahead to 2017, laser equipment suppliers expect market conditions to repeat those of 2016, with total anticipated revenues growing almost 9%. Microprocessing, which includes laser annealing, should grow by 18%, while marking (1%) and macroprocessing (5%) will show modest gains.
CO2 lasers will continue to experience decreasing revenues as high-power fiber lasers increase share in the cutting market. The total fiber laser market may grow by 8%, while excimer and diode lasers (in the "other" category) should show a strong double-digit pattern. Market assumptions for 2017 are based on industry estimates of a repeat of 2016 results.
The market forecasts in this report were created, with the assistance of Laser Markets Research/Strategies Unlimited for PennWell Corporation, from public data released by public companies, other public data, direct contacts, and e-mail correspondence with industry companies. The numbers are based on data available up until the end of November 2016, with fourth-quarter data estimated from public companies' guidance advice. These estimates will be updated online after fourth-quarter data becomes available in February 2017.
As a consequence, modifications were made to all tables presented in last year's published report. The headings in this year's tables are revised as follows: past-year data will be a Revision, if required, of that presented in preceding issues, current-year data will be an Estimate based on company reports available at press time, and future-year data will be our Projection based on information available to ILS by the end of the reporting year.
Categories used in this report are:
- Marking, which includes all lasers used in this application, plus those CO2 lasers used in non-metal engraving;
- Microprocessing, which includes all lasers with output power levels <1kW; and
- Macroprocessing, which includes all lasers with output power levels >1kW.
About the Author
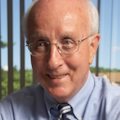
David Belforte
Contributing Editor
David Belforte (1932-2023) was an internationally recognized authority on industrial laser materials processing and had been actively involved in this technology for more than 50 years. His consulting business, Belforte Associates, served clients interested in advanced manufacturing applications. David held degrees in Chemistry and Production Technology from Northeastern University (Boston, MA). As a researcher, he conducted basic studies in material synthesis for high-temperature applications and held increasingly important positions with companies involved with high-technology materials processing. He co-founded a company that introduced several firsts in advanced welding technology and equipment. David's career in lasers started with the commercialization of the first industrial solid-state laser and a compact CO2 laser for sheet-metal cutting. For several years, he led the development of very high power CO2 lasers for welding and surface treating applications. In addition to consulting, David was the Founder and Editor-in-Chief of Industrial Laser Solutions magazine (1986-2022) and contributed to other laser publications, including Laser Focus World. He retired from Laser Focus World in late June 2022.