Which pulse length and wavelength is right for your application?
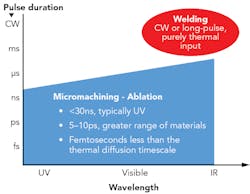
Going back about 20 years, the only real ultraviolet (UV) laser used in production was the excimer laser, which with its typical pulse length of about 20ns was also the ultrafast-pulse (UFP; also known as ultrafast) laser of the time. In fact, Lumonics (Bedford, MA) had a 2ns laser, and there were some applications where there was clearly a difference in the quality of the processing by going to pulse lengths in the low nanosecond regime.
On the other side of the visible spectrum, infrared (IR) processing (non-CO2) was done almost exclusively with Nd:YAG lasers or their derivatives. Infrared fiber lasers (and disk lasers) at this time did not exist in the industrial sense, even though today they are the industry workhorse. Working in the visible portion of the spectrum was just beginning to be investigated.
In the past 10 years or so, UFP technology—lasers with pulse lengths <1ns—have become standard on manufacturing floors. So, now there are options to consider when choosing the right UV laser for a particular task. Furthermore, when purchasing a UFP laser operating in the UV, visible and IR wavelengths also come along with the package. In a typical manufacturing environment, only one wavelength is usually used because in this setting, the number of parts and materials to be processed is very small. For an R&D or job shop type of environment, it is frequently useful to have access to all three wavelengths. In our laboratory, we have nanosecond, picosecond, and femtosecond lasers all operating at IR, visible, and UV wavelengths so that the customer can investigate a number of possibilities and choose the correct configuration for the task at hand.
FIGURE 1 shows a graph of pulse duration (from femtosecond to continuous-wave [CW]) and wavelength (IR to UV). Lasers with output characteristics near the origin (bottom left) are ideal for achieving the highest-quality features on target in that they have both short wavelength and short pulse length. The lasers at the top right have long pulse lengths and IR wavelengths, so these lasers are not generally suited for micromachining applications, although they may be quite useful for other things like welding, joining, surface treatment, and additive manufacturing. Note that there is no mention of applications for lasers with output characteristics shown at the top left—using a long-pulse UV laser is somewhat counterproductive for most applications. Therefore, this discussion will focus on lasers contained within the shaded blue area.
Also, even though both CO2 and excimer lasers have been mentioned and are still of great value in materials processing, the current discussion will focus on lasers with wavelengths of 2μm to about 300nm. This also excludes frequency-quadrupled lasers, but these lasers were much more useful before picosecond and femtosecond lasers were commercially available. And because of reliability issues, they are not used unless absolutely necessary (such as excimers).
The TABLE shows some features of the three wavelengths under discussion. In summary, UV photons cost more and come in lower power than IR photons, but smaller, cleaner features are possible and the material removal is more precise, yet slower than using IR. The visible wavelength is used for applications where needed, such as backside processing of transparent materials or indium-tin oxide (ITO) removal, but because of eye safety issues, other alternatives are usually considered first.
Nanosecond lasers
Diode-pumped solid-state (DPSS) lasers were first commercially introduced into industrial environments in the late 1990s. The first units had low output power of a couple of watts at 355nm. Prior to diode pumping, laser light was available using lamp pumping, but these lasers were very unreliable. At that time, a couple of watts of nanosecond UV light cost in excess of $100,000.
This market matured and these lasers are now available from a number of different manufacturers in the IR, visible, and UV, with 10W UV output power for less than $50,000. Ten watts of IR power from a fiber laser currently costs less than $10,000. For the most part, the pulse durations of these lasers are in the range of tens to maybe hundreds of nanoseconds.
Picosecond lasers
Picosecond lasers were first commercially introduced in about 2005, with Lumera (now part of Coherent [Santa Clara, CA]) being the major player at the time. It did not take long for a number of other players to enter this market [1]—now, there are a variety of choices available for both scientific and industrial lasers. Almost all have pulse lengths between 2 and 20ps. There are some lasers with pulse lengths in the hundreds of picoseconds, but the utility of these lasers is questionable for most applications. In fact, a large portion of this pulse length regime is referred to as the "valley of death" because the material interaction is quite poor—certainly no better than using a nanosecond laser and in many cases, the quality is even worse. So when I discuss picosecond lasers, it should be taken to mean lasers with pulse lengths under 20ns—perhaps as long as 50ns, but no more.
One of the claims of UFP laser utility is that there is wavelength-independent absorption. This may be true at shorter pulse lengths, but at nominally 10ps, there is almost always a difference in the quality between parts processed at IR vs. UV wavelengths.
For example, consider FIGURE 2, which shows a feature made in 50μm-thick polyethylene terephthalate (PET) using a 100mm f-theta lens and approximately the same output power for each different sample. The nanosecond IR and UV samples (c-d) both show a lot of debris and charring on the edges. The picosecond samples (g-i) are all markedly improved over the nanosecond samples, but there is still a visual difference between the three wavelengths at the 10ps pulse length.The question is always, "What quality is 'good enough' for the application at hand?" Since the IR wavelength has more power available and the cost of the photons is less than the UV photons, this wavelength is used for most applications, but the UV is useful if the highest quality is needed and/or the smallest feature size is needed. In general, picosecond lasers are used where higher power is valuable on target quality.
When these lasers first became available, the cost was in excess of $300,000. Now, the cost for a medium-power (20W), IR-only laser is about $130,000–150,000, with the harmonics and higher power running the cost to over $200,000. Companies like EdgeWave (Würselen, Germany) also provide very high-power lasers using slab amplifiers, but in general these lasers are used for very specific applications.
A newcomer to the UFP market, IPG Photonics (Oxford, MA), is now selling a 50W laser with a 15ns pulse length for about $65,000. In addition to the low cost, these lasers require only a 60s warmup time from cold start, and the small head and rack-mount power supply can easily be integrated into either existing platforms or small envelope designs.
Femtosecond lasers
There are femtosecond lasers commercially available from ~10 to 900fs, but the real useful range is between ~200 and 500fs. Above 500fs, the laser is really more like a picosecond laser. Below 200fs, there is usually no noticeable improvement in quality and the optics become much harder to manage because of the broadband nature of the light. In this useful range, in most materials there is not a noticeable difference in the quality of many materials, so the majority of applications for this type of laser currently use the fundamental wavelength. There are some materials like glass and some polymers that, even in the femtosecond regime, process with better edge quality in the UV—and UV is also useful if the smallest spot size is needed. Note that one of the other virtues of a smaller spot size is a smaller kerf, meaning less material removal and therefore less debris and a cleaner cut.
As with the picosecond laser discussed above, the initial entry price of these lasers was in excess of $300,000. Now, the cost for a high-power (20W), IR-only laser is about $200,000–225,000, with the harmonics adding another $20,000.
On the very high-energy side, companies like Amphos (Herzogenrath, Germany) make femtosecond lasers with hundreds of watts of output, but these are not normally used in typical micromachining applications and they also carry a large price tag. Light Conversion (Vilnius, Lithuania) sells a model that is air-cooled, has an extremely small power supply, plugs into the wall, and costs just over $100,000 for 3W of IR. Long-time femtosecond laser supplier Amplitude Systèmes (Pessac, France) is offering a 100W, 300μJ/pulse laser, as well as a new, low-cost 10W laser with a <500fs pulse length. Industry giants Spectra-Physics and Coherent are also offering very competitive products.
Price disrupter IPG Photonics is now selling a femtosecond laser with 10W output at the fundamental wavelength and with a ~500fs pulse length, which should enter the market at approximately $100,000. So, the push to get a femtosecond laser on the market below $100,000 is definitely achievable, and may be reality by the time this article actually goes to press.
What's next?
Now, the ideal laser I wished for many years ago is pretty much a reality. I am not really sure where things go from here. A few years ago, I would have said that higher pulse energy is needed, but I have found over the last few years that for most applications, we do not even use the power or energy per pulse we have available.
When using galvanometers, a good benchmark is that at least 50μJ/pulse is needed for picosecond and nanosecond lasers, and 25μJ/pulse for femtosecond lasers with pulse lengths <500fs. Too much energy per pulse—or too high a repetition rate—can compromise the on-target quality. Photonics Industries (Ronkonkoma, NY) is selling lasers with up to 700μJ of pulse energy for those applications that really require it. Going to pulse lengths shorter than about 200fs does not seem to be an interesting path. So, smaller and cheaper seems to be the direction and femtosecond lasers are becoming almost "pedestrian" [2]. Therefore, margins will deteriorate, but volumes—when these lasers are well below $100,000—should increase significantly.
In closing, the simple way to choose the correct laser for your application is to choose the one that has sufficient quality and costs the least. I look at an application and assume it can be done with nanosecond IR photons. If not, then consider either using visible or UV photons and/or going to shorter pulse lengths. This seems like quite a daunting task, and it may be, but there are good resources—including laser manufacturers and laser contract manufacturers—that can help in this process.
REFERENCES
[1] R. Schaeffer, "Commercially available ultrafast-pulse lasers: An update," Industrial Laser Solutions, 29, 6, 18–20 and 32 (Nov/Dec. 2014); http://bit.ly/2fTNRbY.
[2] See http://bit.ly/2ghQdCr.
About the Author
Ron Schaeffer
Ron Schaeffer, Ph.D., is a blogger and contributing editor, and a member of the Laser Focus World Editorial Advisory Board. He is an industry expert in the field of laser micromachining and was formerly Chief Executive Officer of PhotoMachining, Inc. He has been involved in laser manufacturing and materials processing for over 25 years, working in and starting small companies. He is an advisor and past member of the Board of Directors of the Laser Institute of America. He has a Ph.D. in Physical Chemistry from Lehigh University and did graduate work at the University of Paris. His book, Fundamentals of Laser Micromachining, is available from CRC Press.