Application versatility of nanosecond pulsed fiber lasers
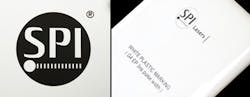
Although pulsed fiber lasers have only just passed a decade of industrial adoption, the roll call of their achievements is truly impressive. From a standing start, they now dominate the global laser marking market with estimates that more than 30,000 units will be deployed in 2014. They have also made significant inroads into a broad range of advanced micromachining applications. All this is fueled by the fact that these lasers are compact, air cooled, competitively priced, and maintenance free…as close to "Fit and Forget" as you can get. Industrial lasers with no alignment or maintenance requirements…who would have believed it if you'd suggested that just 10 years ago?
MOPA
Much of these lasers' success can be attributed to the great parametric flexibility offered by master oscillator power amplifier (MOPA)-based fiber lasers. These lasers use a semiconductor seed to generate the pulses so they are not constrained by the limitations of conventional Q-switch technology. This has been the traditional basis for diode pumped solid-state (DPSS) pulsed lasers, offering a single pulse duration and a limited repetition frequency range. The MOPA approach allows users to vary the pulse duration and operate over a broader operating frequency range, enabling the pulse parameters to be easily tailored to suit individual applications. The results are quite staggering; elevating what was originally conceived as a humble marking laser to a micromachining marvel.
Some may ask why they would want to control the pulse duration, and the answer is relatively simple. Materials react differently to applied energy, and the ever-increasing diversity of materials being processed by lasers means that the tools need to be more sophisticated and versatile because one size does not fit all.
The most commonly used fiber lasers are those with pulse durations of between 100 and 200 ns, operating in the 20–80 kHz range. They are typically used for general marking applications, giving a good balance between peak power and pulse energy and generating acceptable results on many metallic and plastic parts. Many of these lasers are based on q-switched designs, so they are performance-limited. Some of today's MOPA-based sources are capable of operating in a 3–500 ns pulse duration range, offering three orders of magnitude of controllability. Coupled with their ability to operate at 1 kHz to 1 MHz, they offer an unrivaled capability in pulse optimization, allowing any pulse duration to be operated at any frequency. These lasers are setting new benchmarks for advanced marking and micromachining applications.
Shorter pulses
Shorter pulses, typically less than 30 ns, enable more controlled energy input when processing sensitive materials. These pulses still have the peak power to overcome materials processing thresholds, but have lower pulse energy to reduce localized thermal damage. Good examples can be found in decorative marking of consumer electronic products. Many manufacturers have adopted the use of plastic cases, which are typically hard coated to provide scratch resistance. Marking these types of materials without damaging the surface is particularly challenging, as a careful balance between peak power, pulse energy, and average power is required.
Initially, these applications were considered to be suited only to green or ultrashort pulsed laser processing, but the cost and robustness of these sources was considered a barrier to some applications. Fortunately, the flexibility of the new generation of ns pulsed fiber lasers has yielded parameters that can produce these subsurface marks reliably and cost effectively in the required mass production environments. Similarly the marking of clear anodized aluminium (FIGURE 1) with a dark subsurface mark has been perfected, again using short ns pulses at high rep rates.
The proliferation in the use of touch screens has generated a more functional thin-film processing application for these lasers. Thin conductive films on glass and plastics need to be accurately scribed to leave perfectly isolated grids. The variability of the composition and thickness of these films is not always as well controlled as you'd like, and it falls on the laser to overcome these variations. This can often be achieved by multipass processing, where the initial pass removes the bulk of the film, while secondary passes using significantly different processing parameters --often using shorter pulses, higher pulse frequency, and higher speed -- are used to clean up residues. This improves edge quality, ensuring that there are no electrical shorts that could impact device yield. The ability of the laser to change parameters such as pulse duration and pulse energy in a few microseconds means that parameter switching during processing can be seamless.
Longer pulses
Conversely, the use of longer pulses great than 200 ns can yield quality and productivity improvements in a range of other applications such as dark marking (often referred to as black anneal marking), cutting, welding, and micromachining.
For example, in dark marking of stainless steel, a careful solid state oxidation process is required where no surface melting can be tolerated. The ability to use long duration pulses and high repetition rates that more closely resemble gated CW (continuous wave) pulsed lasers than conventional high peak power ns pulses, can provide more controlled heating characteristics that give superior and faster marking.
Pulse duration in engraving (FIGURE 2) applications can have a significant impact on material removal efficiency. Experimental investigations have shown that the optimal pulse duration is unsurprisingly material dependant. For example, the use of 450 ns pulses can yield a 20% increase in material removal versus conventional 200 ns pulses on steels, while on aluminium, more modest increases can be achieved at 300 ns.Simplified pulse control
SPI's pulsed fiber range is solely based on its MOPA design, with PulseTune waveforms giving users simplified pulse control, offering additional sources with four different beam qualities. The question that is often asked is why?
The reality is that different beam qualities (FIGURE 5) do not just give you different spot sizes, but the energy distribution and the pulse characteristics can significantly impact application performance. To help explain, a simple sample has been generated that shows marked performance differences between lasers that have at first glance quite subtle differences in M2 values (M2 is a measure of beam quality), max pulse energy, and max peak power.When comparing cutting performance, you might expect the S-type true single mode with the highest beam quality of <1.3 and smallest spot size to be the best, but in reality, the Z-type with M2 less than 1.6 and with its slightly higher pulse energy and peak power is more effective. However, the L-type with M2 less than 2 lags significantly due to the extensively larger spot and correspondingly lower power density. However, when looking at area removal, the roles are reversed, with the L-type being able to remove a considerably greater area, thanks to the larger spot and broader energy distribution, with the Z & S types lagging. The keener-eyed individuals may also note that the S-type removed area has a slightly greyish metallic tinge while the Z and L are a bright frosted white finish. This is due to the sharpness of the S-type spot which tends to gouge into the aluminium, resulting in a poorer finish. The final part of the exercise is the depth of field test, where the S-type laser wins hands down, being able to maintain a process at a significantly out of focus position. Although the effect may change, the general message is that certain applications can benefit from the use of a tailored beam quality. Defocusing or merely changing the spot size with a high beam quality source does not necessarily have the same effect.
The unique versatility offered by today's nanosecond MOPA-based fiber lasers is linked to the extended performance in pulse duration and pulse frequency. This allows users greater ability to optimize pulse parameters, notably improving application results. This level of control has enabled a new generation of applications, some of which were previously considered to be only possible with green or ultra-short sources. So, if you've got a challenging application, perhaps you should see what a nanosecond pulsed fiber laser could do. The results are conclusive; whether marking or micromachining, these lasers are truly versatile manufacturing tools.
About the Author
Jack Gabzdyl
Industry Manager – Electronics, TRUMPF Laser UK Ltd
Dr. Jack Gabzdyl is Industry Manager – Electronics at TRUMPF Laser UK Ltd (Southampton, England) and has more than 30 years of laser materials processing experience. He obtained his PhD in laser processing from Imperial College London in 1989. He has since had a number of technical and marketing positions at BOC Gases, Advanced Laser Solutions, and TWI before joining TRUMPF (formerly SPI Lasers) in 2007.