Joe Gibbs Racing (JGR) made its debut on the NASCAR racing circuit in 1992 and won its first victory at the prestigious 1993 Daytona 500, considered to be the premier race of the season. Racing one car with mixed success for the first few years, JGR realized that the future in NASCAR would be multi-car teams. So in 1999 they brought out the famous No. 20 Home Depot car driven by rookie Tony Stewart on board. Stewart immediately brought JGR fame as he won three races and Rookie of the Year in his first season. By 2000, led by Stewart and Bobby Labonte, JGR won 10 races out of 34 and the NASCAR Cup Series Championship. JGR added a third Cup Series car in 2005 capturing a third Cup Series Championship. Today JGR is considered as one of the top teams in Cup Series racing.
Headquartered in Huntersville, NC, JGR has 450 employees in a modern building that houses 18 Doosan Infracore CNC machines, a Mitsubishi laser cutter, a water jet cutter, EDM wire machines, EDM sinker, EDM hole Popper, and a Stratasys 400 FDM machine all running two shifts a day, that enable them to manufacture just about all they need to field a stable of racing cars. About 37 engineers turn ideas into reality feeding the demand for manufactured parts. In addition the machines turn out replacement parts for those that are worn due to attrition, as well as inventorying all the replacements that are needed for a normal racing schedule.
JGR manufactures in-house because they seek to protect the propriety ideas of the design engineers from the competition, which could be difficult when dealing with a lot of outside contract people. Also, they believe that having the best people with the best equipment means they are able to sustain the high quality of parts needed to keep their cars in contention. And finally, the shop is able to supply parts practically on demand, rather than having to wait weeks for outside subcontractors to deliver on their schedule. This is important when R&D develops a part that improves their competitive edge and they want to get this to the track as soon as possible.
Mark Bringle, technical sponsorship and marketing director, told ILS that JGR has about 900 parts approved for production. In 2000 JGR had only 8 engineers doing R&D on about 70 pieces. Last year they went through 3600 different pieces. All this constant improvement rather than settling on what they have makes their cars quicker, faster, lighter, and stronger. He believes that JGR has the finest manufacturing complex in all of the sport. They have been able to do this through the sponsorship program that allows machine suppliers to use the manufacturing building for a showroom for meetings and to demonstrate their equipment to other customers in a NASCAR setting.Some of the parts the company manufactures incorporate small incremental changes that are barely noticeable to the naked eye. Within a family of parts these increments can be very small. When the car is being worked on at the racetrack and the crew needs to make a change relatively quickly they can't take the time to measure a part; rather the company decided to mark every part for easy and quick identification by reading the number. Being a bit old fashioned, they first tried color coding with ink pens, which didn't work out well. Bringle, who has a background in manufacturing, suggested that the laser might be a more effective solution.
So he attended IMTS (International Manufacturing Technology Show) to look over the suppliers and listen to their business concepts with the caveat that the JGR name is an asset so they are fussy about with whom they do business. They evaluated the equipment and then sat with the potential suppliers to make sure that their philosophies were aligned with JGR. Bringle says suppliers essentially take stock in the operation and the shop becomes their showroom. From the evaluation, the company selected Telesis Technologies (Circleville, OH; www.telesis.com) as the system provider.
The Telesis solution was based on JGR's need to mark and encode more than 500 various racing parts for the following: identification and tracking, analyzing part failures, encrypting competitive information, matching parts for optimum compatibility, and dressing parts with sponsor graphics and logos. For the flexibility to handle the diversity of materials used in NASCAR, Telesis suggested its FQ20 FIBER laser because it has a small footprint, is powered by 110VAC, and is air cooled. This unit allows for a mobile workstation that fits the lean mold important in today's factory cell environment.
The CDRH Class I aluminum workstation chosen is 60-in wide and 48-in deep, which allows a workspace that can process long dash panels and axles. A 49-in door provides easy access to load parts. Inside the system is a programmable Z tool post with a 5-in jaw rotary device mounted to an X-linear programmable 350 mm slide assembly.
The old method of having three part patterns to mark a dash panel is no longer in-play as the panel can now be laid out on the linear stage and one program and the Telesis Merlin LS software can complete processing of the 12-in panels in one setup operation.
In operation, the fiber laser runs at full power when needed for jobs requiring fast cycle time, deep engraving, or annealing on high-luster stainless steel and titanium parts. Power can be reduced for marking various lightweight composites like poly and glass filled nylon. With full programmable operation, large work area, and intuitive software, the laser marking system allows the Joe Gibbs team to have the same consistency in laser processing as they do in fielding competitive race cars for their fans and sponsors.JGR runs their shop using Job Boss software, which develops route sheets that call out all the production processes for a given part number. As the parts leave a machining center they are routed to the laser marker where a full-time operator then marks the part volumes required from downloaded identification numbers. After marking, the route sheet directs the parts to the next process. Why a full-time operator? Well with 18 Doosan Infracore CNC machines and the Mitsubishi laser, water jet, and EDM machines churning out parts 20 hours a day, a lot of parts need to be marked.
JGR is very pleased with the laser marker. So much so that they also mark giveaways for receptions they, and their sponsors, hold at the center.
With the Telesis systems JGR found they could mark the instrument panels for the cars with all the instrument designations. They also mark all the tools that are used in the track garages so they can identify theirs from others. And each chassis has a number on it so that NASCAR can inspect it at pre-race to avoid tampering.
After two years of virtually maintenance-free operation Joe Gibbs Racing is completely satisfied with the choice of laser marker, which has become a key part of the company's drive for continued success on the NASCAR circuit.
About the Author
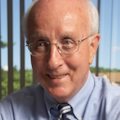
David Belforte
Contributing Editor
David Belforte (1932-2023) was an internationally recognized authority on industrial laser materials processing and had been actively involved in this technology for more than 50 years. His consulting business, Belforte Associates, served clients interested in advanced manufacturing applications. David held degrees in Chemistry and Production Technology from Northeastern University (Boston, MA). As a researcher, he conducted basic studies in material synthesis for high-temperature applications and held increasingly important positions with companies involved with high-technology materials processing. He co-founded a company that introduced several firsts in advanced welding technology and equipment. David's career in lasers started with the commercialization of the first industrial solid-state laser and a compact CO2 laser for sheet-metal cutting. For several years, he led the development of very high power CO2 lasers for welding and surface treating applications. In addition to consulting, David was the Founder and Editor-in-Chief of Industrial Laser Solutions magazine (1986-2022) and contributed to other laser publications, including Laser Focus World. He retired from Laser Focus World in late June 2022.