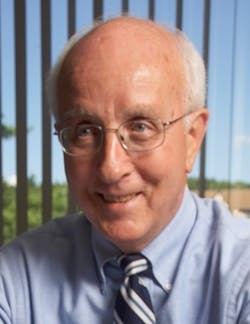
I'm sitting here in front of the keyboard thinking, this can't be 2003. Why, it was only a few weeks ago that we celebrated 2002—wasn't it? Oh lord, is this what getting older is all about, time whizzes by and your mind says it was only yesterday?
So much of what we do is measured by the passing of time. This magazine is published on a strict production schedule; each month editorial has to move from my keyboard to production on specific dates. This means editorial for the first half of the year is being worked on now. You're reading January and we are working on March. Maybe that's why the year passes so quickly; you're recovering from the New Year's Eve and we're thinking St. Patrick's Day.
This month's annual economic review comes across as being somewhat optimistic, with good reason I believe. Historically, economic slowdowns in the industrial laser sector have not exceeded three years. And there are no reasons to think this one will be an aberration, unless some unforeseen political, or ethnic, originated earthquake shatters the status quo.
What this? Sounds like he's accepted terrorism as a way of life. Perhaps. We have been living with it for 15 months now and, except for some inconveniences at the airports, it has barely changed the way we do things. This year's economic review hardly mentions the impact of extended anti-terrorism activities or even the prospect of war. At least at the time this was written. Strange world we now live in isn't it.
A comment made by a leading laser supplier caught me by surprise. Responding to my query about business in 2002, he said, "If it hadn't been for defense business we would have had a no-growth year." This, he implied, was found business that the company had not planned on but willingly accepted. By defense he meant lasers sold for materials processing applications in companies that produce weapons systems. Even in these uncertain times some people benefit. Like the company we know that is working on bullet marking with lasers.
Casting aside the impact of potential conflicts somewhere in the world, the best days for industrial laser processing are still ahead. Expect no market contractions resulting from replacement of laser technology by some new materials processing methods.
Quite the opposite. With the, as yet, unfulfilled promise of diode lasers, both as economical pumping devices for solid-state lasers and as compact, cost effective direct processors appearing ready to drive down equipment costs, new market opportunities are expected. The growth of hybrid applications is taking laser processing into market sectors now served by competitive technologies. The introduction of high-power fiber lasers into tough industrial applications, such as welding auto bodies, could well open that elusive market for on-line welding.
This month's cover shows a technology advance that moved more quickly from the laboratory to industry than any of us expected. In July of 2000, ILS reported on a process developed at Liverpool University, in cooperation with BOC, that produced quality cuts in thick steel sections using very low CO2 laser power and high pressure oxygen. Now Bender Shipbuilding (Mobile, Alabama) is using this process, as refined by Alabama Laser (Munford, Alabama), to cut up to 2-inch-thick steel faster and more accurately than plasma (see page 5). And this is the beginning of a new market for lasers.
So the future looks bright even though the markets are sluggishly recovering from a severe downturn. Be of good cheer readers, the best is yet to come.
About the Author
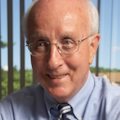
David Belforte
Contributing Editor
David Belforte (1932-2023) was an internationally recognized authority on industrial laser materials processing and had been actively involved in this technology for more than 50 years. His consulting business, Belforte Associates, served clients interested in advanced manufacturing applications. David held degrees in Chemistry and Production Technology from Northeastern University (Boston, MA). As a researcher, he conducted basic studies in material synthesis for high-temperature applications and held increasingly important positions with companies involved with high-technology materials processing. He co-founded a company that introduced several firsts in advanced welding technology and equipment. David's career in lasers started with the commercialization of the first industrial solid-state laser and a compact CO2 laser for sheet-metal cutting. For several years, he led the development of very high power CO2 lasers for welding and surface treating applications. In addition to consulting, David was the Founder and Editor-in-Chief of Industrial Laser Solutions magazine (1986-2022) and contributed to other laser publications, including Laser Focus World. He retired from Laser Focus World in late June 2022.