Is that Lady Godiva leading the charge?
I'm sitting in a taxi, heading from London City Airport to my hotel near Hyde Park one evening. We stop for a traffic light in the vibrant Canary Wharf section of this capital city. Suddenly I see an arm squeegee water off the windscreen (windshield here in the U.S.). The arm is attached to a topless young woman. "Here now!" says the cabby, "You know better than to do that." I ask if he is referring to the topless condition. "No," he says, seemingly unimpressed by the skin show, "they're not supposed to bother taxis."
What about the topless bit, I ask. He responds with great aplomb, "Can't blame her for trying something new. The windscreen washing business is very competitive."
Recovering somewhat from the shock of seeing a semi-nude person, on a brightly lit street in an upscale section of London, performing a task that's usually the province of homeless men, I ponder the cabby's comment about innovation.
I've just come from visiting a company that has an innovative concept for materials working that could advance the metal removal process. As the Brits like to say, it's early days yet, and this process has a ways to go before it's efficacy in the marketplace is proven. Even so, it's the doing that has my attention, and I have plenty of time to ponder on this because the cabby seems to be stopping at every traffic light in London. So much for the vaunted London cabby whose encyclopedic street knowledge is supposed to know where every possible shortcut is.
The technology of laser materials processing is now more than forty years old. There aren't a lot of manufacturing technologies that remain vibrant for this length of time. Think about it. Then think of the word maturity. I posit it's a word that has yet to be applied to industrial laser processing. Granted some applications, such as ceramic scribing, have been around for decades, but have benefited from innovations that keep them from being grouped under the mature technology label. Can't say that about resistance welding flame cutting, pin stamping, or induction hardening. These are mature technologies.
Brings to mind an e-mail I recently received from a Scandinavian contact asking about the state of the art of laser surfacing in the U.S. Thirty years after laser heat treating, cladding, and alloying were invented they have yet to become a mature manufacturing process and only lack an innovative response from industry users to ratchet to the next level. At ICALEO, held in Jacksonville this year, numerous papers described advanced developments in laser surfacing and entire sessions were devoted to laser deposition (cladding) and multi-dimensional manufacturing.
Also at this premier laser processing conference an entire session was given over to polymer joining. Talk about innovation in the stagnant welding market. Who would have thought joining non-metals would take-off so soon.
Another session had three papers describing developments in rock and concrete drilling and cutting, a subject that has had occasional interest spurts over the years and now may have tickled the innovative fancies of some potential industrial users.
This is what industrial laser technology is all about: processes far from maturity allowing their advocates to develop techniques, equipment, and markets that add to the annual growth of the overall business.
In the industrial laser market it doesn't take a naked lady to get attention. Wouldn't hurt, but not needed. Just a cost-effective solution to some company's manufacturing problem.
About the Author
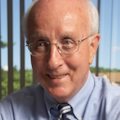
David Belforte
Contributing Editor
David Belforte (1932-2023) was an internationally recognized authority on industrial laser materials processing and had been actively involved in this technology for more than 50 years. His consulting business, Belforte Associates, served clients interested in advanced manufacturing applications. David held degrees in Chemistry and Production Technology from Northeastern University (Boston, MA). As a researcher, he conducted basic studies in material synthesis for high-temperature applications and held increasingly important positions with companies involved with high-technology materials processing. He co-founded a company that introduced several firsts in advanced welding technology and equipment. David's career in lasers started with the commercialization of the first industrial solid-state laser and a compact CO2 laser for sheet-metal cutting. For several years, he led the development of very high power CO2 lasers for welding and surface treating applications. In addition to consulting, David was the Founder and Editor-in-Chief of Industrial Laser Solutions magazine (1986-2022) and contributed to other laser publications, including Laser Focus World. He retired from Laser Focus World in late June 2022.