Fiber-optic and stretchable optical sensors improve robot hands
Carnegie Mellon University (CMU; Pittsburgh, PA) researchers have developed a three-fingered soft robotic hand with multiple embedded fiber-optic sensors as well as a new type of stretchable optical sensor uniquely suited for use in robotic hands.
RELATED ARTICLE: Stretchable polymer skin wired with Bragg gratings senses strain
By using fiber optics, the researchers were able to embed 14 strain sensors into each of the fingers in the robotic hand, giving it the ability to determine where its fingertips are in contact and to detect forces of less than a tenth of a newton. In addition, a new stretchable optical sensing material not yet incorporated in the current version of the hand could potentially be used in a soft robotic skin to provide even more feedback.
"If you want robots to work autonomously and to react safely to unexpected forces in everyday environments, you need robotic hands that have more sensors than is typical today," said Yong-Lae Park, assistant professor of robotics. "Human skin contains thousands of tactile sensory units only in the fingertip and a spider has hundreds of mechanoreceptors on each leg, but even a state-of-the-art humanoid such as NASA's Robonaut has only 42 sensors in its hand and wrist."
Adding conventional pressure or force sensors is problematic because wiring can be complicated, prone to breaking, and susceptible to interference from electric motors and other electromagnetic devices. But a single optical fiber can contain several sensors; all of the sensors in each of the fingers of the CMU hand are connected with four fibers, although, theoretically, a single fiber could do the job, Park said.
The Carnegie Mellon researchers discussed the robotic hand, developed together with researchers at Intelligent Fiber Optic Systems Corp., with support from NASA, Sept. 29 at the IEEE International Conference on Intelligent Robots and Systems, IROS 2015, in Hamburg, Germany. A report on the highly stretchable optical sensors was presented Oct. 1 at the same conference.
Each of the fingers on the robotic hand mimics the skeletal structure of a human finger, with a fingertip, middle node, and base node connected by joints. The skeletal "bones" are 3D-printed hard plastic and incorporate eight sensors for detecting force. Each of the three sections is covered with a soft silicone rubber skin embedded with a total of six sensors that detect where contact has been made. A single active tendon works to bend the finger, while a passive elastic tendon provides opposing force to straighten the finger.
The hand, developed with mechanical engineering students Leo Jiang and Kevin Low, incorporates commercially available fiber Bragg grating (FBG) sensors, which detect strain by measuring shifts in the wavelength of light reflected by the optical fiber.
Despite their advantages, conventional optical sensors don’t stretch much—glass fibers stretch hardly at all and even polymer fibers stretch typically only 20-25%, Park noted. That is a limiting factor in a device such as a hand, where a wide range of motion is essential. Park has previously developed highly stretchable microfluidic soft sensors—membranes that measure strain via liquid-conductor-filled channels—but they are difficult to make and can cause a mess if the liquid leaks out.
So Park, working with mechanical engineering students Celeste To from CMU and Tess Lee Hellebrekers from the University of Texas, invented a highly stretchable and flexible optical sensor, using a combination of commercially available silicone rubbers. These soft waveguides are lined with reflective gold; as the silicone is stretched, cracks develop in the reflective layer, allowing light to escape. By measuring the loss of light, the researchers are able to calculate strain or other deformations.
Park said this type of flexible optical sensor could be incorporated into soft skins. Such a skin would not only be able to detect contact, as is the case with the soft components in the CMU hand, but also measure force.
SOURCE: CMU; http://www.cmu.edu/news/stories/archives/2015/september/optical-robotic-hands.html
About the Author
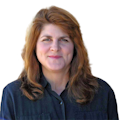
Gail Overton
Senior Editor (2004-2020)
Gail has more than 30 years of engineering, marketing, product management, and editorial experience in the photonics and optical communications industry. Before joining the staff at Laser Focus World in 2004, she held many product management and product marketing roles in the fiber-optics industry, most notably at Hughes (El Segundo, CA), GTE Labs (Waltham, MA), Corning (Corning, NY), Photon Kinetics (Beaverton, OR), and Newport Corporation (Irvine, CA). During her marketing career, Gail published articles in WDM Solutions and Sensors magazine and traveled internationally to conduct product and sales training. Gail received her BS degree in physics, with an emphasis in optics, from San Diego State University in San Diego, CA in May 1986.