Conventional and elliptical-core two-mode optical fibers have been fabricated with wavelength ranges for two-mode operation typically limited to around 150 nm. But researchers at The Hong Kong Polytechnic University (Hong Kong, China) and Beijing Jiaotong University (Beijing, China), have modeled photonic-crystal fibers (PCFs) that can support two-mode operation over wavelength ranges of 1200 nm (from 600 to 1800 nm).1 Two-mode fibers can be used as mode converters, bandpass/bandstop filters, acousto-optic tunable filters, add/drop multiplexers, and fiber sensors.
Typically, a PCF has a solid core surrounded by a holey cladding region. When the ratio of the hole diameter to the hole-spacing pitch is less than 0.45, PCFs can support single-mode operation for any wavelength. When this ratio is large for small hole-spacing pitches (1 to 3 µm), the fibers become nonlinear PCFs, which can be used for supercontinuum generation. For intermediate ratios from approximately 0.45 to 0.65, however, and for wavelengths less than the cutoff wavelength for the PCF, the fiber can support both the fundamental and the second-order modes. For a PCF with a hole spacing of 5 µm and a diameter to hole-spacing ratio of 0.6 at 1550 nm, the mode-field patterns supported are those of the first- and second-order modes only (see figure).
Analysis of the mode field for these two-mode PCFs shows that the mode-field intensity pattern of the four second-order modes actually varies along the fiber length because of the coherent mixing of the four modes and is not stable against environmental disturbance. The polarization states of the fundamental mode also vary. To solve this problem, the researchers intentionally introduced birefringence by modeling air holes with different diameters along the two orthogonal directions of the PCF. By inducing this birefringence, the four second-order modes split into two groups, with the cutoff wavelength between the two groups being several hundreds of nanometers or more.
For this high-birefringence PCF, the fundamental mode and the second-order modes are stable over a wavelength range of 0.6 to 2 µm, covering almost the entire low-loss window of the silica fibers. The confinement losses of the second-order mode supported by a two-mode PCF were less than 0.025 dB/m for wavelengths below 1800 nm, sufficiently low for many device applications.
Two-mode strain sensor
The researchers have already experimentally demonstrated a two-mode PCF-based interferometric strain sensor at wavelengths from 650 to 1300 nm.2 The sensor uses the interference between the two modes at the output of the fiber. Because of perturbation effects and axial strain, the output intensity distribution varies with the differential phase shifts between two modes.
Another application for a two-mode PCF with a wide wavelength range of operation is a tunable optical filter. The researchers have shown that acoustic flexural waves propagating along optical fibers provide efficient coupling between the fundamental and the second order modes, provided that the acoustic wavelength is matched to the length of the mode beat. The modal beat length of the high-birefringence PCF was found to decrease with wavelength, indicating that the wavelength at which the mode coupling occurs can be controlled by varying the wavelength (frequency) of the acoustic wave.
If light is first launched into the fundamental mode of the PCF, the acoustic wave will couple the light to the second-order mode at a particular optical wavelength, which is determined by the acoustic frequency. Because the second-order mode is less confined than the fundamental mode, it can be removed by a mode stripper. The power carried by the fundamental mode will then experience a high loss at that particular wavelength, forming a bandstop or notch filter. The device can also be configured to function as a bandpass filter by introducing a mode converter just before the mode stripper to convert the fundamental mode to the second-order mode. The center wavelength can be tuned by varying the frequency of the acoustic wave applied to the optical fiber.
“We are currently looking at the possibility of using this fiber for simultaneous measurement of strain and temperature,” says Wei Jin, professor in Electrical Engineering at The Hong Kong Polytechnic University. “The sensitivities of the modal and polarization beat length of the PCF to strain and temperature are quite different and strongly dependent on wavelength. The wide wavelength range for two-mode operation will allow for the implementation of modal and polarimetric interferometer sensors at different operating wavelengths and hence with different strain and temperature sensitivities.”
REFERENCES
1. W. Jin et al., Optics Express 13(6) 2082 (March 21, 2005).
2. J. Ju et al., IEEE Photon. Technol. Lett. 16, 2471 (2004).
About the Author
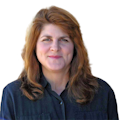
Gail Overton
Senior Editor (2004-2020)
Gail has more than 30 years of engineering, marketing, product management, and editorial experience in the photonics and optical communications industry. Before joining the staff at Laser Focus World in 2004, she held many product management and product marketing roles in the fiber-optics industry, most notably at Hughes (El Segundo, CA), GTE Labs (Waltham, MA), Corning (Corning, NY), Photon Kinetics (Beaverton, OR), and Newport Corporation (Irvine, CA). During her marketing career, Gail published articles in WDM Solutions and Sensors magazine and traveled internationally to conduct product and sales training. Gail received her BS degree in physics, with an emphasis in optics, from San Diego State University in San Diego, CA in May 1986.