LASER OPTICS: Scottish company custom-collimates laser diodes
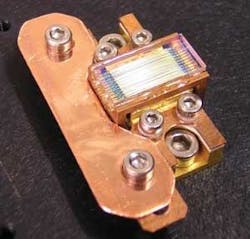
Without a doubt, the high-power diode-laser industry has seen leaps and bounds in the last decade in terms of raw power output. Extracting all that power and making it useful, however, is another matter—often requiring expensive correction micro-optics.
The fabrication of these optics can be mask-based, requiring custom-made masks for each run, or grinding-based, which limits the shapes and spatial resolution of the correcting features.
PowerPhotonic (Edinburgh, Scotland), a spin-off company from Heriot-Watt University (Edinburgh, Scotland), has developed a novel approach for the fabrication of such micro-optics—what the company calls “spectacles for diode lasers.” The process produces phase plates that provide custom aberration correction for individual diode bars and stacks. The result is an increase of up to ten times in fast-axis brightness, leading to significantly more light coupled into an optical fiber.
“The technology came from a requirement at Heriot-Watt University to pump high-power slab-waveguide lasers,” says Roy McBride, PowerPhotonic’s managing director. “What they found was that they couldn’t achieve the brightnesses they needed from commercial stacks. They realized to do that they had to correct both the collimation and aberration, and also the pointing errors between emitters across the whole stack. We’ve basically industrialized and commercialized that technology.”
The product of more than ten years’ work at Heriot-Watt, PowerPhotonic started shipping optics last year.
Direct-write fabrication
The approach starts with an extensive beam characterization of a given diode stack or bar, operated even at full power, to assess the characteristics of the diode. A precision direct-write approach is then used to produce the high-resolution features in silica substrates to correct the aberrations, leading in turn to a clean line focus.“Some processes need to be embossed on softer glass and some only work on plastic, whereas ours works on silica, which is a highly damage-resistant material,” McBride says.
The divergence is much reduced—by more than a factor of 25 in a project PowerPhotonic carried out with the European Space Agency—and the increase in beam quality is clear (see figure).
Overall beam brightness can be improved by as much as a factor of 10 to near-diffraction-limited quality. By avoiding the high costs of masks in mask-based optics production, McBride says, the process is industrially competitive. What’s more, it’s fast.
“In terms of turnaround time, we’re faster than mask plus wafer fab—the reality is our turnaround time is limited by how quickly we can ge stuff antireflection coated rather than how quickly we can get it through our process,” McBride says.
The company’s primary customer base is laser-diode OEMs and system integrators, but the company also makes lenslet arrays and beam transformers, producing, for instance, Gaussian to flat-top phase plates for materials processing, and general beam homogenizing and shaping for incoherent sources.
“We can produce any 3-D relief surface that we like,” McBride says. “We can tailor the beam transformer to the application; we don’t have to produce a one-size-fits-all solution.”
A key feature for the diode micro-optics is that they can be fitted into existing designs, so customers needn’t redesign their products to fit the micro-optics that will make the best of them.
“There are other ways of doing it but no one else is offering a product that lets you take a stack and double its brightness—or increase it by a factor of ten, which we’ve done in extreme cases—and it’s because it’s a direct-write process that allows us to make a different phase plate for every diode laser.”