Spectral processor and ASE source aid fiber sensing
Many applications for fiber sensing use multiple fiber Bragg gratings (FBGs) arranged in series. This arrangement allows a single terminated fiber or fiber loop to monitor several locations in an industrial plant, process line, or engineered structure. The most common way of providing discrimination between the different FBGs is to use FBGs with slightly different wavelengths. Several schemes have been proposed to separate these signals in the wavelength domain, using a tunable laser, an optical spectrum analyzer, or multiple filters.
One technique combines a single broadband source with a programmable spectral processor (PSP) that acts as a programmable filter. The flexibility of the PSP allows this approach to be optimized for tracking both AC ("alternating current," or rapidly oscillating about zero) and DC ("direct current," or steady) signals. It can also be used to set up a carrier/sideband form of signal demodulation. Moreover, the ability to create customized, nonlinear filter slopes allows a linear signal response to be derived from a nonlinear FBG response function.
FBG sensing
An FBG consists of a short length of optical fiber having a periodic modulation of refractive index along its length. This periodic structure causes the FBG to act as a narrowline filter with a peak reflectivity (and transmission dip) at a specific wavelength, called the Bragg wavelength, which is determined by the period length of the FBG and the refractive index of the fiber. If the refractive index of the FBG is changed by a temperature shift, or the period is altered in some way (by compression or extension), a shift in the peak reflected wavelength results. Detecting this shift is the basis of fiber sensing.
Sensing with FBGs is a rapidly growing field encompassing diverse applications. For example, FBGs are now routinely buried in large structures such as bridges and airframes to monitor both static and dynamic strain levels. They are used in power plants to monitor temperature. In addition, FBGs are now widely used as the basis of a new generation of industrial sensors such as pressure transducers and accelerometers.
One of the advantages of FBGs as embedded detectors is that multiple FBGs can be connected in series through a single input/output node, providing there is some way to separate the reflected signals from the different FBGs (see Fig. 1). The signals can be acquired as reflection peaks or, if a fiber loop is used, as transmission dips.
Several schemes have been used to sort the signals and "demodulate" the parameters of interest (temperature, pressure, stress, and so on)—that is, to derive an electronic signal that has a known relationship to the physical parameters. A popular method to demodulate the signal is to use a simple edge filter with a photodetector; wavelength changes are converted into intensity variations as the wavelength of the reflected light changes and moves across the cutoff slope of the edge filter. One drawback of this approach is that it does not allow tradeoffs between sensitivity and range. More important, a separate filter is required for each returned FBG signal. Other methods include the use of an expensive, high-resolution optical-spectrum analyzer or a tunable laser.
We have recently demonstrated a completely different method of fiber sensing based on a broadband source and a programmable spectral processor (PSP) that offers unprecedented flexibility. When used with a single photodetector, this setup both discriminates between the different FBGs and provides a platform to demodulate these signals.
Micromirrors modify grating-dispersed light
The PSP, which is called the Lambda Commander, was jointly developed by CiDRA (Wallingford, CT) and Newport. This instrument is based on the digital-micromirror chip developed by Texas Instruments (Dallas, TX) that is used in many compact computer projectors and projection televisions. The surface of this chip consists of a two-dimensional array of approximately 750,000 MEMS (microelectromechanical-systems) mirrors. Each of these mirrors has two possible angular states (± 10°) that can be individually addressed.
In the PSP, this chip is combined with a bulk diffraction grating. Incoming light from the fiber input is collimated and dispersed by the diffraction grating across the chip. In this way the incoming light is split into 1000 discrete wavelength intervals. Each wavelength interval covers approximately 400 pixels in the orthogonal (nondispersive) axis across the micromirror chip. Light reflected back off the surface of the chip is directed by the diffraction grating into a second collimator that focuses the light into an output fiber. The grating and chip are spatially arranged so that the two deflection states of each mirror switches the output between on and off.
Because each wavelength interval covers approximately 400 pixels in the nondispersive axis of the chip, the light at any wavelength isn't just selectively switched on and off, but can also be variably attenuated at up to 30 dB with a minimum incremental attenuation of 0.1 dB. This means that the PSP can be used as a programmable filter that can be used to create virtually any spectral contour on demand.
Sensing with a broadband source
A typical broadband source for use with a PSP in fiber sensing is an erbium-doped-fiber ASE source that has a 1.5-µm center wavelength. An ASE source is preferred over alternative sources (such as a superluminescent light-emitting diode) in many applications, because the ASE's high average power results in superior signal-to-noise data and/or shorter data-acquisition times.
In an ASE source, an erbium-doped fiber is pumped by a 980-nm-emitting laser diode; the ASE is similar to an erbium-doped fiber amplifier, except that it is designed to run without an input. The amplified noise created by this open-input source constitutes the broadband output that makes up the spectral characteristics (see Fig. 2). The ASE source used in this strain application has an output-power specification of 13 dBm.
Several implementations of the PSP are possible. In the simplest approach, each filter is sensed by using the PSP to generate a simple ramp-filter function. The reflections (or transmissive dips) from the different FBGs are sampled sequentially by moving the ramp function to each FBG wavelength in turn, while strongly attenuating (at greater than 30 dB) the signals from the other FBGs. This method can also be used to produce normalized data by rapidly switching between positive and negative filter slopes and applying a simple difference over the sum ratio for the two signals.
Alternatively, the different ramps can each be on-off modulated at a different frequency, resulting in a type of carrier/sideband demodulation. Here, each FBG signal is transposed into the amplitude-modulation sidebands of a particular carrier frequency.
Both of these methods can be used to detect AC and DC signals such as an oscillating strain or pressure, although they are better suited to detecting AC effects. A method that is ideally suited to demodulating DC signals entails programming the PSP to produce a simple Gaussian FBG-like spectral profile. The PSP is slaved to the photodetector signal so that its center wavelength tracks the FBG wavelength in a closed-loop manner; the data is then derived from the center wavelength of the PSP.
In addition to providing a simple method of sampling each FBG at will with a single photodetector, use of a PSP has other advantages over a broadband system based on fixed filters—for example, the ability to vary the slope. A steep slope provides excellent sensitivity over a limited range, whereas a gradual slope provides a longer range with reduced sensitivity. Differing slopes could be created with fixed optical filters, but only the PSP can change slope on demand.
Nonlinear slopes can also be created. In some sensing applications, a change in the parameter being detected will not always produce a corresponding linear change in FBG wavelength. With a PSP, however, the filter slope can be contoured to produce a linear demodulation signal to produce a near-constant signal-to-noise figure as the parameter changes.
The method in action
We recently conducted a series of fiber-sensing experiments with a broadband source and PSP in our applications lab. A series of three FBGs was used, two of which were held under constant ambient conditions. The other FBG was attached to a simple cantilever beam that applied linear strain to the FBG. Using conventional tools (an optical-spectrum analyzer), the reflection spectrum of the FBG was measured as a function of strain. This confirmed that the FBG reflection peak shifted linearly as the applied strain was increased from 0 to approximately 1000 µstrain (one µstrain causes a dimensional change equivalent to one-millionth of the original length).
This particular FBG had a peak wavelength that varied under stress between 1535.5 and 1537 nm, so the PSP was set to create a linear filter edge from 1535 to 1538 nm. An optical power meter with an indium gallium arsenide sensor then recorded the output from the PSP as a function of strain (see Fig. 3). The measured power had a linear dependence on the applied strain over the range from 0 to 1200 µstrain.
About the Author
Hector Lara
Hector Lara served as senior product manager – instrumentation and photonics for MKS Newport (Irvine, CA) from February 2001 through January 2006.
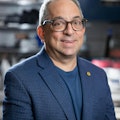
Jason Eichenholz
Jason Eichenholz is the cofounder and CEO of Relativity Networks and a pioneer of laser- and optics-enabled innovation, product development, and commercialization. He holds a Ph.D. in optical sciences and engineering, as well as more than 90 patents within the field. Eichenholz co-founded Luminar, a leading provider of LiDAR. In 2023, he co-founded Relativity Networks.