Algorithm for acoustic fiber sensing isolates a small signal from large disturbances
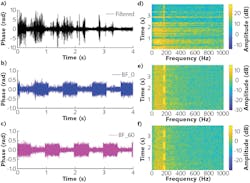
Fiber-optic distributed acoustic sensing (DAS) takes advantage of the extreme sensitivity that the light characteristics in optical fibers can have to the slightest displacement of the fiber. Long segments of fiber, up to kilometers long, can measure and localize sounds and other disturbances to submeter accuracy (along the fiber) using, for example, the variations in phase of Rayleigh backscattered light. DAS has some unique advantages, including large coverage, high spatial and temporal resolution, and strong ambient adaptability, so it is widely applied in many fields. However, DAS has trouble picking out a small signal spaced somewhat away from the fiber from a sea of other disturbances also away from the fiber.
At present, DAS is still troubled by an aliasing problem from multiple adjacent acoustic sources due to its physical mechanism. On the one hand, weak target signals may be submerged by intense broadband environmental noise; on the other hand, multiple target signals are challenging to detect individually. Now, a group of researchers from the Shanghai Institute of Optics and Fine Mechanics of the Chinese Academy of Sciences (CAS) has proposed and preliminarily tested a solution to this problem of picking the right signal from multiple nearby disturbances that achieves acoustic multisource aliasing suppression using directionally coherent enhancement technology.1
Atomic norm minimization algorithm
The approach is based on so-called beamforming, where the overall signal from an evenly spaced linear array of acoustic sensors (in this case, segments of the fiber) listening to a source somewhere near the array is subjected to computer processing via an “atomic norm minimization” (ANM) algorithm, which coherently enhances a chosen small region somewhere near the fiber containing a signal, enabling the system to block out other disturbances.
While the algorithm may not seem intuitive, it was experimentally tested. A single-frequency laser was split into two beams—oscillation and probe—and the probe beam chopped using an acousto-optic modulator, resulting in a 20 ns pulse width and an interrogation rate of 5 kHz. Backward Rayleigh-scattered light from a 200-m-long sensing fiber (wrapped around a mandrel in the lab experiment) was locally interfered with the oscillation beam. A weak 170 Hz acoustic signal source was positioned at -60° from the chosen axis and a strong broadband (100–300 Hz) noise source was located at 0°, both about 5 m away from the wound fiber assembly.
While the signal was completely buried in the raw data, the directionally coherent enhancement algorithm was able to spatially find and isolate the signal with a signal-to-noise ratio (SNR) enhancement of approximately 21 dB. Similarly, two spatially separate acoustic sources with the same frequency but with different phase were also each spatially isolated (see figure).
The researchers say that many common problems from multisource aliasing, such as low recognition accuracy and lack of robustness, can be resolved using their method, which they say could help lead to large-scale implementation of DAS.
REFERENCE
1. Z. Wang et al., Opt. Lett. (2020); https://doi.org/10.1364/ol.404736.
About the Author
John Wallace
Senior Technical Editor (1998-2022)
John Wallace was with Laser Focus World for nearly 25 years, retiring in late June 2022. He obtained a bachelor's degree in mechanical engineering and physics at Rutgers University and a master's in optical engineering at the University of Rochester. Before becoming an editor, John worked as an engineer at RCA, Exxon, Eastman Kodak, and GCA Corporation.