Error proofing is a systematic process for improving the reliability, quality, and stability of manufacturing methods. In factory-automation applications, this process often relies on the use of noncontact sensors to ensure that specific quality processes have been followed to minimize the possibility of human error.
For years, system integrators have deployed limit switches and IR and LED sensors in error proofing to detect the presence or absence of a part on a production line or they have used light grids to perform tasks such as profile detection, object recognition, overhang control, and height measurement. While these products can be used to determine the presence of a part, laser-based triangulation products are now available that can improve performance by precisely judging the position of the part. For example, when performing simple distance-measurements functions, low-cost laser-based displacement sensors can be most effective. In a stationary mode, the sensors can accurately measure the distance of an object from a target. When used with conveyor-based systems, these sensors can generate surface-height profiles of products as they move past.
Thickness measurement can also be performed using two opposing laser displacement sensors. By aiming sensors at the opposite sides of an object, computing the distance measurements of both laser readings and the separation between the laser sensors yields the thickness of an object. Such a system was recently developed by Laser-view Technologies (Lionville, PA) for a manufacturer producing plates of various contours.
To address less-complex applications such as Data Matrix reading and part profiling, industrial-sensor vendors are offering smart sensors with simple programmability, PLC interface capability, and Ethernet compatibility. For example, Cognex (Natick, MA) offers several product lines that address these different markets, including the company’s Checker and In-Sight series of vision sensors.
In the near future, ifm efector (Exton, PA) will also embed an advanced algorithm into its Efector Dualis smart sensor. In operation, the sensor uses incident light or backlight to detect the contours of an object and compares them with the contours of one or several models in a reference image. Depending on the degree of conformity, a result is output if a specific model is found.
Structured light
Although applications such as parts-presence detection, barcode inspection, and color product identification can be performed with smart sensors that incorporate 2-D visible light imagers, more-sophisticated sensors are incorporating one or more sensing techniques to provide 3-D data. Structured-light techniques have long been used to extract depth information from scenes, but only recently have companies such as SICK IVP (Linköping, Sweden) combined structured laser lighting, cameras, and computer into single image sensors to perform these tasks. Using devices such as SICK’s IVC-3D, automated systems can detect and compute 3-D geometrical features of objects, as well as control an external machine, robot, or conveyor without an external PC (see Software and Computing, p. 73).
Servo-Robot (Milwaukee, WI) and Meta-Scout (Munich, Germany) have also developed structured-light-based image sensors, and what makes both sensors unique is that they combine data from a number of sources to provide feedback to a robot. Servo Robot’s Robo-Pal sensors combine ultrasonic detectors for long-range detection and a structured light sources for short-range detection, and Meta-Scout’s M300 Sensor comprises multiple structured laser light sources and a miniature video camera. Both detectors are targeted at applications such as weld seam analysis where three-dimensional profiles of weld joints must be accurately determined. In an application for a hot-tub manufacturer, Robo-Pal measures the surface plane of the tub, allowing a robot to drill dimple holes perpendicular to the surface.
Large companies with experience in automated manufacturing such as Omron (Tokyo, Japan) and Siemens (Munich, Germany) are now entering the machine-vision market with smart sensors. This will surely impact the markets once dominated by smart-camera vendors. To compete, smaller companies may need to pursue more niche markets that are not so closely aligned with industrial automation.
About the Author
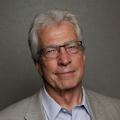
Conard Holton
Conard Holton has 25 years of science and technology editing and writing experience. He was formerly a staff member and consultant for government agencies such as the New York State Energy Research and Development Authority and the International Atomic Energy Agency, and engineering companies such as Bechtel. He joined Laser Focus World in 1997 as senior editor, becoming editor in chief of WDM Solutions, which he founded in 1999. In 2003 he joined Vision Systems Design as editor in chief, while continuing as contributing editor at Laser Focus World. Conard became editor in chief of Laser Focus World in August 2011, a role in which he served through August 2018. He then served as Editor at Large for Laser Focus World and Co-Chair of the Lasers & Photonics Marketplace Seminar from August 2018 through January 2022. He received his B.A. from the University of Pennsylvania, with additional studies at the Colorado School of Mines and Medill School of Journalism at Northwestern University.