CMOS image sensors from vendors such as Eastman Kodak (Rochester, NY), Micron Technology (Boise, ID), and Omnivision (Sunnyvale, CA) are being used in products ranging from mobile phones and security cameras to automobile lane-departure warning systems and vision-guided robots. Before these sensors and the camera modules based around them can be shipped, however, they must be tested at every stage of product development.
There are currently three approaches to testing these devices and modules. Large-volume image-sensor and camera-module manufacturers sometimes use expensive automated production test equipment from Teradyne (Boston, MA) and Agilent (Palo Alto, CA); however, it takes very large volumes to justify the high price of this approach. Smaller-volume sensor and camera-module manufacturers may simply use the evaluation boards provided by the sensor vendors, which may provide only limited evaluation functionality.
Test engineers can, of course, develop their own test systems. “Generally,” says Martin Vasey, CEO of Jova Solutions (San Francisco, CA), “these consist of off-the-shelf instruments such as frame grabbers, power supplies, oscilloscopes, custom-designed test beds, and sophisticated image-analysis algorithms to evaluate the ICs and the camera modules built around them. Developing these systems requires a high level of expertise and can take many months and cost tens of thousands of dollars.”
Jova Solutions has developed a CMOS image-sensor and camera-module test station, the Image Sensor Lab ISL-1600, that provides a range of CMOS image-sensor interfaces and control, test, evaluation, and comparison capabilities-and costs less than $5000. In essence, the ISL-1600 provides a bridge between the image sensor or camera module under test and a host PC that runs the unit’s software suite.
To interface to sensors or camera modules, a simple adaptor makes the connections between the ISL-1600 standard connector pinout to the camera module’s specific mating connector and pinout. Jova Solutions makes custom adaptors to meet customer-specific requirements. A reference adaptor template is provided so that customers can develop their own custom adapters quickly and cost-effectively.
Competitive Imaging
According to Vasey, the company has developed more than 20 test boards for semiconductor and camera vendors including Aurora Optical (Tucson, AZ), Exbiblio (Seattle, WA), and Flextronics (Singapore). These interface boards generally cost between $800 and $1500 to develop. For devices Jova has already developed, this cost can be as low as $125, says Vasey.
The ISL-1600 can be interfaced to most CMOS sensors. Since the maximum data-clock frequency of the unit is 136 MHz and data are clocked over a maximum 16-bit-wide data bus, the test unit cannot be used to test high-speed, multiple-tap image sensors. In fact, Jova Solutions is firmly targeting the CMOS imager and camera-module test market for its product.
The ISL-1600 was designed as a generic sensor interface for bit parallel devices. Jova Solutions’ Image Sensor Lab application software includes many of the common high-level characterization tests typically performed on image sensors, including photoresponse uniformity, dead- and defective-pixel detection, Macbeth color analysis, and MTF/SFR image-sharpness measurements.
“In most cases,” says Vasey, “the images generated from a CMOS sensor will be very different from those from a camera module that uses the same semiconductor device.” One of these effects, for example, is lens vignetting, or “shading”-the light fall-off observed toward the edges of an image.
One of the tests incorporated into the ISL-1600 software suite is the Bayer photoresponse uniformity algorithm. This calculates the mean and standard deviation of all the pixel intensities in the entire image, for each of the four Bayer color planes. To help eliminate lens-shading effects when using this test as a measure of the pixel noise in the image, a background-subtraction image-processing step can be selected.
Other tests include focus accuracy, spatial frequency response/modulation transfer function, dust and particle detection, and luminance uniformity. Developers of vision-related products should benefit from such a relatively low-cost testing system that helps ensure product performance.
About the Author
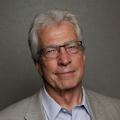
Conard Holton
Conard Holton has 25 years of science and technology editing and writing experience. He was formerly a staff member and consultant for government agencies such as the New York State Energy Research and Development Authority and the International Atomic Energy Agency, and engineering companies such as Bechtel. He joined Laser Focus World in 1997 as senior editor, becoming editor in chief of WDM Solutions, which he founded in 1999. In 2003 he joined Vision Systems Design as editor in chief, while continuing as contributing editor at Laser Focus World. Conard became editor in chief of Laser Focus World in August 2011, a role in which he served through August 2018. He then served as Editor at Large for Laser Focus World and Co-Chair of the Lasers & Photonics Marketplace Seminar from August 2018 through January 2022. He received his B.A. from the University of Pennsylvania, with additional studies at the Colorado School of Mines and Medill School of Journalism at Northwestern University.