High-speed web-inspection systems require high-resolution images to be captured by single or multiple linescan cameras that are deployed across the width of the web. With very high linescan rates, these cameras can capture images at high resolution across the transport width of the web. Because these web systems are fast, they require cameras with very high sensitivity, a parameter only now being met by high-resolution linescan-camera manufacturers.
“More than most other types of machine-vision applications, linescan applications are starved for photons,” says Mark Butler, product manager at DALSA (Waterloo, ON, Canada), “and, with line rates approximately 100 to 1000 times those of comparable frame rates of area-array camera, providing enough illumination to capture images from linescan-based cameras becomes expensive.”
Unfortunately, the tradeoff against increased responsivity of these cameras is fewer signal electrons, which results in a higher photon shot noise relative to the camera’s output. “If these trends continue,” says Butler, “the camera’s read and photon shot noise will exceed the digital detection threshold of machine-vision applications.” Therefore, many companies are turning to cameras based on time-delay-integration (TDI) architectures.
TDI cameras, however, are more difficult to set up and maintain than cameras based around single linescan devices. With this in mind, DALSA and Basler (Ahrensburg, Germany) have both developed cameras based around dual-linescan architecture, which contains two arrays of pixels.
In DALSA’s design, each array is connected to a selectable delay that either allows charge through or delays the charges by one scan line. The signal from these two arrays-one of which is delayed-are combined into a single output, effectively doubling the responsivity of the device. It also results in a twofold increase in the dynamic range of the device and decreased shot noise.
While DALSA’s dual-linescan imager uses the CCD design in its 1k- and 2k-based Spyder3 GigE cameras, Basler’s Sprint family is based on recently developed 2k and 4k CMOS imagers. “The increasing demand for speed and throughput means that finding ways to improve responsivity is becoming more and more important,” says Lars Hansen, a product manager for the Vision Components division of Basler. “Basler now has exclusive rights to a next-generation linescan sensor that combines speed and sensitivity.” One novel feature of the imager is that the sensor’s maximum allowed line rate increases linearly as the area of interest is decreased, an advantage not possible with CCD sensors.
DALSA’s offering runs at a 36 kHz line rate at 2k resolution and the CMOS-based Sprint series runs at 140 kHz with 4k resolution.
Contact sensor challenge
“Conventional linescan systems operate with a largely reduced image of the object,” says Christine Tichawa, managing director of Tichawa Vision (Friedberg, Germany). “This is why the distance between the object to be inspected and the sensor needs to be comparable to the width of the object. To capture a linescan image across a 2 ft web, for example, a linescan camera needs to be positioned approximately 2 ft above the object being inspected.”
One alternative is to use a contact image sensor (CIS) across the width of the web. However, conventional CISs are limited in machine-vision applications. In office products such as photocopiers, for example, these image sensors are placed very close to the object being imaged. Furthermore, they are not built to withstand rugged industrial environments, support high line rates, or interface to standard Camera Link or LVDS frame grabbers.
To overcome these limitations, Tichawa has introduced a series of CISs designed for the machine-vision industry that are composed of an array of linear CCD or CMOS sensors, sophisticated on-chip optics, and an embedded light source.
What makes these sensors unique is the optics. An array of graded-index lenses allow these devices to be placed at a distance of 20 mm from the web-inspection surface. Each lens in the array forms an image over a limited region and the lenses are placed so that an overlap between individual images forms a sharp overall image over a long narrow line. With these sensors, the company expects to challenge the role predominantly held by linescan cameras in web applications.
About the Author
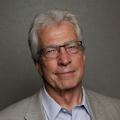
Conard Holton
Conard Holton has 25 years of science and technology editing and writing experience. He was formerly a staff member and consultant for government agencies such as the New York State Energy Research and Development Authority and the International Atomic Energy Agency, and engineering companies such as Bechtel. He joined Laser Focus World in 1997 as senior editor, becoming editor in chief of WDM Solutions, which he founded in 1999. In 2003 he joined Vision Systems Design as editor in chief, while continuing as contributing editor at Laser Focus World. Conard became editor in chief of Laser Focus World in August 2011, a role in which he served through August 2018. He then served as Editor at Large for Laser Focus World and Co-Chair of the Lasers & Photonics Marketplace Seminar from August 2018 through January 2022. He received his B.A. from the University of Pennsylvania, with additional studies at the Colorado School of Mines and Medill School of Journalism at Northwestern University.