Sometimes multiple imaging technologies can be combined to perform a new kind of compound application. This can be of particular value in the electronics industry, where the complexity, density, and cost of PCBs continues to escalate-particularly those related to embedded electronics for medical and other real-time critical systems.
Currently, most finished electronics are checked with in-circuit testing of functional blocks. However, some electronics manufacturers are moving traditionally offline nondestructive-testing systems such as x-ray, thermography, and acoustic microscopy to their production lines to achieve 100% inspection. With this trend in mind, several European companies partnered with Kaunas University of Technology (Kaunas, Lithuania) and Fraunhofer-Institut für Produktionstechnik und Automatisierung IPA (Stuttgart, Germany) to develop the Microscan PCB inspection system.
Microscan combines the three most common offline inspection technologies with automated optical inspection (AOI) to provide 100% inline inspection of populated PCBs. These technologies work with common data and material handling interfaces so that end users could pick and choose among the systems, depending on the PCB inspection requirements, or use all four systems.
As part of the EU Framework 6 CRAFT-funded program, small- to medium-size companies were chosen from across Europe to develop the imaging systems: X-Tek Systems (Tring, England) built the microfocus x-ray systems, LOT Oriel (Leatherhead, England) developed the thermal-imaging system, Machine Vision Products (Carlsbad, CA) developed the AOI systems, and Ultrasound Sciences (Aldershot, England) developed the scanning acoustic microscope.
The Microscan group developed a list of 24 of the most common defects on electronic boards, from dry joints, to solder shorts and bridges more common to the new generation of lead-free solders, to ball-grid-array (BGA) inspection, and missing or misaligned components. The defect list was matched with the most appropriate Microscan inspection systems and prioritized based on the cost to rework the board. The IPC’s Surface Mount Equipment Manufacturers Association (SMEMA) standard for electronic-boards material-handling systems was used, including electronic interface, physical dimensions, permissible conveyor height, and PCB edge clearance, to enable the systems to be connected to each other and to other PCB manufacturing equipment.
Starting with AOI
Microscan’s AOI system was designed to inspect boards after any of the three main stages of manufacture-solder paste printing, component placement, reflow oven-and provide a test bed for image-processing algorithms that would be reused on the x-ray and scanning acoustic-microscope inspection systems; the IR system has its own software. At each step, AOI systems can locate defects and designate boards for rework before additional value is added.
Camera controls and image-acquisition source code were packaged along with the Hitachi Kokusai Electric (Waltham Cross, England) KP-F120 CCD camera and Nexeon CL PCI Camera Link frame grabber from dPict Imaging (Indianapolis, IN). Camera Link provides the connection between camera and frame grabber.
The x-ray system was developed to build on the lessons of the AOI system. A microfocus electron gun housed in a vacuum chamber is aimed at a tungsten foil target to produce x-rays of varying energies between 40 to 160 kV. A digital camera is optically coupled to a phosphor screen to produce 758 × 580-pixel, 12-bit monochromatic images of an x-ray radiograph.
Shorts and delamination of PCB boards and IC packages are among the most important targets for the IR imaging system. The IR camera was a FLIR Systems (North Billerica, MA) A20, which can indicate the temperature of objects instead of producing a thermal image and is suited to process control and monitoring environment.
At the end of the Microscan system, a scanning acoustic microscope system raster scans an ultrasonic probe above each component. The Microscan system uses a column of sprayed water instead of submersing the PCB in water to enable acoustic imaging. This proprietary method reduces the chances of water being trapped between components and the PCB, and makes integration easier with the conveyor.
About the Author
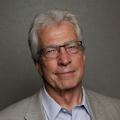
Conard Holton
Conard Holton has 25 years of science and technology editing and writing experience. He was formerly a staff member and consultant for government agencies such as the New York State Energy Research and Development Authority and the International Atomic Energy Agency, and engineering companies such as Bechtel. He joined Laser Focus World in 1997 as senior editor, becoming editor in chief of WDM Solutions, which he founded in 1999. In 2003 he joined Vision Systems Design as editor in chief, while continuing as contributing editor at Laser Focus World. Conard became editor in chief of Laser Focus World in August 2011, a role in which he served through August 2018. He then served as Editor at Large for Laser Focus World and Co-Chair of the Lasers & Photonics Marketplace Seminar from August 2018 through January 2022. He received his B.A. from the University of Pennsylvania, with additional studies at the Colorado School of Mines and Medill School of Journalism at Northwestern University.