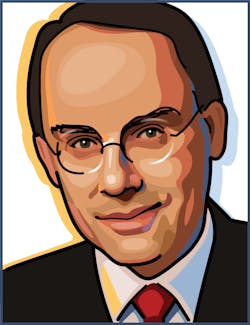
Extreme ultraviolet (EUV) lithography has been under development for more than 20 years. Among all the unsolved technological challenges the generation of appropriate light has been biggest. For a long time, there was severe doubt if the target of 250 Watts for high-volume manufacturing could ever be reached. Now it has been accomplished. How? By careful development of minute details.
Until recently it was an open question whether EUV lithography would ever make it to the industrial chip production. "The EUV source has turned out to be much more challenging than we had thought," said Stefan Wurm, director of lithography at Sematech (Albany, NY) in a 2013 LFW article. In 2014 the ASML/Cymer development team showed for the first time, that 250 Watt would be feasible. The belief in the technology became even stronger, when the Trumpf Group announced an $80 Million investment in a new factory for EUV pump lasers in 2015.
This year, ASML and Trumpf show record sales related to EUV technology. After years of substantial R&D investments industry giants such as Intel, TSMC, Samsung, Global Foundries, and IBM put EUV on their roadmap for the 7 nm node for introduction within the next two years. Samsung has fixed plans for it, while others such as Global Foundries announced to migrate to EUV when the technology is ready for volume manufacturing.
The laser system
In a recent article the ASML/Cymer team presented an overview on their work towards an EUV light source for high-volume manufacturing. They say that for a throughput of 100 wafers per hour (WPH) at a typical scanner duty cycle of 60%, the power at the wafer should be greater than about 550 mW. This means that the EUV source power provided to the exposure tool at Intermediate Focus should be greater than 200 W.
The method of choice for generating those 200 W at a wavelength of 13.5 nm is firing a CO2 laser on tiny tin droplets. The laser evaporates the tin and generates a plasma that emits incoherent radiation into a full sphere. The power at intermediate focus depicts the light behind the collection optics that is available for illuminating the semiconductor.
Challenges are numerous: Stability, debris mitigation, power scaling, conversion efficiency to name but a few. The last two were most important for reaching the HVM target of 200 W. While Trumpf has a long record for delivering kW-class CO2 lasers for cutting and welding they had to re-think their system completely for the EUV generation.
Due to a conversion efficiency of a few percent from CO2 radiation to EUV, the CO2 source must deliver more than 20 kW. The radiation is pulsed at 50 kHz to hit the ~30 µm tin droplets. Most importantly for an improved conversion efficiency, the laser has to include a special pre-pulse. After testing several different setups, the teams arrived at a 3-stage power amplification (+ pre-amplification) system in the TWINSCAN NXE:3100, shown in Figure 1.It’s the right pre-pulse that makes it
It was in the early days of laser science when people had already started to explore laser-produced plasma. And soon it became clear that a pre-pulse can significantly improve the conversion efficiency from laser light to plasma radiation. Since the 1970s scientists have been working hard on the theoretical and experimental investigation of this effect. The EUV development teams had to watch that closely, not only to get closer to the HVM target but also for the economic argument: Every percent in conversion efficiency would save the future customer millions in investments.
Figure 2 shows the impressive progress that was achieved with an evolution of pre-pulse technology. The pre-pulse evaporates the tin droplet, transforming it into a target with optimized shape and density. In fact, the target diameter has already been increased to 400 µm and the conversion efficiency went up to more than 4 percent with a disk-shaped target. At this target diameter the laser beam profile can be much better exploited than with the original droplet size, which is significantly smaller than the beam size.As the researchers report in their paper, a modified ASML NXE:3300B source demonstrated one hour dose controlled EUV power at 210 W by late 2015 and early 2016. This breakthrough result illustrated for the first time the ability of laser-based EUV technology to meet high volume manufacturing needs.
In the meantime, as the authors from ASML/Cymer say, more than 10 of their EUV sources have been used around the world, accumulating the necessary knowledge to eventually move into the HVM environment. MOPA pre-pulse technology has been validated as the path to higher power output, and stabilized power of 210 W at intermediate focus has been established. Normal-incidence collector mirrors with > 5 sr light collection and high average reflectivity are being produced in volume and are showing increasingly long lifetimes in the field. Enhanced collector protection and in-situ cleaning technologies on the NXE 3350B source are both expected to increase lifetime further. NXE 3400B sources are being installed at the customer’s facilities in 2017.
At Semicon West 2017 the ASML team claimed 250 W “rather consistently by really understanding the conversion efficiency in the source and putting the right controls in place.”
References
“Light sources for high-volume manufacturing EUV lithography: technology, performance, and power scaling”, Igor Fomenkov, David Brandt, Alex Ershov, Alexander Schafgans, Yezheng Tao, Georgiy Vaschenko, Slava Rokitski, Michael Kats, Michael Vargas, Michael Purvis, Rob Rafac, Bruno La Fontaine, Silvia De Dea, Andrew LaForge, Jayson Stewart, Steven Chang, Matthew Graham, Daniel Riggs, Ted Taylor, Mathew Abraham, Daniel Brown
Adv. Opt. Technol. 6 (3-4), 173-186 (June 2017), DOI: https://doi.org/10.1515/aot-2017-0029
About the Author
Andreas Thoss
Contributing Editor, Germany
Andreas Thoss is the Managing Director of THOSS Media (Berlin) and has many years of experience in photonics-related research, publishing, marketing, and public relations. He worked with John Wiley & Sons until 2010, when he founded THOSS Media. In 2012, he founded the scientific journal Advanced Optical Technologies. His university research focused on ultrashort and ultra-intense laser pulses, and he holds several patents.