NASA and Made in Space explore 3D printing and fiber-optic manufacturing in microgravity
The National Aeronautics and Space Administration (NASA) Optical Fiber Production in Microgravity (Made In Space Fiber Optics) investigation demonstrates the merits of manufacturing fiber-optic filaments in microgravity. The fiber-optic material chosen for this demonstration is ZBLAN. Research indicates this material has the potential for better optical qualities than the silica used in most fiber optic cable. This demonstration of the scientific and commercial merits of manufacturing exotic optical fiber in microgravity could set the stage for large-scale manufacture of high-quality fiber-optic fiber in orbit. NASA is the Sponsoring Space Agency for the project. The principal investigator is Jan Clawson from Made in Space (Moffett Field, CA).
In addition to actually creating 3D printed objects on the International Space Station (ISS), Made in Space is already working towards milestones that enable fabrication of optical fiber in space in a microgravity environment.
Commercial manufacturing of microgravity-enabled optical fiber has enormous potential, both on Earth and for space exploration. The Made In Space Fiber Optics (MIS Fiber) miniature fiber-pulling machine harnesses the unique properties of the microgravity environment to produce an optical fiber orders of magnitude better than what can be produced on Earth.
When produced in a strong gravitational environment, such as Earth, exotic optical fiber is subject to tiny flaws. These crystals appear in the fiber and significantly increase signal loss. When considering data transmission lines such as long-haul communication lines that can span thousands of miles, these flaws cause large enough attenuation of the transmitted light to make the system commercially infeasible. In space, ZBLAN optical fiber can be produced without these crystals, providing superior data transmission capabilities compared to both Earth-produced ZBLAN and traditional silica fiber-optic lines. This microgravity-produced fiber has numerous applications, including transatlantic telecommunications, high-speed internet, lasers, as well as enhancing technologies in space.
Through privately funded, multi-year internal research and development work, Made In Space (MIS) has developed the expertise to successfully produce large quantities of high-grade optical fiber. MIS is partnered with Thorlabs, provider of ZBLAN preforms and production of the material for terrestrial uses, to rapidly industrialize production of optical fiber in space.
MIS will pull at least 100 meters of ZBLAN in microgravity, via a cooperative agreement with the Center for Advancement of Science in Space (CASIS). See the Made in Space blog for actual updates.
SOURCE: NASA and Made in Space; https://www.nasa.gov/mission_pages/station/research/experiments/2421.html and http://madeinspace.us/mis-fiber/
About the Author
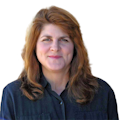
Gail Overton
Senior Editor (2004-2020)
Gail has more than 30 years of engineering, marketing, product management, and editorial experience in the photonics and optical communications industry. Before joining the staff at Laser Focus World in 2004, she held many product management and product marketing roles in the fiber-optics industry, most notably at Hughes (El Segundo, CA), GTE Labs (Waltham, MA), Corning (Corning, NY), Photon Kinetics (Beaverton, OR), and Newport Corporation (Irvine, CA). During her marketing career, Gail published articles in WDM Solutions and Sensors magazine and traveled internationally to conduct product and sales training. Gail received her BS degree in physics, with an emphasis in optics, from San Diego State University in San Diego, CA in May 1986.