LASSOS ground sensor from MIT Lincoln Laboratory finds origin of laser aircraft strikes (see video)
Although perpetrators of laser strikes can be punished by federal, state, and local laws in the United States, lack of accurate and timely information for law-enforcement officials means less than 1% of perpetrators are ever caught. It is difficult for pilots to see where a laser beam is coming from, and even more difficult for police officers to pinpoint the perpetrator's location based on the pilot's report. Certain military aircraft are equipped with sensors that can estimate perpetrators' geographic location (geolocation), but it is costly and unrealistic to have them installed on every airplane.
RELATED ARTICLE: MetaAir metamaterial film protects pilots from cockpit laser strikes
To address the present lack of effective laser strike mitigation systems, the Laser Technology and Applications and Air Traffic Control Systems Groups at MIT Lincoln Laboratory have teamed up to develop the Laser Aircraft Strike Suppression Optical System (LASSOS). LASSOS is a ground-based sensor system that can accurately identify the probable location of a perpetrator of a laser strike and immediately notify law enforcement (see video below):
"These sensors can provide persistent, automated protection for a high-risk volume of airspace, such as a final approach path, by quickly locating the origin of a laser strike and transmitting the coordinates to local law enforcement. This technology will enable law enforcement to launch a rapid and targeted response to a laser strike event, greatly increasing their chance of apprehending and prosecuting perpetrators," said Tom Reynolds, a member of the development team and the associate leader of the Air Traffic Control Systems Group.
The system works by capturing side-scattered laser light and tracing it back to the perpetrator's location. When a laser is shone into the sky, a small fraction of the light is scattered by air molecules and aerosols, forming a residual streak in the laser's path. Two or more high-sensitivity, low-noise charge-coupled device cameras image the scattered light from different vantage points, providing the geometric diversity needed to digitally reconstruct the laser streak in three dimensions. The geographic coordinates of the laser's origin are calculated by tracing the laser streak down to a topographically accurate model of the Earth's surface.
A feature of LASSOS that makes it particularly effective is its integration with Google Earth. As soon as a laser is detected by the cameras, a digital reconstruction of the streak appears on a Google Earth map in real-time. This image summarizes the detection event, depicting the laser's point-of-origin and most probable path through the night sky. Within 30 seconds of the image being captured, LASSOS provides nearby members of law enforcement with the perpetrator's GPS coordinates, nearest address, and the time of the incident. This information allows officers to rapidly intervene.
The system prototype has already demonstrated its speed and accuracy in several tests. For one test trial, LASSOS's geolocation ability was tested at a distance of nine nautical miles to simulate the typical length of a final approach path when an aircraft is most vulnerable to lasing. One sensor was placed on top of the B Building at Lincoln Laboratory and another on the Flight Test Facility at Hanscom Air Force Base. Testers shone high-power laser beams (of the type used during lasing events) from a baseball field nine nautical miles away in Tewksbury, Massachusetts, and were geolocated by LASSOS in less than 30 seconds. The system was so accurate that it could distinguish whether the laser beams came from first, second, or third base on the field.
SOURCE: MIT Lincoln Laboratory; https://www.ll.mit.edu/news/LASSOS.html
About the Author
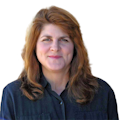
Gail Overton
Senior Editor (2004-2020)
Gail has more than 30 years of engineering, marketing, product management, and editorial experience in the photonics and optical communications industry. Before joining the staff at Laser Focus World in 2004, she held many product management and product marketing roles in the fiber-optics industry, most notably at Hughes (El Segundo, CA), GTE Labs (Waltham, MA), Corning (Corning, NY), Photon Kinetics (Beaverton, OR), and Newport Corporation (Irvine, CA). During her marketing career, Gail published articles in WDM Solutions and Sensors magazine and traveled internationally to conduct product and sales training. Gail received her BS degree in physics, with an emphasis in optics, from San Diego State University in San Diego, CA in May 1986.