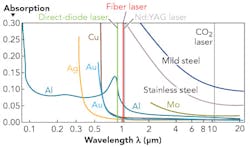
FRANCISCO VILLARREAL SAUCEDO, BIEN CHANN, BRYCE SAMSON, and PARVIZ TAYEBATI
Recent interest in using direct-diode lasers rather than fiber or CO2 lasers is largely enabled by improvements in performance that now allow high-speed diode laser cutting of all relevant industrial metals. The combination of higher wall plug efficiency, together with improved reliability and ease of servicing, have long made direct-diode lasers the holy grail of laser materials processing companies, attracted also by the lower cost of manufacturing. This article shows the benefits over alternative lasers, with direct-diode lasers outperforming fiber lasers in cutting speed in many thin materials, particularly aluminum, and now meeting the cutting quality in thicker materials—the last realm of CO2 metal cutting systems. Recent product launches by system integrators are now validating these performance enhancements.
Cutting speed improvements
The move from CO2 lasers to fiber lasers in the last 10 years is primarily because of the improvement in cutting speed—often 2–3 times faster than what CO2 lasers can achieve at the same power level [1]. This can be readily explained by the higher beam absorption in most metals associated with the 1.08μm wavelength, as compared with 10.6μm for the CO2 laser (FIGURE 1).Cutting of highly reflective materials is also improved in direct-diode laser systems, aided by the reduced sensitivity to back-reflection intrinsic to these lasers. Indeed, this is a particular problem associated with fiber lasers, where the ytterbium-doped fiber is traditionally very sensitive to back-reflection and typically requires sensors to protect the laser from damage. Overall, this makes processing of copper, brass, and other reflective materials possible, but somewhat restricted with fiber lasers. In the case of direct-diode lasers, we have processed copper with N2 (rather than O2) without back-reflection issues, therefore enabling an additional process for the end user that significantly enhances the surface finish by producing an oxide-free edge for laser cutting of copper.
Cut quality improvements
The relative difficulty of getting good cut quality using a fiber laser when processing thick metals has been widely reported, and for this reason the technology is mostly associated with cutting speed improvements. Indeed, for many integrators, the continuation of CO2 product lines is primarily to satisfy end-user demand for processing thicker materials with better surface quality than can be obtained with fiber laser-based systems. Our studies with direct-diode lasers and those detailed by others have found the tendency for lower surface roughness from the direct-diode laser-based cutting system-most prominent when processing thicker metals. This was also highlighted by M. Wood [2], where the surface roughness comparison between CO2 and direct-diode laser cutting mild steel up to 4mm using with 2kW is shown (FIGURE 5). In this case, we attribute the enhancement in quality to the improved stability from the direct-diode laser source, which is a feature of direct-diode lasers in general when compared with alternative laser technologies.In our experience, the dominant factor in surface roughness with thick metal cutting is the beam quality of the laser source, which needs to be matched to the application for the best cut quality and optimum speed. However, unlike fiber laser technology that typically is limited to switching beam quality between two modes in a digital fashion (either high or low beam parameter product [BPP]), our work indicates that the optimum BPP is a continuously variable function that depends on material and thickness [4]. Previously, we highlighted a 50% improvement in cutting speed without affecting cut quality by optimizing the BPP from 4mm-mrad to 10mm-mrad in stainless steel cutting [5].
In FIGURE 6, we highlight the cut quality improvements obtained by optimizing the BPP from the laser source up to 20mm-mrad, which is readily achieved in direct-diode laser systems with variable BPP option [7]. In mild steel, we see a reduction in surface roughness consistently for thicker mild steel samples by a factor of almost two in samples measuring 16–25mm when the BPP is changed from 10 to 20. This continuous variable BPP function is not typically available with fiber laser systems, where the control of the beam is typically dictated by the fiber and the BPP is modified by switching between waveguides—for example, the Corelase ARM product line [6]. In direct-diode laser systems, the full range of BPP between 4 and 20 is available to the end user in real time, allowing optimization of speed and quality for a range of materials. Together with the availability of 6 and 8kW direct-diode laser systems with excellent beam quality, the majority of the metal cutting market is now covered by commercially available direct-diode lasers and should help speed up adoption.
Conclusion
The combination of higher wall plug efficiency, together with improved reliability and ease of servicing, have long made direct-diode lasers the holy grail for laser materials processing companies that are also attracted to lower manufacturing cost. The latest innovations in direct-diode lasers now enable direct-diode laser systems to cut metals directly rather than use diodes as the pump source for more complex and costly fiber or disk lasers. The first set of comparisons over the last year by several groups show that direct-diode laser systems perform favorably when compared with more-established fiber and CO2 lasers, and in some cases far exceed the performance because of the more favorable wavelength. Enhancements in cutting speed, improved cut quality for thick materials, and variable BPP options differentiate the technology, and offer real process improvements in end-user applications. We expect that further studies in the near future will enhance the findings of these early studies.
REFERENCES
1. D. Larcombe, "Fiber versus CO2 laser cutting," Industrial Laser Solutions (Nov/Dec 2013).
2. M. Wood, "Laser beam technology development and application," 7th Alta Brillanza Workshop, Milan, Italy (Sept. 2015).
3. M. Sbetti et al., "Performance and efficiency of an industrial direct diode source with an extremely low BPP in laser cutting of Fe-based and reflective alloys," 7th Alta Brillanza Workshop, Milan, Italy (Sept. 2015).
4. F. Villarreal et al., "High brightness multi-kilowatt direct diode laser using wavelength beam combining," Fabtech 2015, Chicago, IL (2015).
5. B. Samson et al., "Direct benefits of DDL," Shop Floor Lasers (Dec. 2015).
6. See www.corelase.com.
7. See www.teradiode.com.
FRANCISCO VILLARREAL SAUCEDO, BIEN CHANN, BRYCE SAMSON ([email protected]), and PARVIZ TAYEBATI are with TeraDiode, Wilmington, MA, www.teradiode.com.