Photonics Products: Laser Scanning: Polygon beam scanners enable essential applications
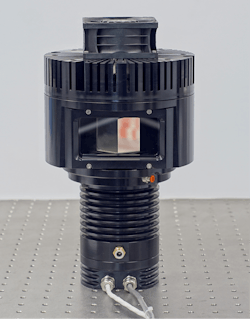
Laser scanning systems have many uses, ranging from 2D and 3D printing to materials processing, lidar, and others. Scanning a laser beam is almost always accomplished by reflecting it off one or more moving mirrors. For example, one approach is to use one or more oscillating galvanometer (galvo) mirrors, which can allow arbitrary control of the beam position in one or two dimensions.
However, if what is needed is a repeated linear scan (or, with slow movement of a stage or second mirror in a perpendicular direction, a 2D raster scan), nothing beats a rotating polygon mirror for simplicity, as there is no oscillatory element with its more-complex control system needed to create linear scans. In combination with an f-theta lens, which translates the constant-angular-velocity scan of a polygon mirror to a constant-linear-velocity scan at the work surface, a polygon mirror (and its associated motor) can straightforwardly produce a highly accurate scan. Following are some commercial examples of the art.
Aerostatic-bearing rotary spindle technology
Glenn Stutz, engineering leader for Cambridge Technology Lincoln Laser products (Phoenix, AZ), gives a background on the polygon-mirror-based laser-beam delivery systems produced by the company, and the design, fabrication, and use of polygon mirrors in general.
"These mirrors are typically fabricated from aluminum using single-point diamond machining technology to create the optical facets," he says. "In some applications, beryllium may be used to address ultrahigh-speed distortion. Post-machining, thin-film metal, and/or dielectric coatings are often applied to the mirror facets in order to 'tune' mirror performance to the specific application."
Within the scanner assembly, the polygonal mirror is rotated via a brushless DC electric motor, and is supported by a ball bearing or an air-bearing rotary spindle, Stutz explains. The mirror spindle is designed and manufactured to tight tolerances, ensuring smooth rotational operation that minimizes distortions within the reflected laser beam. "Brushless DC drive motors, designed to produce low cogging torques, enable polygonal scanners to operate smoothly at speeds ranging from a few rpm (revolutions per minute) up to speeds in excess of 55,000 rpm," he adds.
Polygonal scanners can be found in many varied applications, including medical applications such as skin treatment and retinal scanning. Other uses are in printing, marking and coding, metrology, material processing, additive manufacturing technologies, agricultural sorting, and lidar.
Several applications are currently driving scanning speeds at ever-increasing rates for use in future generations of medical and industrial laser tools. "Unfortunately, ball bearing performance drops to unacceptable levels in many of these high-speed applications," Stutz says. "For smaller mirrors, aerodynamic-bearing rotary spindle technology can be employed for operation at speeds up to 55,000 rpm, but until recently no options have been available for high-speed use with larger mirrors. To address these emerging demands, aerostatic-bearing rotary spindle technology has been developed to meet the payload requirements of larger mirrors at increased rotational velocities."
Aerostatic-bearing rotary spindle technology incorporates a rotating shaft as opposed to a rotating sleeve commonly used in aerodynamic bearings. This aerostatic stationary sleeve design has two rows of air jets positioned along the bearing surface to optimize support, and contains aerodynamic features to mitigate damage in the event of bearing pressure loss during operation. To achieve the highest rotational speeds, the scanner's optical chamber is enclosed and partially evacuated with an eductor vacuum generation system utilizing the aerostatic bearing air pressure source (see Fig. 1).
"This aerostatic bearing design has been successfully tested for speeds up to 40,000 rpm with a mirror mass up to 500 g and can be operated bidirectionally in any orientation," Stutz says.
Polygon scanners for materials processing
While galvo mirrors are widely used in materials processing to guide the beam, George Helser, president of Precision Laser Scanning (Scottsdale, AZ), notes that the lasers used in some materials-processing applications have become so powerful or operate at so high a pulse rate that traditional galvo scanners are not fast enough to utilize the full potential of the lasers.
"The original mass market for polygon scanners was laser printers back in the 1970s," Helser says. "Polygon scanners are the fast x-axis component of a raster scan, but the requirements of a laser printer are much different than for materials processing. Our polygon scanners for materials processing have a large aperture so a large spot may be focused to a small, intense point on the target."
Helser adds that powerful motors spin the large-aperture polygon mirrors to 10,000 rpm, equivalent to hundreds of meters per second linear speed. (Note: the company also makes small low-noise polygon scanners that operate up to 70,000 rpm.) "Polygon scanners are most efficient in high-pixel-density applications such as patterning with large-area removal, surface treatment, cleaning, and paint stripping," he explains. "The features of large aperture and high rpm are also needed in non-materials-processing applications such as inspection and lidar."
The Eagle Eye, the company's most popular polygon scanner for materials processing, has a 21 mm aperture—a large-enough facet for nearly all applications, Helser says (see Fig. 2). The controller uses a sine-wave drive rather than the traditional trapezoid drive. "The sine-wave drive has less EMI (electromagnetic interference), but more important is its ability to provide very smooth rotation over a very wide speed range," he explains. "A 10:1 speed range is standard, but 20:1 is optional. In most embedded applications, a polygon scanner has one operating speed and is operated with a TTL (transistor-transistor logic) interface. In materials processing, the operating speed is dictated by the process. Some materials require a relatively low scan speed, while others need a high scan speed. The Eagle Eye advanced controller has USB and RS-232 interfaces so a high-level system can easily control the polygon."Galvanometer scanners require an absolute encoder to be accurate, Helser notes, while polygon scanners require a start-of-scan (SOS) detector to be accurate. An SOS detection system for a laser printer is not going to work well in a polygon scan head because of interference from the bright working beam, he notes, adding that Precision Laser Scanning has developed an SOS kit that solves the problems of SOS detection in a materials-processing system. It combines a small, low-power red laser that does not require focusing with a compact SOS detector board that includes a light tube baffle to block stray light, and an optional filter that passes only the SOS beam. Because a polygon scan head is likely to warm up when operating with a high-power laser, the detector on the SOS board is a bi-cell detector that eliminates drift because of heating.
"It is difficult to provide a one-size-fits-all polygon scan head," Helser says. "Galvo scanners are very versatile in that they have a variable scan angle. Polygon scanners are much faster, but have a fixed scan angle primarily determined by the number of facets. Sophisticated OEMs and systems integrators add value by building their own scan heads. Many engineers know how to design a galvo scan head, but high-speed polygon scanning technology is completely foreign to them. Precision Laser Scanning not only supplies polygon scanners with advanced controllers and SOS kits, it can supply other needed optics, beam shaping, and know-how to assist those who wish to build their own polygon scan head."
As for getting 2D coverage for materials processing, Helser notes that polygon scan heads may include a galvanometer for the slower y-axis, which gives an x-y raster scan on a stationery target. However, the fastest implementation of polygon scanners is to use the polygon for the fast x-axis and a moving web or conveyor for the y-axis. "This continuous motion allows greater throughput," he says. "The motion of the target will create a skewed scan line, but that can be compensated for by mounting the polygon scan head skewed relative to the motion of the target."
High-speed scanner for line-by-line processing
In 2009, it became evident to the Dutch/Belgian startup Next Scan Technology (NST; Evergem, Belgium) that economically viable ultrashort-pulsed laser (USP) micromachining would require high-average-power lasers and very high-speed scanning systems, says Lars Penning, the company's CEO and cofounder. The founders of NST realized that well-established technology in demanding industries such as high-performance laser printing could be adapted to the needs of this new laser materials processing market.
Penning says that at the LASER World of PHOTONICS 2011 show in Munich, Germany, NST was the first to introduce a polygon-based scanner system compatible with high-power USP lasers. Since the end of 2015, NST has been associated with galvo-scanning-system maker Scanlab (Puchheim, Germany), which has concentrated its polygon-scanner know-how at the NST site in Evergem.
To achieve industrial-scale productivity, USP lasers are best combined with ultrafast scanners-for example, a polygon scanner, Penning explains (see Fig. 3). "Polygon scanners are particularly advantageous for line-oriented full-surface processing of workpieces at fine resolutions and with freely definable patterns and structures," he says. "Thanks to the high speed, these systems can considerably slash materials-processing times. USP laser processing applications range from structuring touchscreen surfaces or solar cells, to microdrilling and processing of electronic components, glass and plastics, as well as sensor and wafer manufacturing."Refractive f-theta optics vs. mirror f-theta optics
Ultraprecise micromachining requires small focused spot sizes and a full telecentric field of view-that is, a constant round spot size over the complete scan area. To focus to a small spot, Penning says, f-theta optics are required. However, traditional refractive optics using lenses are limited in size because of the progressive cost increase as the laser area becomes larger. This means cost-efficient, highly accurate laser scan heads with refractive f-theta optics have a limited scan field.
"Processing large-area ultraprecise work by traditional f-theta optics requires a step-and-repeat or multiplexing approach," Penning notes. "This approach introduces challenges on stitching (overlap of different scan jobs). To solve stitching, there is a need for accurate feedback of positioning errors and controls for active correction. Such technology requires a higher level of investments, and challenges production yields if it is not working accurately and reliably enough."
An alternative solution to avoid stitching is using wide-field mirror optics. "The core technology of NST is a polygon scanner system with patented and integrated f-theta mirror optics," Penning says. "The polygon scanner system addresses a full telecentric scan field with a 170 mm scan width. Last year, a scan head with a full telecentric scan field of 300 mm was introduced; compared to traditional f-theta optics, this increase in scan field is a factor of 4 to 5 larger. Such a large view eliminates stitching. In addition, NST has developed a high-numerical-aperture version (LSE170HNA) to enable smaller spot sizes."
Mass-produced scanners
Mass-producing compact motor-polygon assemblies is the forte of Nidec Copal Electronics (Tokyo, Japan), according to Toshiaki Doi, president of Nidec Copal Electronic's American branch (Torrance, CA). The company has produced millions of compact and low-cost polygon scanners for various industries, including manufacturing, industrial, and biomedical markets. They can be used for process control in manufacturing, materials processing for semiconductor production, 3D printers, lidar, and many more applications (see Fig. 4).Using Nidec's aerodynamic-bearings technology, the model PTC30ERG can provide rotation speeds of up to 33,000 rpm while maintaining a small profile and low cost, Doi says, adding that the polygon mirror's high reflectivity, even at incidence angles of more than 30°, is well suited for high-speed 3D printing. He also notes that the model PD60EA can provide a rotation speed of up to 5000 rpm while carrying a high-resolution, large-aperture polygon mirror that can be used for long-range lidar performance.
"Nidec Copal Electronics has designed miniaturized control boards using specialized ICs for running polygon scanners," Doi says. "By reducing the number of discrete components, we managed to reduce the cost, size, and power consumption per unit." As an example, he describes custom compact motors that can spin the PTC30ERG at speeds of up to 55,000 rpm, compared to classical ball-bearing motors that are limited to 10,000 rpm. The motors are also built right onto the control board, saving space and cost. "However, ball-bearing motors are also available for carrying large-aperture polygons for mobile applications," he adds.
"The hot markets today for compact polygon scanners are lidar for autonomous vehicles and high-speed scanning for 3D printers," Doi says. "In autonomous vehicles, several different types of sensors may be employed; however, lidar is the main component in object detection. A typical lidar can image in 3D despite total darkness or fog, contrary to a camera or RF (radio-frequency) radar that would suffer from resolution limitations."
The initial 3D printer market was based primarily on slower galvanometer scanners, while newer 3D printers require the use of faster raster scanners, Doi explains. With the increasing shift in 3D printer technology from conventional extrusion-based printing methods like fused-deposit modeling (FDM) to resin, or powder-based printing such as stereolithography and selective laser sintering (SLS), the use of laser technology has become crucial. "Polygon laser scanners can meet and exceed the demands for future faster and more accurate 3D printers," he says.
Many materials
Types of polygon mirrors produced by II-VI Infrared (Saxonburg, PA) include prismatic (all mirror surfaces parallel to the axis of rotation), pyramidal (all mirror surfaces taking the same angle with respect to the axis of rotation), and irregular. An irregular polygon mirror enables the production of scan lines in two or more positions as the polygon mirror rotates (see Fig. 5).In addition to aluminum, the company produces polygon mirrors made of many other materials, including silicon, germanium, the infrared materials zinc selenide and zinc sulfide, copper, and even plastics. Mirror surfaces can be nickel-plated if desired. Uses include bar-code reading, paint stripping, 3D printing, transponders, and advanced driver-assistance systems and lidar.
For More Information
Companies mentioned in this article include:
Cambridge Technology Lincoln Laser
Phoenix, AZ
www.cambridgetechnology.com
II-VI Infrared
Saxonburg, PA
www.iiviinfrared.com
Next Scan Technology/Scanlab
Evergem, Belgium
http://nextscantechnology.com
Nidec Copal Electronics
Tokyo, Japan
www.nidec-copal-electronics.com
Precision Laser Scanning
Scottsdale, AZ
http://precisionlaserscanning.com
DISCLAIMER: While we try to include information from the broadest possible number of companies that manufacture the products featured in our Photonics Products series, because of limited word count as well as deadlines that cannot always be met by requested contributors, we cannot possibly include all companies and regret if your company is not included in our series.
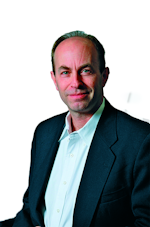
John Wallace | Senior Technical Editor (1998-2022)
John Wallace was with Laser Focus World for nearly 25 years, retiring in late June 2022. He obtained a bachelor's degree in mechanical engineering and physics at Rutgers University and a master's in optical engineering at the University of Rochester. Before becoming an editor, John worked as an engineer at RCA, Exxon, Eastman Kodak, and GCA Corporation.