Nanoengineers in Jonathan Claussen’s lab at Iowa State University (Ames, IA) are finding ways to use graphene and its amazing properties in their sensors and other technologies. Just an atom thick, the carbon honeycomb is great at conducting electricity and heat and is both strong and chemically stable. But researchers have struggled to move beyond tiny lab samples for studying its material properties to larger pieces for real-world applications.
RELATED ARTICLE: University at Buffalo researchers lead 'frozen' synthesis of 3D graphene
Recent projects that used inkjet printers to print multilayer graphene circuits and electrodes had the engineers thinking about using it for flexible, wearable and low-cost electronics. But there are problems with the existing technology. Once printed, the graphene has to be treated to improve electrical conductivity and device performance, usually with high temperatures or chemicals that degrade flexible or disposable printing surfaces such as plastic films or even paper.
Suprem Das, an Iowa State postdoctoral research associate in mechanical engineering and an associate of the U.S. Department of Energy's Ames Laboratory, and Claussen came up with the idea of using lasers to treat the graphene. Claussen, an Iowa State assistant professor of mechanical engineering and an Ames Laboratory associate, worked with Gary Cheng, an associate professor at Purdue University’s School of Industrial Engineering, to develop and test the idea.
They found treating inkjet-printed, multilayer graphene electric circuits and electrodes with a pulsed-laser process improves electrical conductivity without damaging paper, polymers or other sensitive materials. The work is described in the journal Nanoscale; Claussen and Cheng are lead authors and Das is first author.
"The breakthrough of this project is transforming the inkjet-printed graphene into a conductive material capable of being used in new applications," Claussen said. Those applications could include sensors with biological applications, energy storage systems, electrical conducting components, and even paper-based electronics.
To make all that possible, the engineers developed computer-controlled laser technology that selectively irradiates inkjet-printed graphene oxide. The treatment removes ink binders and reduces graphene oxide to graphene, physically stitching together millions of tiny graphene flakes. The process makes electrical conductivity more than a thousand times better. "The laser works with a rapid pulse of high-energy photons that do not destroy the graphene or the substrate," Das said. "They heat locally. They bombard locally. They process locally."
That localized, laser processing also changes the shape and structure of the printed graphene from a flat surface to one with raised, 3D nanostructures. The engineers say the 3D structures are like tiny petals rising from the surface. The rough and ridged structure increases the electrochemical reactivity of the graphene, making it useful for chemical and biological sensors.
"This work paves the way for not only paper-based electronics with graphene circuits," the researchers wrote in their paper, "it enables the creation of low-cost and disposable graphene-based electrochemical electrodes for myriad applications including sensors, biosensors, fuel cells and (medical) devices."
SOURCE: Iowa State University; http://www.news.iastate.edu/news/2016/09/01/paperelectronics
About the Author
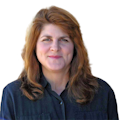
Gail Overton
Senior Editor (2004-2020)
Gail has more than 30 years of engineering, marketing, product management, and editorial experience in the photonics and optical communications industry. Before joining the staff at Laser Focus World in 2004, she held many product management and product marketing roles in the fiber-optics industry, most notably at Hughes (El Segundo, CA), GTE Labs (Waltham, MA), Corning (Corning, NY), Photon Kinetics (Beaverton, OR), and Newport Corporation (Irvine, CA). During her marketing career, Gail published articles in WDM Solutions and Sensors magazine and traveled internationally to conduct product and sales training. Gail received her BS degree in physics, with an emphasis in optics, from San Diego State University in San Diego, CA in May 1986.