Imaging performance test method from NIST uses realistic hyperspectral scenes
Gaithersburg, MD--Scientists and engineers developing imaging instruments and cameras face a daunting task when evaluating the imaging performance of these devices. In response, the National Institute of Standards and Technology (NIST) has developed the Hyperspectral Image Projector, or HIP, to enable performance evaluation of cameras and other imaging instruments using realistic scenes. The purpose of HIP is to project hyperspectral images into sensors, simulating realistic scenes both spectrally and spatially, for performance testing and evaluation of the sensor instruments in the laboratory. For example, NIST says that using HIP to test satellite-sensor performance in a controlled laboratory setting alleviates expensive field testing, allow better separation of environmental effects from instrument effects, and enables system-level performance testing and validation of space-flight instruments prior to launch.
The HIP system's design is similar to commercially available digital light processing (DLP) projection systems in which the projected image is made from a composite of grayscale images representing each of the RGB colors. The individual grayscale images are generated by focusing light through a rotating multicolored filter to obtain the spectral component and illuminating a digital micromirror device to obtain the spatial component. When the grayscale images are projected and combined at typical video frame rates, the result is a full RGB color image.
In contrast to the DLP system, the HIP system can project composites of numerous spectra. Instead of using a filter, the HIP system's spectral components are generated with a spectral engine composed of dispersive optics and a spatial light modulator such as a digital micromirror device or a liquid-crystal spatial light modulator. The spatial engine, composed of a second spatial light modulator, then determines the spatial component for each spectral component. Synchronized operation of both engines ensures that each spectral component is projected sequentially in the correct proportions in each spatial region to create a time-averaged hyperspectral image.
The advantage of the HIP system is not only its ability to project realistic, spectrally, and spatially complex scenes, but also the user's ability to arbitrarily define and control the spectral distributions at each spatial image pixel. For example, the HIP can alter certain spectral components to reflect changing scenes. This means that HIP can be used to test imagers under a wide range of conditions and for a variety of applications.
In a recent demonstration of the HIP process, an image of a coral reef acquired by an airborne hyperspectral sensor was deconvolved into six spectral components and then re-projected using the HIP into a laboratory imaging spectrometer (see image). This produced an RGB version of the original image and the HIP-projected image. The NIST research, performed with the HIP operating in the visible spectrum, served to prove the concept. NIST and its collaborators are continuing to develop the HIP by extending the spectral range into the IR and UV, increasing the spectral resolution and brightness, and enabling the showing of dynamic scenes such as hyperspectral image movies.
SOURCE: SPIE Newsroom; http://spie.org/x57013.xml?ArticleID=x57013
About the Author
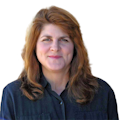
Gail Overton
Senior Editor (2004-2020)
Gail has more than 30 years of engineering, marketing, product management, and editorial experience in the photonics and optical communications industry. Before joining the staff at Laser Focus World in 2004, she held many product management and product marketing roles in the fiber-optics industry, most notably at Hughes (El Segundo, CA), GTE Labs (Waltham, MA), Corning (Corning, NY), Photon Kinetics (Beaverton, OR), and Newport Corporation (Irvine, CA). During her marketing career, Gail published articles in WDM Solutions and Sensors magazine and traveled internationally to conduct product and sales training. Gail received her BS degree in physics, with an emphasis in optics, from San Diego State University in San Diego, CA in May 1986.