Photonic-bandgap Fibers: Propagation time through this fiber has zero sensitivity to temperature change
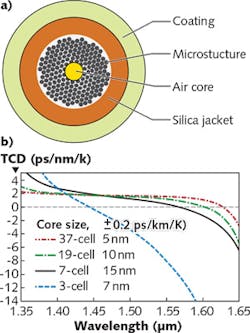
Single-mode optical fibers serve science and industry wherever there is a need to flexibly route light over short or long distances while maintaining a beam with diffraction-limited beam quality, and without any lateral spreading. Some examples include high-speed data transmission, fiber sensing in harsh environments, and quantum communications. Active devices relying on single-mode fiber include many fiber lasers and amplifiers.
For some applications, such as carrying precisely timed signals for synchronization of, for example, optical clocks, variations in timing of pulses traveling through a single-mode fiber because of environmental influences such as temperature are unwanted. This sensitivity of propagation time to temperature variation, also called thermal coefficient of delay (TCD), which is caused by elongation of the fiber and change in refractive index as a function of temperature, is most pronounced in solid-core fiber, and is greatly reduced in hollow-core photonic-bandgap fiber (HC-PBGF). As a result, the latter type of fiber is used in many critical timing-based experiments. However, even HC-PBGF has a residual thermal sensitivity.
Counterbalanced thermal effects
A group of researchers from the Optoelectronics Research Centre (University of Southampton; Southampton, England) has now gone the extra distance and created an optical fiber that has zero thermal sensitivity (TCD).1 In fact, they have theoretically and experimentally demonstrated not just this, but also the design of fibers with a negative TCD.
The achievement takes advantage of optical properties unique to HC-PBGFs, in which the mode group index can be made to decrease, and thus the speed of light in the fiber to increase, as the fiber lengthens with temperature. When done right, the thermal effects and the change in mode group index balance each other out, resulting in complete temperature insensitivity.
As temperature increases and the glass refractive index increases, the fiber microstructure expands in size as well, changing the microstructure's grating period. It is the latter effect that can be optimized to counterbalance the normal thermal sensitivity, at least at a certain wavelength (and, given a realistic tolerance on TCD of ±0.2 ps∕km∕K, over a finite wavelength band of a few nanometers).
The researchers also calculated these fibers' sensitivity to manufacturing tolerances. For example, for a seven-core fiber design (which was later used in experiments), calculations showed that a 1% change in the fiber core diameter (a reasonable number, the researchers say) for single-mode operation would cause a zero-TCD wavelength shift of about 1 nm with a negligible contribution to a TCD of within ±0.2 ps∕km∕K (see figure). Additional calculations showed that negligible changes to TCD were caused by coiling the seven-core fiber to a 5-cm diameter.
For the experiment, a 2.8-m-long section of seven-core fiber was chosen with a 0.965 air-filling fraction, a 13.6 μm core diameter, a 9.7 μm 1/e2 mode-field diameter, and an attenuation below 10 dB/km. Delay was measured at temperatures of 29°, 47°, 65°, and 82°C. At a wavelength of 1531 nm, the delay was insensitive to change in temperature (TCD = 0), and the optical bandwidth in which the TCF fell within ±0.2 ps∕km∕K was 11 nm.
The researchers note that the fiber is 10X less temperature-sensitive than other HC-PBGFs, and is almost 200X less sensitive than standard solid-core fibers over an 11 nm bandwidth. In addition, over a 2 nm bandwidth, the new fiber has a thermal sensitivity 1000X more than standard solid-core single-mode fiber.
The group aims to optimize two further parameters: first, to align the wavelength where TCD is zero with the wavelength of maximum transmission, and second, to reduce the dispersion slope to widen the bandwidth over which the TCD falls within the ±0.2 ps∕km∕K range.
REFERENCE
1. E. N. Fokoua et al., Optica (2017); https://doi.org/10.1364/optica.4.000659.
About the Author
John Wallace
Senior Technical Editor (1998-2022)
John Wallace was with Laser Focus World for nearly 25 years, retiring in late June 2022. He obtained a bachelor's degree in mechanical engineering and physics at Rutgers University and a master's in optical engineering at the University of Rochester. Before becoming an editor, John worked as an engineer at RCA, Exxon, Eastman Kodak, and GCA Corporation.