LITHOGRAPHY: Pre-pulse technology scales EUV source power
Production-ready extreme ultraviolet (EUV) lithography technology depends on a high-efficiency, high-power source of 250 W in order to meet 22 nm and smaller semiconductor node requirements. To reach this power level, Cymer (San Diego, CA) is implementing its pre-pulse technology to achieve a 2X improvement in the conversion efficiency (CE) between the carbon-dioxide (CO2) drive laser and the resultant EUV source power output.
LPP source architecture
Laser-produced-plasma (LPP) source architectures are being advanced to scale EUV power output to the levels needed for high-volume semiconductor manufacturing using EUV lithography. High-power sources enable the level of throughput needed for cost-effective operation—even for high-performance photoresists that require high-dose exposures for optimum imaging.
In an LPP source, pulses of high power CO2 light are focused onto small, molten tin droplets, heating the tin to create a very high temperature, highly ionized plasma that emits light over a broad range of wavelengths. The 13.5 nm light of interest for EUV lithography is collected by a large ellipsoidal, multilayer mirror and directed to an intermediate focus point at the interface with the lithography exposure tool.
The mirror is a highly polished substrate with a silicon/molybdenum multilayer coating for selecting 13.5 nm radiation, and is protected by a capping layer to prevent erosion by energetic ions from the tin plasma. It is important to maintain high reflectivity of the mirror in order to obtain maximum collection efficiency. Hydrogen gas is used as the primary technique for mitigation of residual tin debris that can contaminate or damage the mirror surface.
Another key factor in eliminating contamination is to minimize the size of tin droplets so that the initial quantity of tin debris is low. However, the CO2 laser beam cannot be focused to a spot size as small as the required droplet size, resulting in a loss of potential CE between the input CO2 power and EUV in-band power. This happens because much of the CO2 laser energy is not coupled into the plasma.
‘Puffing’ the tin droplets
A solution to this issue is the use of prepulse technology (see figure). In this scheme, a low-intensity pulse of light is fired at the tin droplet before the CO2 laser main pulse in order to pre-puff the droplet from its original diameter of about 30 μm to more than 100 μm. This increases the interaction area between the main laser pulse and the droplet and allows more of the pulse energy to be coupled into the tin target, resulting in an increase in CE and EUV output power.
The current pre-pulse configuration improves CE by a factor of approximately two over the CE during normal operation. The pre-pulse pulse intensity is carefully controlled in order to provide a droplet expansion velocity that produces the optimum expanded size by the time the main laser pulse is fired. Further optimization of the pre-pulse conditions is one of the paths to additional CE improvements in the future.
Pre-pulse technology requires sophisticated controls to ensure that maximum CE is achieved at high laser pulse repetition rate and duty cycle. Both the droplet position and laser beam focus position must be controlled in three dimensions so that the targeting is optimum for every pulse at a rate of about 50 kHz.
Slight deviations from optimum targeting can lead to reduced CE and energy excursions that potentially impact dose control at the wafer. Integration of the droplet and beam metrology and controls hardware and algorithms has allowed successful closure of control loops for all spatial dimensions, in addition to timing and energy.
Cymer’s pre-pulse technology has been successfully demonstrated on a fully integrated pre-production EUV source, running at high laser repetition rate and high duty cycle. Simulated wafer exposure tests have been repeatedly carried out over multiple runs, containing thousands of long bursts that simulated the exposure time required for wafer die exposures.
The current performance level is at 40 W of dose-controlled power over several hours of stable operation. Over this time period, the controls system maintained accurate droplet targeting for both the laser pre-pulse and main pulse such that there were no deviations in energy greater than 0.5% of the average dose within each simulated die.
“Pre-pulse technology has been demonstrated as the path to continued increases in EUV source power,” says Nigel Farrar, vice president of EUV strategic marketing at Cymer. “Scaling will be achieved through increases in CO2 laser power and improvements to CE from optimization of pre-pulse conditions. A road map to power levels of 250 W and beyond has been established to support introduction of EUV lithography manufacturing within the next few years.”
About the Author
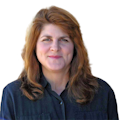
Gail Overton
Senior Editor (2004-2020)
Gail has more than 30 years of engineering, marketing, product management, and editorial experience in the photonics and optical communications industry. Before joining the staff at Laser Focus World in 2004, she held many product management and product marketing roles in the fiber-optics industry, most notably at Hughes (El Segundo, CA), GTE Labs (Waltham, MA), Corning (Corning, NY), Photon Kinetics (Beaverton, OR), and Newport Corporation (Irvine, CA). During her marketing career, Gail published articles in WDM Solutions and Sensors magazine and traveled internationally to conduct product and sales training. Gail received her BS degree in physics, with an emphasis in optics, from San Diego State University in San Diego, CA in May 1986.