PHOTONIC FRONTIERS: DIRECT LASER DIODES: Making direct laser diodes shine more brightly
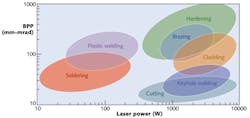
When it comes to efficiently converting electrical input into light, laser diodes can't be beat, achieving greater than 70% wall-plug efficiency in the laboratory. But that figure measures high-divergence emission from a small aperture, not a useful beam. The challenge for direct diodes is putting as much of that energy to work as possible.
So far, the best applications have been spreading laser energy uniformly, such as sweeping a square or line beam across a surface for heat treating or metal cladding.1 Fiber beam delivery can concentrate direct-diode power to the intensity needed for welding metals but falls short of the higher brightness needed to cut metals.
Beam quality and direct-diode applications
Diode laser powers are impressive, with tens of watts from single emitters, hundreds of watts from multistripe bars, and thousands of watts from stacks of bars. But edge-emitting diode beams diverge very quickly perpendicular to the thin active layer, which poses challenges for materials working.
Figure 1 shows values of two key laser parameters—beam quality and output power—needed in materials working. The largest application, metal cutting, requires high power and a small intense spot, as shown at lower right. Welding requires larger spot sizes to fuse sheets together. Heat treating and applying metal claddings require high powers spread over large areas, as shown at upper right. Plastic welding and metal soldering require lower powers.
Direct diodes can be tailored to fit many applications. They are "ideal heat sources for large-area heat processing," says Frank Gaebler, director of marketing for materials processing at Coherent Inc. (Santa Clara, CA). Multiple-stripe diode bars can be stacked to generate direct-diode powers to 8 kW. Stacks with beam-shaping masks and optics can produce beams from 1 × 3 mm to lines 6 × 36 mm. "A large mode with a top-hat profile is very fast and efficient" in applying wear-resistant cladding layers to metal shafts used in the oil industry, says Gaebler. Multikilowatt line beams heat large areas fast, speeding processing.
Fiber beam delivery and beam combination
Optical fibers can deliver the higher-intensity beams needed for welding applications. Fiber coupling produces a round beam and can collect the output of many diodes, either discrete devices or separate stripes on a diode bar.
The output from diode bars is coupled into a single beam-delivery fiber. The approach is straightforward, avoids the need to splice fibers, and offers serviceability for long-term product support. "We believe that bar technology is easier to maintain in the field," says Gaebler.
On the other hand, single emitters generate more power per stripe, and the space between adjacent stripes on a bar is too tight to connect all of them to 50- or 100-μm-core fibers, says Georg Treusch, managing director of TRUMPF Photonics (Cranbury, NJ). Although a 55-emitter bar can emit a total of 200 W, fibers can reach only 19 stripes, yielding only 50 to 60 W. Connecting the same 19 fibers to 10 W single emitters would collect 190 W in suitable fiber.
Beam-delivery fibers vary in light-guiding core size, depending on the application. Cores of 50 or 100 μm are common for cutting and other precision applications. Cores of 400 to 600 μm are used for brazing and some types of welding, and 600 μm fibers can deliver a few kilowatts of power. Core sizes to 1500 μm can be used for applications such as hardening and cladding.
Power capability depends on core size, and beam quality depends on both core size and numerical aperture. Laserline Inc. (Santa Clara, CA) rates a 200 μm fiber with 0.2 NA as able to deliver 500 W with beam parameter product (BPP) of 20 mm-mrad; a 400-μm fiber with 0.1 NA can deliver up to 2 kW at the same beam quality.
Types of beam combination
Advanced beam-combination techniques can increase brightness as well as total power. Diode output is inherently polarized, so power can be doubled by combining two beams of orthogonal polarization. For example, the 80 W produced by combining eight diodes emitting 10 to 12 W in a 100 μm, 0.12 NA fiber can be doubled to 160 W by adding a second set of eight such emitters with orthogonal polarization.
Two other techniques can further increase power. Coherent beam combination superimposes multiple beams so their phases add, as when a single master oscillator drives several parallel power amplifiers. Wavelength beam combination adds laser beams at several wavelengths, like wavelength-division multiplexing in a fiber-optic system, with the wavelength difference preventing destructive interference among the wavelengths.
Coherent beam combination promises high beam quality as well as high power. However, implementation has been difficult because it requires sub-wavelength phase control and path-length matching, and narrow laser linewidth. Coherent combining of fiber lasers has produced hundreds of watts, but diode results are considerably more modest.2 Two years ago, the MIT Lincoln Laboratory (Lexington, MA) reported coherently combining the output of 218 parallel semiconductor amplifiers to generate 38.5 W.3
Wavelength beam combining has been far more successful, reaching the kilowatt level. TRUMPF uses four lasers spaced about 30 nm apart between 938 and 1030 nm to achieve power to 6 kW in fiber-coupled beams with BPP of 20 to 30 mm-mrad for brazing and welding applications. A pair of startups pack wavelengths closer together in different ways, seeking the high intensity needed for laser cutting.
DirectPhotonics (Berlin, Germany) uses a modular approach that starts with a module that optically stacks 12 single emitters. As shown in Fig. 2, the diodes are mounted on 12 steps within the module. A fast-axis collimator lens is mounted on each emitter to focus light into the plane of the step and onto a curved slow-axis collimator mirror on the corresponding step on the opposite side. The step reflectors stack beams from individual emitters so they can be focused into a 100 or 200 μm output fiber. A volume Bragg grating locks all diodes in the module to the same wavelength.Multiplexing four wavelengths at 2.5 nm intervals using dichroic mirrors increases the power and maintains good beam quality. DirectPhotonics has demonstrated 1 and 2 kW versions with wall-plug efficiency above 30%, says cofounder Mark Wippich. BPP from the fiber output is 7.5 mm-mrad, making the system suitable for metal cutting, and developers hope for further improvements in beam quality.
TeraDiode (Wilmington, MA) builds its approach on diode bars arranged in an external cavity so a diffraction grating, a transform lens, and an output coupler select different wavelengths in the 970 nm band from each stripe, as shown in Fig. 3.4 The bar emits across a 30 nm range. The basic multiwavelength module generates 500 W through a 50 μm fiber, and a 2 kW version emitting through a 100 μm fiber also is available. TeraDiode says the modules can be stacked to generate up to 6 kW.In 2012, CEO Parviz Tayebati told Laser Focus World that the company had demonstrated a 360 W version for DARPA that had a BPP of 0.6 mm-mrad, close to that of a singlemode fiber laser. The company's commercial goal is BPPs of 2 to 8 mm-mrad, suitable for the large metal-cutting market. Prototypes have reached 46% wall-plug efficiency.2
Outlook
Direct diodes have achieved real progress, but real limitations remain. A central issue is the tradeoff between efficiency and beam quality. Beam combining optics can improve beam quality; they also lose light in the process, reducing efficiency.
Wall-plug efficiency needs to be improved, says Treusch. "Right now we can reach 70% to 73% in the lab, but it is more like 65% to 68% in average operation," and down to 60% for harvestable light, he notes. "You cannot collimate the beam. You always have losses. In the end, we are happy to have 50%" on the workpiece from a single emitter, and that's not in a tightly focused beam. "It's hard to consistently achieve more than 40%" with wavelength combining at 2 to 3 kW, he says.
That's close to the 30% to 35% wall-plug efficiency of fiber and disk lasers, which can convert 65% to 70% of diode pump power into a higher-quality beam. Can direct diodes overcome the advantages of gain media in producing the high-intensity beams needed to cut metals? That's a good question, and it's provoking a technology horse race that will be well worth watching.
REFERENCES
1. T. Koenning et al., "KW-class line sources for direct applications," Proc. SPIE, 8241, 824105-1 (2012); doi: 10.1117/12.911816.
2. J. Hecht, "Photonic Frontiers: Beam Combining: Beam combining cranks up the power," Laser Focus World, 46, 6 (June 2012).
3. S.M. Redmond et al., "Active coherent beam combining of diode lasers," Opt. Lett., 36, 909–911 (Mar. 15, 2011).
4. R.K. Huang et al., "Direct diode lasers with comparable beam quality to fiber, CO2, and solid state lasers," Proc. SPIE, 8241, 824102 (2012).
About the Author
Jeff Hecht
Contributing Editor
Jeff Hecht is a regular contributing editor to Laser Focus World and has been covering the laser industry for 35 years. A prolific book author, Jeff's published works include “Understanding Fiber Optics,” “Understanding Lasers,” “The Laser Guidebook,” and “Beam Weapons: The Next Arms Race.” He also has written books on the histories of lasers and fiber optics, including “City of Light: The Story of Fiber Optics,” and “Beam: The Race to Make the Laser.” Find out more at jeffhecht.com.