SPECIALTY FIBERS: Dual-core fiber has nanomechanical switching properties
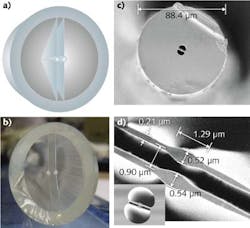
Researchers at the University of Southampton (Southampton, England) have shown off a novel dual-core fiber architecture that permits changes in the coupling between the cores, allowing light to jump between the two with tiny amounts of pressure.1
The team, from the Optoelectronics Research Centre (ORC), has been developing the technique for a decade and has finally cracked the engineering challenges in drawing the unique fibers. This paves the way for fibers with a higher number of cores and a range of applications from precision sensing and optical buffering to beam scanning.
Wei Loh of the ORC notes that while multiple-core fibers were already a mature technology, to date they lack functional flexibility. “Traditionally, fibers once they’ve been made are mechanically quite rigid,” he explains. “The technology has now improved so we’re able to make fibers where the cores can mechanically move—which makes them very similar to micromechanical systems (MEMS) devices.”
The team started with lead silicate glass (chosen for its low melting point and ease of extrusion) and a steel die with two slots, each with a circular hole. The preform resulting from the extrusion process is drawn down to a 1 mm diameter, placed in a glass jacket tube as cladding, and then drawn to the final fiber geometry: two submicron fiber cores, each held in place by a 200-nm-thick glass membrane that anchors them to the outer wall of the overall fiber. The two cores are separated by about 2 μm (see figure).
Switched by air-pressure changes
To make one core move relative to another, which changes their optical coupling, a slot was added to the end of the fiber adjacent to one of the cores. The wall of the fiber adjacent to the other core was etched away. That process allows application of a tiny amount of pressure using nitrogen gas in the half of the fiber that was still closed, forcing the glass membrane containing one core to bend toward the other.
The team showed that by moving one core by just 8 nm, light could be made to jump from one core to another. This phenomenon could lead to precision pressure and movement sensing applications, but Loh’s team has moved on to new ways to shift the cores.
“What we’re moving toward now is to get electrostatic actuation—just like in silicon MEMS—movement by applying electrostatic fields,” he says. “If we do that, we should be able to control it very precisely.”
One crucial application of the technology is optical buffering—slowing or storing a light signal for routing. “If you look at one small core, much of the light is outside in the air, because that’s where the mode is, so the speed of the light approaches that in the air,” Loh says. “Now when you have two cores and bring them close together, the amount of glass that the light sees is much greater, and the light becomes better confined and slows down. You have a much larger glass core, which is more like a conventional fiber.”
The range of potential applications for the technique is huge, leading not only to all-optical networks but possibly to all-fiber networks. However, much work lies ahead in scaling up the process and developing multiple-core fibers.
“There will be lots of challenges,” says Loh. “But given that we’re able to make these fibers now, I think those challenges are solvable—it’s more a question of the engineering and the design.”
Beyond tunable optical buffers, he adds that uses might include tunable filters and the use of multiple-core fibers in a way analogous to phased-array radar, with the cores working in concert for precision beam scanning.
REFERENCE
1. Z. Lian et al., Opt. Exp., 20, 28, 29386–29394 (2012); doi:10.1364/OE.20.029386.