INTERFEROMETERS: Integrated optical sensor measures dynamic magnetic fields
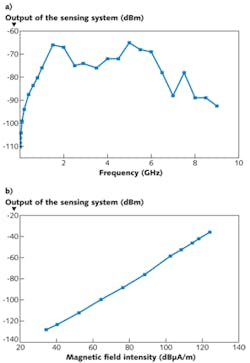
Magnetic-field sensors that measure the magnetic portion of electromagnetic fields (as opposed to sensors that measure static magnetic fields) are valuable for determining problems with electromagnetic interference in electronic circuits. Conventional metallic-probe magnetic-field sensors tend to pick up electric as well as magnetic signals; previous attempts to create an electro-optical magnetic-field sensor to solve these problems have resulted in complex optical systems unsuited for use in the field.
Scientists at the University of Electronic Science and Technology of China (Chengdu, China) have now created an integrated optical magnetic-field sensor that is situated on a nonlinear-crystal chip 35 × 6 × 1 mm in size.1 The device can sense magnetic fields oscillating at frequencies into the gigahertz range.
Waveguide interferometer
A doubly loaded loop antenna and a Mach-Zehnder interferometer were both fabricated on a chip of x-cut lithium niobate (LiNbO3). The interferometer was fabricated first by a proton-exchange technique in benzoic acid followed by annealing, then a silicon-dioxide buffer layer was deposited before evaporating and electroplating the electrodes and antenna from chromium and gold. The width of the waveguide was 6 µm, and the Mach-Zehnder interferometer had a π/2 optical bias to ensure a linear output. Two V-grooves were created in the device for fiber-coupling light in and out of the device. A continuous-wave, 1 mW, 1310 nm laser source was coupled to the interferometer with polarization-maintaining singlemode fiber; the output of the interferometer was coupled via singlemode fiber to a fast photodetector connected to a spectrum analyzer.
The presence of an external magnetic field creates a voltage across the electrodes, which modulates the phase of the beams in the interferometer, and thus the light output. The structural symmetry of the electrodes naturally cancels out any voltages created by an electric field, causing only the magnetic component to modulate the light beam.
To create an electromagnetic field for experimentation, a transverse electromagnetic (TEM) cell was used for fields from DC to 1 GHz, and a gigahertz TEM was used for fields from 1 to 18 GHz. The sensor was placed so that it was parallel to the direction of electromagnetic-wave propagation. The resolution bandwidth was 10 Hz, while the sensing system’s noise floor was -120 dBm.
The frequency response of the device extended from 2 kHz to 9 GHz (see figure). The field strength of the source was varied to test dynamic range; at 1 GHz, the device showed a dynamic range of 98 dB and a linear response. The minimum detectable magnetic field was 51.8 µA/m—a level that can be further decreased by using a light source with a higher optical output. The researchers plan to take a closer look at the sensor’s performance as a function of temperature, as well as increasing its sensitivity.
REFERENCE
1. B. Sun et al., Appl. Opt., 50, 11, 1570 (Apr. 10, 2011).
About the Author
John Wallace
Senior Technical Editor (1998-2022)
John Wallace was with Laser Focus World for nearly 25 years, retiring in late June 2022. He obtained a bachelor's degree in mechanical engineering and physics at Rutgers University and a master's in optical engineering at the University of Rochester. Before becoming an editor, John worked as an engineer at RCA, Exxon, Eastman Kodak, and GCA Corporation.