PLASMONICS: Airy beam controls the flow of surface plasmon polaritons
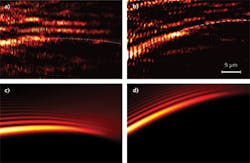
Light can travel seemingly without diffraction in a curved arc in free space. Such peculiar optical beams are named “Airy beams” after English astronomer Sir George Biddell Airy, who studied the parabolic trajectory of light in a rainbow. In 2007, Airy beams were first demonstrated in a laboratory setting by a research team at the University of Central Florida (Orlando, FL).1 One year later, researchers at the University of St. Andrews (Fife, Scotland) developed one of the first applications for these “Airy” beams: moving particles in a curved path for microfluidic engineering and cell-biology applications.
Recently, Airy beams were theoretically introduced into plasmonics for controlling the surface-plasmon polaritons (SPPs) along metal-dielectric interfaces.2 Now, researchers at the University of California–Berkeley, Lawrence Berkeley National Laboratory (LBNL), and San Francisco State University have experimentally realized such plasmonic Airy beams (PABs). More importantly, they have found a way to dynamically control the trajectories of these PABs in real time, offering a new approach to control the flow of SPPs over metallic surfaces for possible applications in reconfigurable optical interconnects and on-chip nanoparticle manipulations.3
Plasmonic Airy beams
In order to manipulate SPPs—electromagnetic waves that propagate parallel to a metal/dielectric surface—for light-routing applications such as optical integrated circuits, permanent (and difficult-to-fabricate) nanostructures are required. But by directly coupling free-space Airy beams to SPPs on a metal surface through a grating coupler, the SPPs can be dynamically routed along parabolic trajectories without diffraction and any physical waveguide structures. The trajectories of such PABs can be changed in real time either through mechanical adjustment of the launch condition or through a computer-controlled spatial light modulator (SLM). The PABs make it possible to route light over metallic surfaces—even over rough structures or obstacles.
In the experimental setup, a one-dimensional Airy beam is created via a cubic phase mask by passing 820 nm laser light through an SLM followed by Fourier transformation through a 20X objective lens. The output strikes an 805-nm-period grating etched into a 50-nm-thick gold film on a quartz substrate. A half-wave plate ensures that the polarization of the beam is parallel to the grating vector. The excited PAB is monitored using the optical far-field method of leakage radiation microscopy. Transverse or longitudinal displacements of the objective lens or computer-based adjustment of the positions of the input beam and phase mask in the SLM are used to dynamically modulate the path of the PABs. These displacements can be used to manipulate the ballistic motion of the PAB, as well as the location of the peak intensity within the PAB arc (see figure).
“Apart from being the first experimental demonstration of PABs, our results enable a new way to dynamically route surface energies in real time without any fabricated permanent waveguiding structures, which may inspire researchers from different areas to develop new technologies or tools for a variety of applications,” says professor Xiang Zhang, director of the NSF Nanoscale Science and Engineering Center of UC Berkeley and a faculty scientist at LBNL, who led the research. Team member Peng Zhang adds, “Our method could improve the sensitivity of current plasmonic optical sensors and may be directly applied for exciting Airy surface waves in other low-dimensional systems, including graphenes and topological insulators.”
REFERENCES
1. G.A. Siviloglou et al., Phys. Rev. Lett., 99, 213901 (2007).
2. A. Salandrino et al., Opt. Lett., 35, 2082 (2010).
3. P. Zhang et al., Opt. Lett., 36, 16, 3191–3193 (2011).
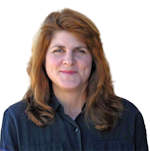
Gail Overton | Senior Editor (2004-2020)
Gail has more than 30 years of engineering, marketing, product management, and editorial experience in the photonics and optical communications industry. Before joining the staff at Laser Focus World in 2004, she held many product management and product marketing roles in the fiber-optics industry, most notably at Hughes (El Segundo, CA), GTE Labs (Waltham, MA), Corning (Corning, NY), Photon Kinetics (Beaverton, OR), and Newport Corporation (Irvine, CA). During her marketing career, Gail published articles in WDM Solutions and Sensors magazine and traveled internationally to conduct product and sales training. Gail received her BS degree in physics, with an emphasis in optics, from San Diego State University in San Diego, CA in May 1986.