OPTICAL DESIGN: New shape specification eases design and fabrication of aspheres
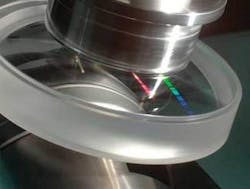
The capabilities that well-designed aspheric lens surfaces can bring to optical systems are dramatic, from the simplification of objective lenses for CD and DVD drives to larger field sizes for microlithographic projection lenses. Adding aspheric surfaces to an optical design, however, can be difficult; one hurdle is the conventional mathematical representation of an aspheric surface, which for strong aspheres can introduce substantial uncertainties in the surface profile for even tiny round-off errors. Now, Greg Forbes, senior scientist at QED Technologies (Rochester, NY), has developed a shape specification that is quite well-mannered, leading to aspheric surfaces that match their intended shape-and can easily be constrained (in the process of optical design) to be more manufacturable.1
The radial profile of a rotationally symmetric aspheric surface is conventionally represented by a conic plus a polynomial that consists of a sum of monomial even-power terms; this representation is then best-fitted to the desired optimum surface profile by the optical-design program. But the terms of the polynomial, which typically alternate in sign and produce the desired profile only through heavy cancellation, are often badly behaved and, indeed, practically limit the polynomial to no more than about ten terms. This contrary behavior takes the form of huge coefficients, which lead to individual terms that can be many thousands of times larger than their coordinated effect on profile shape (net sag). The result is extreme sensitivity to errors.
The representation developed by Forbes is instead based on terms that each consist of a set of polynomials, with each term orthogonal with respect to the others-a property that essentially “decouples” each term from the rest, avoiding any heavy cancellation. “When it gets to the manufacturing end, lots of canceling coefficients boosts the chance of operator errors,” says Forbes. “We have seen this in our metrology efforts, where, thankfully, errors generally mean only that the test process fails. In fabrication, such errors generally mean that the part would be given the wrong shape. In the new representations, the coefficients can be interpreted at a glance, unlike the traditional set, which need significant processing to get any idea of the part’s shape.”
Perhaps more important, Forbes notes, the traditional representation does not make it easy for a designer who wants to place constraints on aspheres to force them to be more cost-effective (able to be fabricated and tested without dedicated tooling or null optics). Working with the new representation chiefly involves the straightforward task of constraining the sum of the squares of the coefficients that describe the surface. Such matters can play a significant role for global optimization, in which the designer must specify the domain to be searched, says Forbes; in the new representations, this is far easier to do and can lead to more-efficient searches.
Two bases
A particular form of representation (called a “basis”) can be tailored for a particular need. One basis, termed “Qcon,” is intended for unconstrained aspheres, explains Forbes. “For example, telescope primary mirrors are close to paraboloids, and the secondaries can be close to hyperboloidal. In this case, the conic picks up most of the aspheric departure (and generally allows for simpler dedicated null tests). The additive polynomial in this case is structured to leave the axial intercept and axial curvature of the conic unchanged. These entities are often of direct interest to the designer who therefore needs easy access to them. That is why the polynomial portion in this case begins at the fourth order.”
The second basis, called “Qbfs,” has another purpose altogether, Forbes notes. “In particular, for an asphere to be especially cost-effective, it must be sufficiently close to spherical in shape. More specifically, for the purposes of testing, the slope of the normal deviation between the part and its best-fit sphere must be constrained. This second basis is therefore defined with respect to a sphere. What’s more, the additive portion now must start at the second order (to allow for the axial curvature to be different from the best-fit curvature) and it must vanish at the edge (to leave the best-fit sphere unchanged). In this way, the additive portion changes the shape of the surface without changing its best-fit sphere. Again, the coefficients can be interpreted upon inspection. The main thing, however, is that a measure of the difficulty of interferometrically testing the part is directly accessible. These constraint-related matters are the main motivation behind Qbfs, and our intent with it is to boost the prevalence of more-cost-effective aspheres by putting improved tools in the designers’ hands.”
The particular levels that are set for these constraints depend on the interferometric tool, whether it be a standard Fizeau interferometer (which, without null optics, can measure only mild aspheres), or QED’s SSI-A (a subaperture-stitching interferometer that, again without null optics, can measure stronger aspheres).
But the ideal is to tie the new aspheric-surface representations into the entire design and fabrication process. “We can directly include these new representations into QED’s control software, but the challenge is to get them used by designers so that users will come to our machines with these new descriptions of aspheres in their hands,” says Forbes. “We are therefore working with the major optical-design-code people to see if we can facilitate getting these representations in place and used.”
REFERENCE
1. G.W. Forbes, Optics Express 15(8) (April 16, 2007).
About the Author
John Wallace
Senior Technical Editor (1998-2022)
John Wallace was with Laser Focus World for nearly 25 years, retiring in late June 2022. He obtained a bachelor's degree in mechanical engineering and physics at Rutgers University and a master's in optical engineering at the University of Rochester. Before becoming an editor, John worked as an engineer at RCA, Exxon, Eastman Kodak, and GCA Corporation.