Manufacturers of CCD and CMOS imagers have long argued the merits of each technology. Generally speaking, for machine-vision applications, CCD imagers remain the detector of choice, while CMOS imagers are used in more specialized applications requiring high speed, low cost, random access, or high dynamic range. The reasons for this difference lie primarily in the specific design of the pixels and readout electronics associated with each device.
As a small-volume market, machine vision has depended on technology developed for consumer markets. Yet many machine-vision applications require higher performance than consumer-based devices can deliver. Some CCD and CMOS manufacturers have realized this opportunity and optimized their production for added-value niche markets.
Many scientific, medical, and security imaging applications demand low-light, solid-state sensors with photon-counting sensitivity that can capture hundreds of frames per second. Although CCDs are capable of high quantum efficiency, low dark current, high linearity, and uniformity, their serial-readout design limits readout speed. In addition, the on-chip output amplifiers of these devices need to be operated at high speed, increasing CCD read noise and compromising sensitivity in low-light-level applications.
To overcome these limitations, engineers at Fairchild Imaging (Milpitas, CA) have developed a low-light-level digital camera with a Camera Link interface that combines the best features of CCD imagers and CMOS technology. The camera, shown at Photonics West (San Jose, CA), uses two CMOS readout ICs that are bump bonded to a split-frame transfer CCD. With very low dark current, the camera has been demonstrated to capture images at 30 frames/s where the brightest region within the image has less than 200 photoelectrons.
Low-light level
Scientific CCD image sensors with electron multiplication are also beginning to emerge for low-light-level applications. Before charge-to-voltage conversion, charge passes through a series of multiplication states, in which photogenerated electrons create more electrons with impressively low excess noise. While these devices still suffer flaws due to aging and at high temperature, they are already commercially available and permit low-light-level cameras to be built more easily.
The back-thinned CCD97 from e2v technologies (Chelmsford, England), for example, is available in a 512 times; 512 frame transfer format and is part of the company’s L3Vision range. For scientific imaging at low light, it uses an electron-multiplication output amplifier circuit that can operate with read noise of less than one photoelectron at pixel rates in excess of 11 MHz .
By coupling the quantum-efficiency performance of back-thinning with low read noise, the CCD97 complements the back-thinned CCD60. The back-illuminated CCD60 was the first CCD to offer sensitivity close to the theoretical maximum for a silicon imaging sensor, with quantum efficiency greater than 90% and read noise less than one electron, extending the scope of CCD sensor applications to include confocal microscopy, single-molecule imaging, and adaptive optics.
The CMOS counterpart to this CCD-based electron multiplication technology is called Geiger-mode avalanche pixels. At a pixel size of about 30 µm, the devices are capable of detecting a single photon. However, further developments are needed to increase their fill factor from their current 5%.
In operation, each single-photon avalanche diode (SPAD) is a p-n junction biased above breakdown voltage by an excess voltage of a few volts. A primary carrier resulting from the absorption of a photon can generate an infinite number of secondary electron-hole pairs by impact ionization. Upon arrival of a photon, the breakdown current discharges the depletion region capacitance, reducing the voltage across the SPAD to its breakdown voltage. The near-infinite internal gain requires no further amplification and the pixel output can be routed directly outside the chip.
At the Swiss Federal Institute of Technology (Lausanne, Switzerland), a single 32 × 32 SPAD imager has been developed specifically for use in a 3-D camera. Based on the pulsed time-of-flight (TOF) method, the sensor used in the camera is implemented in standard CMOS technology and consists of an array of single-photon avalanche diodes, capable of performing 1024 independent distance measurements.
About the Author
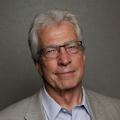
Conard Holton
Conard Holton has 25 years of science and technology editing and writing experience. He was formerly a staff member and consultant for government agencies such as the New York State Energy Research and Development Authority and the International Atomic Energy Agency, and engineering companies such as Bechtel. He joined Laser Focus World in 1997 as senior editor, becoming editor in chief of WDM Solutions, which he founded in 1999. In 2003 he joined Vision Systems Design as editor in chief, while continuing as contributing editor at Laser Focus World. Conard became editor in chief of Laser Focus World in August 2011, a role in which he served through August 2018. He then served as Editor at Large for Laser Focus World and Co-Chair of the Lasers & Photonics Marketplace Seminar from August 2018 through January 2022. He received his B.A. from the University of Pennsylvania, with additional studies at the Colorado School of Mines and Medill School of Journalism at Northwestern University.