LASER MICROPROCESSING: Lotus-leaf biomimetics create hydrophobic surface
A process devised by researchers at the University of Twente (Enschede, The Netherlands) produces a water-repellent surface that mimics the complex surface of a naturally hydrophobic and self-cleaning lotus leaf. The researchers created laser-machined structures in injection molds that are then used to mold polymer surfaces, which, due to their structure, are highly water-repellent.1 Because the leaf of the lotus plant—as revealed by a scanning-electron microscope—consists of a cone-shaped background covered with tiny wax crystals, the laser-texturing process must mimic the overall macroscopic background, as well as the microstructures on the pillar surfaces. In addition to the cone structure with feature sizes in the 10 µm range, a submicron superimposed structure is needed.
This complex pattern can be machined by femtosecond pulsed lasers in one run because of a self-structuring phenomenon that was found by serendipity: in the first experiments using the femtosecond-pulsed laser, periodic ripple structures and more-chaotic rough structures in the submicrometer regime were seen to emerge. Recognizing the usability of these self-organizing phenomena, the researchers studied the formation of these ripples based on a number of laser parameters.
Slightly subwavelength ripples
The submicrometer ripple pattern was found to be a general phenomenon occurring on all kinds of materials after illumination with several pulses. The ripple spacing was usually between 600 and 700 nm, just beneath the 800 nm wavelength of the femtosecond pulsed laser. After irradiation with further pulses, the ripple pattern deteriorates into trenches that appear perpendicular to the ripple patterns. By applying even more pulses, highly chaotic structures emerge. The point of transition between the two self-structuring regimes, as well as the morphology of the emerging rough structures, depends on the process parameters used.
One parameter is the repetition rate of the laser source, which can be tuned from 10 to 300 kHz. The laser-repetition rate strongly influences the morphology of the microstructures. At 100 kHz, the emerging structures showed the most extreme forms, possibly indicating that a time-dependent factor plays a role in the physical background of the structuring mechanism. Future experiments on different materials are planned to clarify whether this “eigenfrequency” is a material-dependent factor.
In addition to optimizing the finer microstructure patterns, the self-cleaning properties of the surface also depend on the cone-shaped pillar pattern. This pattern was machined into the steel mold by a direct-write process. By careful selection of the laser parameters, the pillars and the submicron structure can be machined in one run. This means that the laser pulses ablating the material in the 10 µm range also lead to the emergence of the submicrometer pattern. This method is fast and can easily be used for 3-D curved surfaces.
Next, the researchers used the steel molds to fabricate polypropylene replicas. Polypropylene is an inexpensive material with relatively low surface tension that leads to hydrophobic properties. By applying a designed microstructure on such a material, ultrahydrophobicity comparable to the lotus leaf can be achieved (see figure). The fabricated surfaces are nonwetting and water droplets residing on them are very mobile.
“Besides the amplification of hydrophobicity, surface structures can also be used to amplify hydrophilic properties,” says Max Groenendijk, one of the researchers. “Design and fabrication of such structures enable us to control wetting. Applications for such surfaces include control of microfluidic flows, friction control in lubrication, control of drop formation in emulsification, wetting control of scaffolds for tissue engineering, and many other applications where a liquid and a solid phase are in contact.” Groenendijk says the future focus of the research will be on the fabrication of surfaces out of different materials, including more-robust polymers.
REFERENCE
1. M. Groenendijk and J. Meijer, paper M202, ICALEO 2006, Scottsdale, AZ (October 2006).
About the Author
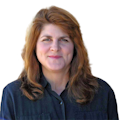
Gail Overton
Senior Editor (2004-2020)
Gail has more than 30 years of engineering, marketing, product management, and editorial experience in the photonics and optical communications industry. Before joining the staff at Laser Focus World in 2004, she held many product management and product marketing roles in the fiber-optics industry, most notably at Hughes (El Segundo, CA), GTE Labs (Waltham, MA), Corning (Corning, NY), Photon Kinetics (Beaverton, OR), and Newport Corporation (Irvine, CA). During her marketing career, Gail published articles in WDM Solutions and Sensors magazine and traveled internationally to conduct product and sales training. Gail received her BS degree in physics, with an emphasis in optics, from San Diego State University in San Diego, CA in May 1986.