MICRO-OPTICS: Hydrogel-controlled liquid microlenses respond to stimuli
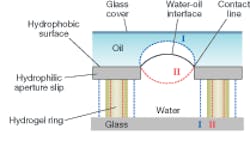
Small and versatile adaptive liquid lenses have been fabricated by researchers at the University of Wisconsin-Madison; the many potential uses of these lenses stem from the fact that their focal length can respond to a number of unusual stimuli, such as pH or the presence of biological substances like antigens.1 They can also be made to respond to many other useful stimuli that include light, electrical fields, and temperature.
The microfluidic lenses get their optical power from a fluid interface that has oil on one side and water on the other (with different refractive indices); the edge of this interface is “pinned” by a circular interface between a hydrophilic sidewall and its hydrophobic top surface (see Fig. 1). Below the sidewall is a hydrogel ring, which contacts or expands in response to external stimuli, changing the volume of the water inside the ring, which then pushes or pulls on the oil/water surface and alters its optical power.
The solid supporting portion of the device’s structure is fabricated by polymerizing a UV-curable plastic using photolithography. In one experimental example, a temperature-sensitive hydrogel, which contracts as the temperature is raised, is placed in the device. In this case, a plastic outer ring restricts the hydrogel so that it can only expand inward; although the hydrogel absorbs water from the reservoir within, it expands by a volume greater than the water it absorbs. The liquid lens, which is about 2 mm in diameter, takes 20 to 25 seconds to change focal length from -11.7 mm at 23°C to infinity at 47°C.
A second example replaces the temperature-sensitive gel with one that responds to pH; in this case, no outer plastic ring is present, allowing the hydrogel ring to respond to the pH of the surrounding solution. The response time is about 12 seconds for a visual change in the shape of the lens meniscus.Arrays respond locally
Adaptive-microlens arrays are possible; to demonstrate the concept, the researchers fabricated a pair of liquid microlenses, each with a different hydrogel-one expands under increasing pH, the other contracts under the same conditions (see Fig. 2). Arrays of stimuli-driven microlenses, whether using identical or differing hydrogels, have the scientifically interesting ability to respond to very local stimuli, thus providing a 2-D “map” of the immediate environmental conditions.
The lenses can be fabricated in diameters ranging from the micrometer to the millimeter level-in other words, at any size at which surface tension is the dominant shaping force, says Hongrui Jiang, one of the Wisconsin researchers. Micro-imaging and other optofluidic systems, as well as lab-on-a-chip technology, are applications of interest. “Biological and chemical sensing are most-immediately realizable,” he notes. “I am most excited by a micro-imaging system that incorporates these lenses.”
REFERENCE
1. L. Dong et al., Nature 442 (Aug. 3, 2006).
About the Author
John Wallace
Senior Technical Editor (1998-2022)
John Wallace was with Laser Focus World for nearly 25 years, retiring in late June 2022. He obtained a bachelor's degree in mechanical engineering and physics at Rutgers University and a master's in optical engineering at the University of Rochester. Before becoming an editor, John worked as an engineer at RCA, Exxon, Eastman Kodak, and GCA Corporation.