PHOTONIC FRONTIERS: HIGH-POWER FIBER LASERS: Pumping up the power
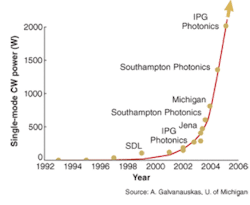
Bigger used to be better when it came to making high-power lasers, but fiber lasers have changed the equation. Fiber lasers confine the pump light and the stimulated emission to small volumes, allowing pumping efficiency to exceed 80% in the best materials. Pumping with high-power diode lasers, therefore, can effectively convert low-quality diode output into powerful, high-quality beams from the fiber laser.
That comparatively simple recipe has kept fiber lasers on a roll of steadily increasing output powers for several years (see Fig. 1). The highest single-mode powers yet achieved in the laboratory, about 2-kW continuous wave (CW), have come from ytterbium-doped fiber lasers emitting near 1.1 µm. But powers have also been increasing from erbium-doped fiber lasers emitting at 1.5 to 1.6 µm and from thulium-doped systems emitting at 1.8 to 2.2 µm. Commercial fiber lasers emitting a couple of hundred watts already are used for materials working, and military developers are taking a hard look at the prospect of laser weapons based on high-power fiber lasers.
Fiber-laser design concepts
High-power fiber lasers are built around dual-core fibers (see Fig. 2). The inner core, with the highest refractive index, is doped with light-emitting rare-earth elements such as ytterbium and erbium, which may be concentrated in the central part of the core. The outer core (sometimes called the inner cladding) has an index intermediate between the inner core and the outer cladding. External diode lasers pump the outer core, which confines the pump light and guides it so it passes through the inner core and excites the light-emitting atoms. High pump powers typically are coupled into the outer core through tapered couplers, which sometimes combine the output of 6 or 19 pumps. The outer cladding has a lower refractive index, and passively confines pump light inside the outer core.To optimize conversion efficiency, the outer core should have a large area to collect as much energy as possible from multimode pump diodes. The cross section of the outer core is designed to pass all pump light through the central inner core at some point along the fiber. Conversely, the inner core should be relatively small, to concentrate most emission in a single mode. The actual sizes depend on design tradeoffs. The outer cores of high-power fiber lasers approach 1 mm in diameter to match the emitting areas of kilowatt-class pump lasers. Higher powers also require larger inner cores, to increase emitting volume and limit the optical power density to control nonlinear effects. For kilowatt-class fiber lasers, the inner cores reach about 40 µm, with optical tricks such as coiling the fiber helping to limit most emission to a single mode. Optical damage can be an issue for pulses with high peak power.
A big advantage of fiber lasers is the relatively large surface area per unit volume, which aids dissipation of waste heat that could cause beam distortion. Fiber lasers also benefit from inherently high efficiency if the light emitters and pump lines are carefully matched. Thus, a 1-kW pump source can produce 800 W of output from an ytterbium-doped fiber, leaving only 200 W of heat to be dissipated.
Cranking up the power
IPG Photonics (Oxford, MA) holds the record for raw power, produced by combining light from multiple ytterbium-doped fibers to produce a multimode beam. The beam quality can’t match that of single-mode lasers, but it’s adequate for industrial cutting and welding. IPG sells industrial lasers based on that technology, and supplied a 17-kW ytterbium-fiber laser to the new test center for welding aluminum alloys, which Bias (Bremen, Germany) opened earlier this year. IPG boasts the system has wall-plug efficiency of 30%, well above that of other industrial lasers.
Single-mode power has reached more than 10% of that level. At CLEO/Europe in June (Munich, Germany), IPG reported record CW power of 2 kW at 1075 nm from a ytterbium-fiber laser, with beam quality (M2) less than 1.2. Both the University of Southampton (England) and the Friedrich Schiller University Jena (Germany) have demonstrated more than 1 kW from single-mode ytterbium-doped fibers in the lab. In practice, the main limit on fiber-laser power is the cost of the pump diodes, says Johan Nilsson of Southampton, who also works with Southampton Photonics. Pump lasers are so expensive he says it’s hard to justify buying more just to set laboratory records.
A true single-mode fiber for the 1.1‑µm ytterbium band would have a core of only 6 µm, but larger cores are needed to generate high laser power. Reducing numerical aperture (NA) below 0.06 could increase single-mode core diameter, but comes at a cost of higher bending loss. In practice, designers use larger-core fibers, which they wind in coils to raise bending losses for high-order modes. Typical coils are about 5 cm in diameter. Laser oscillation enhances the single-mode selection effect, and fibers with inner-core diameter to 50 µm are used in coiled fiber lasers, says Andy Held, vice president of sales and marketing at Nufern (East Granby, CT; see Fig. 3).Nonlinear effects also constrain the design of high-power fiber lasers. Stimulated Raman scattering and stimulated Brillouin scattering can build up over long distances, so fibers are kept relatively short. Increasing core size helps ease nonlinear effects and the chance of end damage by reducing power density. However, care must be taken in fiber fabrication to ensure dopant uniformity in the center of the core.
Kilowatt single-mode powers remain in the laboratory realm, but CW powers of a couple hundred watts in a single mode are readily available in commercial ytterbium-fiber lasers. Their main applications are in precision machining.
Single-polarization operation is possible in a fiber laser made of large-core polarization-preserving fiber coiled so that one of the polarization modes leaks out. Nilsson’s group at Southampton recently reported 633-W plane-polarized CW output at 1.1 µm with about 10-nm linewidth.1 At the Solid State and Diode Laser Technology Review conference in June (Los Angelas, CA), Alamantas Galvanauskas of the University of Michigan reported 400-W linearly polarized output from a monolithic fiber laser with 2‑nm bandwidth.
A major attraction of polarized output is the prospect for efficient frequency doubling of near-infrared output into the visible. Aculight (Bothell, WA) has reported generating an average power of 60 W in the green by doubling a 10‑MHz pulsed ytterbium-fiber laser with average power of 110 W.2
MOPAs and pulsed lasers
Simple oscillators work well for generating CW output, but master-oscillator/power-amplifier (MOPA) designs, like the Aculight system, are proving valuable for pulsed or modulated output with comparable efficiency.
The advantage of the MOPA design comes from its ability to produce seed pulses at the milliwatt level using modulators, which can produce complex waveforms or chirped pulses but can’t withstand high powers. The power-amplifier stages then can multiply power levels, reproducing pulse shapes with high fidelity, says Nilsson. “What you put in is what you get out, except a thousand to a million times stronger.” This includes trains of modelocked pulses and broadband frequency combs.3
A new twist on fiber-MOPA systems is to inject a relatively high power, then raise it higher in gradual increments by passing it through a series of amplifying stages with increasing mode areas. Each would be pumped by a few hundred watts, and boost the power somewhat. This gradual amplification would avoid the thermal limitations of pumping the final stage with very high power, says Galvanauskas.
Other wavelengths
Ytterbium-doped lasers hold a clear lead in power capability, but other dopants offer other wavelengths desirable for specific applications.
The shortest wavelengths at which reasonable powers have been generated to date are around 0.9 µm, where a three-level neodymium fiber amplifier has generated up to 10 W with a slope efficiency of 54%.4 Ytterbium has a 980‑nm laser line that can be pumped by 915-nm diodes, which has generated up to 4 W with a slope efficiency of 40%.5
Erbium-doped fiber lasers emit up to around 100 W in the 1.5- to 1.6-µm range, which is attractive for eye-safe systems and telecommunications. Adding ytterbium to the core increases pump-light absorption at high powers, and an Er-Yb MOPA has generated CW powers to 150 W, but its efficiency was limited to 33%.6
Thulium-doped fibers can emit more than 30 W at 1.8 to 2.2 µm. Pumping is with diodes emitting near 790 nm, but each input photon can produce two output photons, so the slope efficiency can reach 74%. Nilsson’s group has reached 75 W by codoping with ytterbium and pumping at 975 nm, but the efficiency was limited to 32%.
Emerging trends and applications
Developers don’t think they’ve hit fundamental limits on fiber-laser power, noting that output power shows no signs of leveling off when plotted against pump power. But university groups are turning to address questions they consider more interesting-the potential uses of high-power fiber lasers in more-complex systems such as Raman conversion. “We’re going to have much better control of the light and be able to generate complex waveforms and patterns with high power,” Nilsson says. For example, pulse tailoring could generate long chirped pulses for laser radar, and harmonic generation could generate hundreds of watts at visible wavelengths.
Meanwhile, higher-power fiber lasers are in the running for the generation of 100-kW solid-state lasers envisioned by Pentagon planners. That’s a job beyond single-fiber lasers, so developers are working on coherent combination of the beams from several fiber lasers. That’s a tough problem, Monica Minden of HRL Laboratories (Malibu, CA) said at CLEO Europe, but her group has observed some coherent coupling among groups of neodymium fiber lasers.7
Plenty of challenges and questions remain. But expect plenty of action as well in development of high-power fiber lasers.
REFERENCES
- Y. Jeong et al., Optics Lett. 30, 955 (May 1, 2005).
- A. Liu et al., Optics Lett. 30, 67 (Jan. 1, 2005).
- B. R. Washburn et al., Optics Lett. 29, 250 (Feb 1, 2004).
- T. J. Kane et al., paper MD8, 2004 Topical Meeting, Advanced Solid State Photonics.
- D. B. S. Soh et al., paper MA2, 2004 Topical Meeting, Advanced Solid State Photonics.
- Y. Jeong et al., Postdeadline paper PDP 1, OFC 2005.
- H. Bruesselbach et al., Optics Lett. 30, 1339 (Jun 1, 2005).
About the Author
Jeff Hecht
Contributing Editor
Jeff Hecht is a regular contributing editor to Laser Focus World and has been covering the laser industry for 35 years. A prolific book author, Jeff's published works include “Understanding Fiber Optics,” “Understanding Lasers,” “The Laser Guidebook,” and “Beam Weapons: The Next Arms Race.” He also has written books on the histories of lasers and fiber optics, including “City of Light: The Story of Fiber Optics,” and “Beam: The Race to Make the Laser.” Find out more at jeffhecht.com.