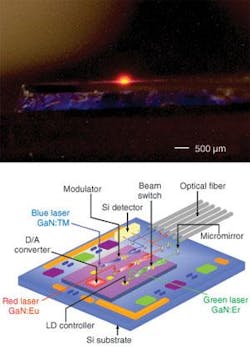
A flexible optical waveguide has been developed that can enable wearable computers and sensors, and ease constraints on assembly and packaging to facilitate integration of optical and electronic functions.
Building on techniques of laser-writing waveguides into rigid silica glass substrates for optical-circuit fabrication, scientists at the University of Toronto (Toronto, ON, Canada) have used a fluorine (F2) laser to directly write silica optical waveguides on the surface of silicone rubber.1 The hybrid glass-on-silicone structure is pliable like a traditional polymer waveguide, but has the advantage of being a carbon-free glass waveguide that provides superior spectral transparency at telecommunications wavelengths, offering heat and chemical resistance.
To fabricate the waveguides, light from the F2 laser was passed through a chromium-on-calcium fluoride photomask and onto the surface of a 2-mm-thick sheet of silicone rubber. An approximate 0.2-mm air gap separating the photomask from the rubber surface was necessary to provide a source of oxygen for a photochemical modification to take place. Surface swelling, gas-phase photodissociation, and other surface-modification processes produced the silica channels. Waveguides with a mode width (full width at half maximum) of 15 µm were created from 9000 laser pulses with a fluence of 10 mJ/cm2 delivered onto an 8-µm-wide mask feature.
Atomic-force-microscope images of a silica rib waveguide showed an approximate 3-µm peak height with 1-µm-deep side trenches, and an approximate 15‑nm root-mean-square surface roughness over the 3 × 3-µm probe area (see figure). In comparison, the nonradiated silicone rubber surface had an approximate 5-nm surface roughness.
To test the waveguides, the researchers butt-coupled 635-nm red light and 1550‑nm IR light from a silica-core fiber into the end facet of the silica rib waveguide. Because the end facets were not flat and could not be polished, index-matching fluid and a 150-µm-thick silica plate were used to enable imaging of the guiding-mode profile onto a CCD camera. The resulting non-Gaussian profile revealed the excitation of low-order modes that were about 20% smaller than the single-mode launch fiber.
By increasing the laser exposure to 72,000 pulses at the same 10-Hz repetition rate and 10-mJ/cm2 fluence, rib waveguides with an approximate 6-µm peak height were fabricated. Exponential fitting of the scattered-light intensity observed from the surface of the waveguide produced propagation losses of 15 dB/cm at 633 nm and 6 dB/cm at 1550 nm, with scattering and absorption of the evanescent fields in the silicone the most significant factor in the loss. These 2-mm-thick silicone samples could be flexed to an approximate 4-cm radius before an observable increase in propagation loss was seen.
“Silicone rubber is already a good optical material that can be cheaply molded into contact lenses, and silica is obviously our most important optical material,” says researcher Masayuki Okoshi. “The process to fabricate silica waveguides and potentially other micro-optic devices into optically flexible circuits is a novel opportunity for low-cost optical packaging in optical communication devices, optical backplanes, sensors, and lab-on-a-chip systems.” The researchers are now searching for interested industrial partners.
REFERENCE
1. M. Okoshi et al., Optics Letters 30 (20) 2730 (Oct. 15, 2005).
About the Author
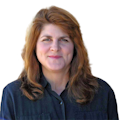
Gail Overton
Senior Editor (2004-2020)
Gail has more than 30 years of engineering, marketing, product management, and editorial experience in the photonics and optical communications industry. Before joining the staff at Laser Focus World in 2004, she held many product management and product marketing roles in the fiber-optics industry, most notably at Hughes (El Segundo, CA), GTE Labs (Waltham, MA), Corning (Corning, NY), Photon Kinetics (Beaverton, OR), and Newport Corporation (Irvine, CA). During her marketing career, Gail published articles in WDM Solutions and Sensors magazine and traveled internationally to conduct product and sales training. Gail received her BS degree in physics, with an emphasis in optics, from San Diego State University in San Diego, CA in May 1986.