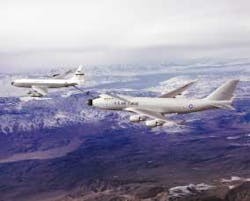
Editors note: This month brings the start of a new Back to Basics series in which contributing editor Jeff Hecht details the use of lasers and optoelectronics technologies for defense and security applications.
The conceptual seeds that grew into the Airborne Laser were planted 45 years ago, when Gordon Gould and Lawrence Goldmuntz brought a new idea to the then-new Advanced Research Projects Agency. Arthur Schawlow and Charles Townes had just published their proposal for an "optical maser" in Physical Review. Gould had independently invented what he called the "laser." The physical principles were the same, but Gould thought he could build a powerful version, one that he told ARPA might ultimately grow potent enough to zap nuclear-armed missiles out of the sky.
That dream has dazzled the Pentagon ever since, and the Missile Defense Agency hopes that the Airborne Laser (ABL) will realize it with a chemical oxygen iodine laser, or COIL, mounted in a converted Boeing 747 aircraft. When the laser is completely installed in the modified aircraft shown in Fig. 1, the ABL is to generate a megawatt-class beam to destroy ballistic missiles several hundred kilometers away during their vulnerable boost phase. The first lethality tests, originally scheduled for the end of this year, have slipped into early 2005, but MDA remains optimistic. In a recent fact sheet, the agency says the ABL may be available to shoot down missiles in case of emergency "as early as 2005, with a fully operational aircraft available later in the decade."
Skeptics aren't convinced the Airborne Laser is ready for prime time. Originally intended for use against short- and medium-range ballistic missiles, its mission has shifted to include intercontinental ballistic missiles. It fared better than kinetic-energy weapons in a report issued last July by the American Physical Society because laser beams reach their targets at the speed of light. The APS report said the laser might defend the United States against vulnerable liquid-fuelled missiles launched from North Korea, but couldn't cover all of Iran, or block sturdier solid-fueled boosters from North Korea. Skeptics warn that the ABL itself is vulnerable to attack, and note serious problems with earlier high-energy laser weapons. Even the optimists agree that it won't be easy for the ABL to do the intended job. Yet its mission is much easier than the Strategic Defense Initiative sought two decades ago.
Laser weapon development
High-energy laser weapon projects date back to the 1970s. The Air Force built the Airborne Laser Laboratory, a 400-kW gas dynamic carbon dioxide laser housed in a militarized Boeing 707. The Navy built a 2.2-mW deuterium-fluoride chemical laser called MIRACL, the Mid-Infrared Advanced Chemical Laser, now housed at the High Energy Laser Systems Test Facility at White Sands Missile Range. DARPA built a compact multimegawatt hydrogen fluoride chemical laser called Alpha, to study prospects for space-based laser battle stations.The ABL emerged from that technology experience and the shift of military interest after the Cold War. Beam transmission is tougher in the atmosphere than in space, but space is otherwise a much more difficult environment. Airborne platforms are much easier to operate and maintain. Adaptive optics can ease atmospheric propagation problems, although it can't eliminate them altogether. The 1.315-µm wavelength of the chemical oxygen iodine laser is much shorter than the 3.5 µm of deuterium fluoride or the 10 µm of CO2 lasers, allowing the use of much smaller optics.
During operation of a laser weapon system a target acquisition and tracking system detects and identifies potential targets, locks onto them, and tracks them (see Fig. 2). The laser generates a high-power beam, which it fires through the beam-directing optics. Atmospheric turbulence, self-focusing, and other effects tend to disrupt high-energy laser beams, so an adaptive optical system collects data on atmospheric perturbations, and adjusts the shape of the deformable output mirror to compensate. The beam pointing system focuses the beam onto the target, which is monitored to check the effect of the laser shots.Structure of the Airborne Laser
The heart of the ABL system is a bank of six COIL modules, each weighing 6500 pounds (including chemicals) and about the size of a Chevrolet Suburban standing on its end (see Fig. 3). Their output is combined and directed through a turret at the front of the aircraft, exiting through a 1.5-m window. Tanks at the back of the aircraft hold laser fuel.
The 1.315-µm iodine laser operates on a transition of atomic iodine. The chemical oxygen version is excited by excited oxygen molecules produced by a chemical reaction. Several reactions are possible. In the ABL, a basic solution of hydrogen peroxide is sprayed into chlorine gas, causing an exothermic reaction that heats gas and excites oxygen to the proper state. The O2 molecules flow to a second chamber in which they excite atomic iodine to produce a population inversion and laser action.
The exhaust gas is largely steam with small amounts of chlorine, hydrogen, and iodine. Vents exhaust the mixture into the atmosphere, with titanium sheets protecting the aluminum airframe from the hot gas. An airtight seal separates the crew compartment from the laser bay, protecting the crew from leaked laser exhaust, and maintaining comfortable pressure for the crew. The laser modules are designed to operate at the normal patrol altitude of 40,000 ft to optimize gas flow and exhaust. This design improves flight performance, but requires that tests be performed in a low-pressure chamber.
Optics combine the beams from the six modules and deliver the light to the beam-control system and a beam-directing turret mounted at the nose of the aircraft that aims the beam. The turret contains an adaptive-optic output mirror that adjusts the beam wavefront to compensate for atmospheric perturbations. The beam exits through a 1.5-m window, then converges to a spot of about 30 cm on target, where power density averages about 25 times that at the output mirror.
The acquisition, tracking, and pointing system includes three smaller lasers. An active carbon dioxide laser ranger tracks potential targets, measuring target range, speed, and course. It can monitor multiple targets, producing data that helps set attack priorities. The track illuminator laser is a 1.03-µm ytterbium:YAG laser that examines the target in detail, finding the nose and moving back down to locate the fuel tank which is the weakest point of a liquid-fuelled booster. The beacon illuminator laser is a 1.06-µm Nd:YAG laser, which illuminates a spot on the target, producing reflections monitored by the adaptive optical system to adjust the shape of the outgoing wavefront to compensate for atmospheric effects.
The initial aircraft (YAL-1A) has operating stations so the crew can monitor system performance during tests. Later versions will have only four battle-management stations to control the laser system and monitor potential targets. Once the shooting starts, computers will take control of the fast-changing situation.
The ABL is designed to fly at 40,000 ft and to hit missiles rising from the ground in their boost phase, when their course is clearly defined. Liquid-fuel tanks are the most vulnerable targets; heat weakens the walls of the pressurized tank, causing them to rupture. Solid-fuel boosters are less vulnerable, but sufficient heat would cause their outer wall to blow out, disabling the missile.
The aircraft can be refueled in flight to allow long patrol times, but the ABL would have to return to base to replenish the chemical fuels for the laser. The mass of laser fuel is classified, but in practice the main operational concern is the number of shots possible. That will vary considerably, depending on the distance of the target, the target type, and the conditions in the intervening atmosphere.
Status and operating plans
Full-scale development of the ABL began in 1996. The program has finished modifications to the aircraft and flight-tested it at the end of 2002. TRW—now part of Northrop-Grumman—built the first laser module, and tests two years ago at San Juan Capistrano showed that it could produce 118% of the projected power. Five copies of that module are now being built, and all six are being installed at the System Integration Laboratory at Edwards Air Force Base. That test bed is built around a scrapped 747 fuselage, to make sure that all the components fit into the space available. The laser modules will be fired together for the first time inside the Ground Pressure Recovery Assemble, a giant vacuum chamber that will bring pressure down to the level at 40,000 ft.
After those tests are completed, the laser modules will be disassembled and installed in the YAL-1A aircraft. The completed ABL is scheduled to get off the ground next year and start a series of test shots culminating in shooting down a ballistic missile. Once the lethality demonstration is finished, the Missile Defense Agency will make the Airborne Laser available for missile defense on an "initial emergency capability" basis as early as next year. Total spending from the start of development in 1996 through the lethality demonstration will come to $2.1 billion.
Although the initial ABL is intended to be useful for missile defense in case of emergency, the Missile Defense Agency does not consider it a "fully operational" aircraft. If performance goals are met, the Air Force will go on to build additional Airborne Lasers for deployment. Developers are still studying how many modules will be required for those units. Initial plans called for 12 or 14, providing about twice the total power of the initial Airborne Laser. Their mission will be defending against missile attack by so-called "rouge states," with North Korea and Iran now the biggest concerns.
There is no doubt the Airborne Laser will have a better chance of success than "Star Wars" defenses against thousands of nuclear missiles the Soviets had in the 1980s. Yet its success is uncertain. Technical obstacles are formidable, particularly in beam propagation and laser performance in the hostile aircraft environment. The APS report warned that its range would be limited to 600 km for liquid-fuel booster and 300 km for solid boosters—to protect against solid- or liquid-fuel Iranian missiles, or North Korean solid-fuel rockets. The big test is coming next year.
Further Reading
American Physical Society, Report of the APS study Group on Boost-Phase Intercept Systems for National Missile Defense (July 2003).
R. W. Duffner, Airborne Laser: Bullets of Light (Plenum, New York, 1997).
Jeff Hecht, Beam Weapons: The Next Arms Race (Iuniverse.com, reprint of 1984 Plenum book).
About the Author
Jeff Hecht
Contributing Editor
Jeff Hecht is a regular contributing editor to Laser Focus World and has been covering the laser industry for 35 years. A prolific book author, Jeff's published works include “Understanding Fiber Optics,” “Understanding Lasers,” “The Laser Guidebook,” and “Beam Weapons: The Next Arms Race.” He also has written books on the histories of lasers and fiber optics, including “City of Light: The Story of Fiber Optics,” and “Beam: The Race to Make the Laser.” Find out more at jeffhecht.com.