MIT molten-glass 3D printing makes complex optical components
A team of Massachusetts Institute of Technology (MIT; Cambridge, MA) researchers says they have opened up a new frontier in 3D printing: the ability to print optically transparent glass objects. The technology behind 3D printing—which MIT says grew out of early work at MIT—has exploded in recent years to encompass a wide variety of materials, including plastics and metals. Simultaneously, the cost of 3D printers has fallen sufficiently to make them household consumer items.
Now, the new system, described in the Journal of 3D Printing and Additive Manufacturing, was developed by Neri Oxman, an associate professor at the MIT Media Lab; Peter Houk, director of the MIT Glass Lab; MIT researchers John Klein and Michael Stern; and six others.
Other groups have attempted to 3D print glass objects, but a major obstacle has been the extremely high temperature needed to melt the material. Some have used tiny particles of glass, melded together at a lower temperature in a technique called sintering. But such objects are structurally weak and optically cloudy, eliminating two of glass’s most desirable attributes: strength and transparency.
The high-temperature system developed by the MIT team retains those properties, producing printed glass objects that are both strong and fully transparent to light. Like other 3D printers now on the market, the device can print designs created in a computer-assisted design program, producing a finished product with little human intervention.
In the present version, molten glass is loaded into a hopper in the top of the device after being gathered from a conventional glassblowing kiln. When completed, the finished piece must be cut away from the moving platform on which it is assembled. In operation, the device’s hopper, and a nozzle through which the glass is extruded to form an object, is maintained at temperatures of about 1900 degrees Fahrenheit, far higher than the temperatures used for other 3D printing. The stream of glowing molten glass from the nozzle resembles honey as it coils onto a platform, cooling and hardening as it goes.
"Glass is inherently a very difficult material to work with," Klein says: Its viscosity changes with temperature, requiring precise control of temperature at all stages of the process. The new process could allow unprecedented control over the glass shapes that can be produced, Oxman says.
"We can design and print components with variable thicknesses and complex inner features—unlike glassblowing, where the inner features reflect the outer shape," Oxman explains. For example, she adds, "We can control solar transmittance. … Unlike a pressed or blown-glass part, which necessarily has a smooth internal surface, a printed part can have complex surface features on the inside as well as the outside, and such features could act as optical lenses."
Houk cites several additional directions for pushing the research further. One is adding pressure to the system—either through a mechanical plunger or compressed gas—to produce a more uniform flow, and thus a more uniform width to the extruded filament of glass. Additional work will focus on the use of colors in the glass, which the team has already demonstrated in limited testing.
SOURCE: MIT; http://news.mit.edu/2015/3-d-printing-transparent-glass-0914
About the Author
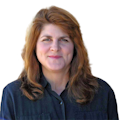
Gail Overton
Senior Editor (2004-2020)
Gail has more than 30 years of engineering, marketing, product management, and editorial experience in the photonics and optical communications industry. Before joining the staff at Laser Focus World in 2004, she held many product management and product marketing roles in the fiber-optics industry, most notably at Hughes (El Segundo, CA), GTE Labs (Waltham, MA), Corning (Corning, NY), Photon Kinetics (Beaverton, OR), and Newport Corporation (Irvine, CA). During her marketing career, Gail published articles in WDM Solutions and Sensors magazine and traveled internationally to conduct product and sales training. Gail received her BS degree in physics, with an emphasis in optics, from San Diego State University in San Diego, CA in May 1986.