Laser-based 3D nozzle quality test from Fraunhofer ILT improves laser material deposition
Aachen, Germany--Scientists at the Fraunhofer Institute for Laser Technology ILT have, for the first time, performed a laser-based qualitative and quantitative characterization of the powder gas stream in laser deposition welding processes. Laser deposition, also called laser sintering, laser additive manufacturing, and a number of other names, is an established processing technique for the repair and manufacture of metal parts and the functionalization of metal surfaces. Precise knowledge of the powder gas feed is an important parameter of the overall process and plays a key role in the results achieved and to maintain process quality.
In laser material deposition processes, a nozzle is used to inject a powdered filler material into the melt generated by the laser beam, producing a layer that is metallurgically bonded to the workpiece. The delivery of powder to the melt pool via the nozzle is a crucial element in this process and has a major influence on the consumption of powder material, the effectiveness of the gas shielding system used to prevent oxidation, and the quality of the coating layer. In order to ensure consistently high process stability and quality, it is necessary to check the processing results at regular intervals. This is because nozzle wear can lead to deviations that cause changes in the diameter and position of the powder focus. Orientation of the powder gas stream to the laser beam is of major importance. Until now, the only way of determining these changes was to use laser metal deposition to obtain reference samples. Correlating these samples with comparative deposited welds revealed the quality of the nozzle.
But a Fraunhofer ILT team has now developed a measurement procedure for characterizing the powder gas stream that offers a simple and reproducible means of checking nozzle quality. The process involves illuminating the powder gas stream from the side with a laser beam and using a camera positioned coaxially to the nozzle to capture images of the powder gas stream through the nozzle. This makes the ring-shaped distribution of the powder visible. Thanks to the camera's high frame rate, it is possible to precisely determine the number and position of individual powder particles at a defined point in time. Based on similar principles to laser caustic measurement, the lateral laser beam moves down the powder gas stream layer by layer, requiring just a few seconds to capture the data for each layer. The system then calculates the particle density distribution for each layer from the several thousand individual images captured by the camera. Finally, the individual layer images are superimposed on each other to yield the overall spatial particle density distribution.
"For the first time, we have succeeded in developing a measuring procedure that enables us to determine the constancy of the powder mass flow, the symmetry of the powder gas stream, and the position and size of the powder focus," says Stefan Mann, who is in charge of the project at the Fraunhofer ILT. Potential applications of this new measuring technique include all activities in the field of laser deposition welding, in particular engine and power plant manufacturing, toolmaking, and mechanical engineering.
A live demonstration of this measuring procedure will be held in the Fraunhofer ILT's laser equipment facility in Aachen on May 11 as part of the "Laser Technology Live" event at the International Laser Technology Congress AKL'12. To find out more, visit www.lasercongress.org.
SOURCE: Fraunhofer ILT; www.ilt.fraunhofer.de/en/publication-and-press/press-release/press-release-2012/press-release-2012-04-25.html
About the Author
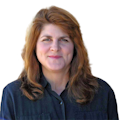
Gail Overton
Senior Editor (2004-2020)
Gail has more than 30 years of engineering, marketing, product management, and editorial experience in the photonics and optical communications industry. Before joining the staff at Laser Focus World in 2004, she held many product management and product marketing roles in the fiber-optics industry, most notably at Hughes (El Segundo, CA), GTE Labs (Waltham, MA), Corning (Corning, NY), Photon Kinetics (Beaverton, OR), and Newport Corporation (Irvine, CA). During her marketing career, Gail published articles in WDM Solutions and Sensors magazine and traveled internationally to conduct product and sales training. Gail received her BS degree in physics, with an emphasis in optics, from San Diego State University in San Diego, CA in May 1986.