MOTION CONTROL: Nanopositioning technology shows progress on multiple levels
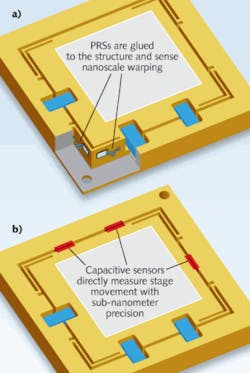
Nanopositioning has become a key enabling technology in many areas of photonics including laser systems, scanning microscopy, semiconductor test and measurement, nanoimprinting, and microlithography, to name a few. Piezoelectric-based positioners have always been known for their ability to provide subnanometer precise motion, though over limited travel ranges.
Recent progress in control technologies and piezoceramic actuator and motor design has resolved the conflict between travel range and precision. Motion engineers can now select from a number of piezo systems with long travel, high stability, exceptional speed, and high force generation while still featuring compact design, the absence of stray electric fields, and stable position holding when the power is turned off.
Speed and throughput
In the nano world, effective speed of a system is often more determined by settling time (milliseconds) or scanning frequencies than the classical velocity definition of inches per second.
Especially when motions are minute—such as in scanning microscopy applications, where lenses or samples need to be moved in and out of focus quickly to access multiple planes of a biological cell to create a 3D image—the distances between each image plane are measured in submicrons; here, classical positioning devices with heavy motors and bearings are not up to the task. Piezo mechanisms are well suited for such applications due to their combination of stiffness, low mass, and precision. Based on a frictionless flexure guiding system and integrated lever mechanism, compact and cost-effective mechanisms with hundreds of microns of travel are feasible today—plenty for most bio-imaging applications. The fastest piezo mechanisms today can move and settle to a new position in about 3 to 5 ms, at least one order of magnitude faster than conventional positioners.
A breakthrough in compact piezomotor technology now provides up to 1000 µm of travel for applications with large penetration depths such as required in two-photon microscopy. The new design maintains the compactness and achieves the travel without giving up the stiff design, important to achieve aggressive step-and-settle performance even with heavy high-numerical-aperture objectives. The unit is compatible with standard microscopes and mounted between turret and objective providing the highest available axial positioning range yet is significantly more compact than conventional motorized mounts. Its novel design principle also offers superior stiffness compared to highly leveraged piezo designs.
Nanopositioning controllers rely on the feedback of extremely sensitive, high-speed position sensors. As of today, the highest-performing sensors capable of providing subnanometer position information are sophisticated analog absolute-measurement devices. Analog servos are extremely fast and are not limited by processor clock rates or digital/analog/digital conversion processes. As a result, nanopositioning controllers have conventionally been mostly based on analog architectures.
In recent years, the most demanding applications have called for more sophisticated digital controllers for reasons of serviceability, flexibility, and functionality. Digital linearization, synchronization with external events, and programmable coordinate transformation were other driving factors. However, these features came at a high price that limited their use to high-end applications.
The newest controllers now offer the advantages of digital control at a cost up to an order of magnitude less than other currently available digital piezo controllers, and are making nanopositioning systems more user-friendly and accessible to more cost-sensitive markets.
Moving from inferred to direct metrology
In the past, many piezo nanopositioning systems were equipped with piezoresistive strain-gauge sensors, mainly to cut costs. These miniature sensors are easy to integrate and have sufficient accuracy for most applications. Due to the way this type of sensor functions, however, it cannot measure actual distance but rather infers the position of the moving platform from the nanoscale warping of the structure to which it is attached. Based on the indirect measure of position, inaccuracies can occur and orthogonality errors are not observable.
For more demanding applications, a different approach in the form of direct-metrology sensors has become a new standard. Capacitive, noncontacting feedback is the technology of choice here, and recent advances in the manufacturing process have helped to make these sensors more affordable. Because the stage platform is measured directly, stability and position linearity are greatly improved; in addition, crosstalk errors are eliminated (see Fig. 1).
Moving farther with higher force
One of the benefits of classical piezo-stack motion is the high force and consequently fast response these units provide. To overcome the drawback of a short travel range, multiple piezo elements can be arranged to act in longitudinal and transverse directions, composing a “walking” actuator with infinitely variable step width. A distant relative of this family of mechanisms was the Inchworm by Burleigh Instruments (Fishers, NY), which was based on low-force, piezo-tube actuators.
In the 1990s, commercial piezo-walk designs replaced the fragile tubes with robust piezo stacks, yielding significantly more force. They were first used in automated photonics-alignment systems. Mechanisms developed more recently have extremely high stiffness and holding forces up to 180 lb; they are optimized for reliability in applications simultaneously requiring long-term position hold, tens of millimeters of travel, and picometer-class resolution. Nonmagnetic in design and insensitive to electromagnetic pulse (EMP) disturbances, piezo-walk motors are used in high-energy physics applications, astronomy, and semiconductor test equipment as well as in medical applications such as MRI scanners.
A smaller, more cost-effective version uses a monolithic manufacturing process in which the whole drive element is essentially made of one cofired multilayer ceramic block. Size and cost are substantially reduced while the excellent power-off stiffness and high holding force is maintained. This design also can provide tens of millimeters of travel range and picometer-class resolution for applications like nanolithography and electron microscopy. As with all piezoelectric motors, piezo-walk drives are inherently vacuum-compatible and fieldless.
When arranged in a parallel kinematic hexapod design, these drives can provide motion in six degrees of freedom (see Fig. 2). Systems capable of handling several pounds of load can be designed in an envelope the size of an apple or smaller while providing subnanometer linear motion and submicroradian angular precision. The hexapod approach, with its virtual pivot point and capacity for a large central aperture, has become crucial for optical alignment of elements as large as secondary mirrors in the latest-generation ground telescopes, and as small as automated fiber-to-photonic-component alignment.High speed and resolution are not always the most critical design parameters. Some processes in optical trapping, microscopy, and optics alignment also require long-term stability on the nanometer scale once a position has been reached. Traditional lead-screw drive systems, linear motors, and so on all either rely on an active servo to hold the position or are sensitive to drift caused by relaxation in bearings or other drive train components. A novel type of piezoceramic linear motor now overcomes these limitations. Its ultrasonic ceramic/ceramic drive principle automatically locks the moving part of the stage into place whenever the final position has been reached, resulting in no further heat generation or servo dither. Its significantly smaller size also enhances temperature stability. Positioning stages based on this principle can achieve multiple times the stability of conventional stages and hold a position to within 10 nm over 30 min in lab conditions.1
Coarse/fine positioning: Hybrid mechanisms
Piezo actuation can also be used to enhance the performance of classical motors and drive systems, forming a coarse/fine positioning system. Traditional coarse/fine mechanisms were run with independent control loops, hindering overall system repeatability and accuracy. The advent of higher-performance motion-control chips and linear encoders with nanometer-scale resolution has allowed construction of hybrid mechanisms in which one feedback sensor provides information to both the coarse- and fine-control loops.The construction of such a hybrid servo is significantly more complex (analogous to controlling an internal combustion engine and electric motor in a hybrid vehicle at the same time) and the result is the combination of piezo-class dynamics, repeatability, and high stiffness with many inches of travel (see Fig. 3). Requirements for motion devices like these come from the astronomy community, where the next generation of multimirror optical telescopes need long travel, extremely high forces, and motion uniformity with tracking accuracy of less than 2 nm and short-term interpolation errors of less than 0.5 nm.2
REFERENCES
1. S. Jordan and P. Anthony, Curr. Pharm. Biotechnol., 10, 515, http://bit.ly/eN3mFe (2009).
2. R. Gloess et al., “Ultra-High Precision Actuator for the Primary Mirror of the 42 m E-ELT Telescope,” Actuator 2010 Conference, poster session, Bremen, Germany.
About the Author
Stefan Vorndran
Stefan Vorndran is VP of marketing at PI (Physik Instrumente; Auburn, MA).