PHOTONICS APPLIED: THIN-FILM APPLICATIONS: Coatings for plastic optics step up to meet higher-end applications
Once relegated to low-end, disposable, nonimaging consumer applications, plastic or polymer/organic optics have improved in performance and durability and are entering nontraditional industrial, automotive, and medical industries. These new applications challenge not only the plastic substrate, but also the optical coatings applied to it. As Angus MacLeod—coating expert from the Thin Film Center (Tucson, AZ)—says, “Without optical coatings, virtually every modern optical application or system would fail.”
Today, research organizations and companies are developing and commercializing thin-film coatings for plastic optics used in digital cameras, barcode scanners, fiber-optic sensor and communications networks, biometric security systems, and as Fresnel lenses in concentrating solar power systems. As the allure of these generally lower-cost (and recently, higher-performance) polymer optics continues to grow, so too must the thin-film coating technologies that enable new applications.
Why plastic?
“Unlike glass-based optics, plastic optics weigh two to five times less, making them more practical for night-vision headgear, field-portable imaging applications, and in reusable and/or disposable medical instruments such as laparoscopes,” says Loretta Fendrock, coatings manager at G-S Plastic Optics (Rochester, NY). “And because plastic optics can be molded along with mounting tabs or other positioning features, assembly steps and manufacturing costs are reduced.”
Fendrock says that plastic optics can be used in most visible-light applications, and for other near-ultraviolet (near-UV) and near-infrared (near-IR) applications—transmission generally ranges from 380–100 nm for such common materials as acrylic (outstanding transparency), polycarbonate (best impact strength), and cycloolefins (high heat resistance and durability with low water absorption). Coatings are applied to plastic optics for the same reasons they are applied to glass optics: to improve transmission or reflection properties and to add durability.
“Thick-film coatings—generally about a micron or more in thickness—are applied as protective layers, but also to improve adhesion or durability of subsequent thin-film coatings,” says Fendrock. “Thin-film coatings include such oxides as silicon dioxide, tantalum oxide, titanium oxide, aluminum oxide, niobium oxide, and hafnium oxide [SiO2, Ta2O5, TiO2, Al2O3, Nb3O5, and HfO2], while metallic mirror coatings are typically aluminum [Al], silver [Ag], and gold [Au].” Fendrock says that fluorides or nitrides are rarely used, since to get good films, you need to use high heat, which is not compatible with the low-heat deposition conditions needed to coat plastics. “Electron-beam sources and resistance sources are used in evaporation coaters to melt the materials and deposit the vapor onto the substrates [physical vapor deposition]. Ion-beam sources are used to preclean before coating and to affect material properties during deposition,” adds Fendrock. “And sputtering is another physical vapor deposition technique that can be used to coat very large-area substrates such as plastic windows.”
But despite their benefits, plastic optics can also present challenges. “Some coating designs that might be used on glass optics may not be environmentally stable on plastic due to its high coefficient of thermal expansion,” says Fendrock. “For this reason, reflectors or bandpass filters formed entirely of dielectrics are not that common on plastics as they may develop adhesion or cracking problems.” One alternative that eliminates this problem is liquid-polymer nanocomposite coatings. Applied using a NanoClear coating system from Optical Dynamics (Louisville, KY), these coatings do not require a vacuum chamber and exhibit thermal expansion properties similar to the polymer substrate to avoid thermal craze failures (see Fig. 1).Beich says aluminum was chosen because it is reflective throughout the visible wavelength range and more environmentally durable than silver. Enhanced coatings of dielectrics on the aluminum were tuned to allow nearly equal reflectivity of the blue, green, and red channels. “One of the benefits of coating in-house is that we can more fully control all of the elements of manufacture. In this case, we further streamlined the manufacturing process by custom designing trays to work with our packaging and coating facility, improving overall productivity,” added Beich.
A much more common type of coated plastic optic may be resting right on your nose: eyeglasses. “Ophthalmic antireflection [AR] coatings are so commonplace today that we give them little thought; more than 95% of eyeglasses use plastic lenses and coating them is really a technical marvel representing 20 years of technological advances,” says Edwin Ellefsen, president of Opticote (Franklin Park, IL). “Apart from the assumed optical and cosmetic requirements, physical durability poses special challenges. First of all, eyeglasses are made of numerous and often unknown (to the coater) substrates, including allyl diglycol carbonate, polycarbonate, and dozens of proprietary blends with refractive indices ranging from 1.48 to 1.74. The substrates are hydroscopic—leading to moisture attack from the substrate side, have high thermal coefficients of expansion, and many exhibit weak boundary layers where the monomer is not fully cross-linked at the lens surface, so even when the coating sticks to the lens, it may rip off the outer surface of the lens.” Ellefsen adds, “Washed daily with harsh chemicals, wiped with coarse paper towels or gritty handkerchiefs, enduring temperatures from freezing winters to hot car dashboards, and occasionally insulted by hairspray or slid across a table face down, it’s a wonder they last as long as they do.”
To combat this harsh treatment, Opticote carefully classifies the incoming substrate and routes the glasses through appropriate aqueous and solvent-based ex situ cleaning steps. After thorough drying, vacuum surface treatments are followed by adhesion layers and by substrate-facing barrier layers (see Fig. 3). Next, an AR or mirror coating is evaporated, followed by more barrier layers, and finally, a hydrophobic/oleophobic topcoat is chemically bonded to keep the coated lens clean.“Plastic optics are particularly useful for flight hardware, for instance, in a heads-up display [HUD], where weight is a critical concern,” says Shari Powell, coatings manager at Polymer Optics (Santa Rosa, CA). “A HUD is like many other complex optical systems where scattered light from stray reflections causes problems and thus antireflection coatings are required.” Powell adds that plastic is the best material for molding such complex shapes as compound parabolic concentrator optics. Although these can be coated with highly reflecting metals and multilayer oxide enhancements, new techniques are needed to support emerging applications for plastic optics.
Beyond traditional coatings
Deposition of thin-film layers on plastic optics typically involves low-temperature (below 150ºC) physical vapor deposition of oxides assisted by cold plasma or ion bombardment (plasma-ion-assisted deposition or PIAD) or wet chemical coatings cured by UV light that can increase abrasion/chemical resistance for plastic optics, or provide special surface-wetting and other properties.1 But Ulrike Schulz, group manager for the Coating on Plastics research group at the Fraunhofer Institute for Applied Optics and Precision Engineering (Fraunhofer IOF; Jena, Germany), is working on some new plasma etching processes specifically developed to create AR nanostructured surfaces directly on polymer optics (see Fig. 4).Since the biomimetically inspired discovery that moth eyes have excellent AR properties, Fraunhofer IOF researchers have worked to fabricate sub-micron moth-eye structures in polymer materials that serve as AR coatings.2 Polymer optics represent a unique opportunity: These surface structures can be fabricated directly within the polymer optics themselves or in organic coating materials such as melamine that can be applied to either glass or plastic optics.
“Because individual plastic materials show different interactions with electron-beam and ion-beam source emissions (UV radiation, ions), these interactions have a large impact on the coating adhesion and the long-time durability of the coated optics,” says Schulz. “As a result, we have developed specialized processes for polymethylmethacrylate [PMMA], polycarbonate, and polycycloolefin materials taking into account their individual adhesion properties.” For example, Fraunhofer IOF has fabricated a polymer dashboard window for Audi finished on the outer surface with a hard AR coating deposited by PIAD with a plasma-etched structure on the inner side (see Fig. 5). “Although the Audi dashboard window is a demonstrator and not yet in production, it has the desirable potential to reduce the weight of a vehicle,” adds Schulz.
REFERENCES
1. U. Schulz, “Coating on plastics” in Handbook
of Plastic Optics, 2nd ed., Wiley-VCH, Berlin,
ISBN 978-3-527-40320-2, 161-195 (2010).
2. U. Schulz et al., Chinese Opt. Lett., 8, Supplement,
1–3 (April 2010).
About the Author
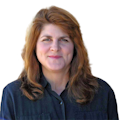
Gail Overton
Senior Editor (2004-2020)
Gail has more than 30 years of engineering, marketing, product management, and editorial experience in the photonics and optical communications industry. Before joining the staff at Laser Focus World in 2004, she held many product management and product marketing roles in the fiber-optics industry, most notably at Hughes (El Segundo, CA), GTE Labs (Waltham, MA), Corning (Corning, NY), Photon Kinetics (Beaverton, OR), and Newport Corporation (Irvine, CA). During her marketing career, Gail published articles in WDM Solutions and Sensors magazine and traveled internationally to conduct product and sales training. Gail received her BS degree in physics, with an emphasis in optics, from San Diego State University in San Diego, CA in May 1986.