PHOTONICS APPLIED: PHOTOVOLTAIC SYSTEMS: Optics take center stage in concentrating photovoltaic systems
Concentrating photovoltaic (CPV) systems (in their low-, medium-, and high-concentrating PV implementations LCPV, MCPV, and HCPV) use a variety of optical devices to focus a large physical area of solar radiation onto smaller PV cells (see Fig. 1). Ultimately, the aim is to reduce the use of high-cost semiconductor material using low-cost optics, improving overall PV output and lowering system costs.
The total CPV market is expected to reach $266 million by 2014, with Europe commanding the maximum market share at 59.3%, followed by 32% for the Americas.1 Even though CPV will represent less than 1% of the total $38.1 billion worldwide PV market by 2014, its proponents say that its growth rate will be higher (33% to 39% compared to 12.5% for the overall PV market) and that it has the potential to achieve grid parity faster than competing technologies.
Currently, CPV systems are commercially available from such manufacturers as Concentrix Solar (Freiburg, Germany), OPEL Solar (Shelton, CT), Emcore (Albuquerque, NM), SolFocus (Mountain View, CA), Prism Solar Technologies (Highland, NY), and a host of other small and large solar-cell companies. Indeed, the number of different concentrating optical designs is even larger than the number of commercial companies in this arena, as more and more new technologies are being developed in research labs everyday. But which optical technologies deliver the highest electrical output? And how do CPV systems differ from traditional crystalline silicon and other popular PV technologies in terms of system efficiency and watts per unit area?
So many designs ...
Typical concentrating optics include Fresnel zone plates, micro-optic collectors, and parabolic mirror designs with harsh-environment coatings.
A variation of the Fresnel option is the HCPV dual-element refractive concentration architecture from OPEL Solar (see Fig. 2). Unfortunately, most CPV manufacturers will not reveal how their "proprietary" optical designs function. "In our dual-element design, the first element is a Fresnel lens, and the second element provides additional functionality that improves the angle of acceptance of the panel with respect to the solar energy hitting its surface, for example," says Frank Middleton, OPEL's VP of marketing. The dual-element system concentrates solar energy onto triple-junction III-V type solar cells from Spectrolab (Sylmar, CA; a Boeing company); in fact, OPEL Solar is a beta site for Spectrolab. According to OPEL, these cells are twice as efficient as conventional solar cells.Concentrix Solar also uses a Fresnel-based optical system; however, CTO Andreas Gombert is proud to say that rather than developing a complex optical system, Concentrix chose an ultra-simple Fresnel-only concentrating design and instead decided to focus on system reliability: Standard Fresnel lens arrays are replicated in silicone rubber, already extensively used for high-power LEDs and extremely resilient at high temperatures. "Our focus is on using existing, robust technology and maintaining excellent precision between the focal point of our silicone Fresnel lenses and the solar cells," says Gombert. "Our FLATCON design is a nearly hermetic double-glazed window of sorts, with glass top and bottom plates protecting the UV-stable Fresnel optic; in fact, we have tested our materials and found no degradation, even with illumination doses equivalent to 3200 years of UV radiation."
More exotic concentrating optics include holographic planar concentrator (HPC) technology from Prism Solar Technologies. A stack of holographic optical elements (imprinted using diode-pumped solid-state lasers) diffract wavelengths usable by the solar cells while passing through unusable wavelengths. The usable energy guided by total internal reflection at the glass/air interface to the solar cells results in a threefold concentration of energy per unit area of photovoltaic material.
Other concentrating optical designs use mirror-based designs. Professors Jeffrey Gordon and Daniel Feuermann of the Ben-Gurion University of the Negev (Beer-Sheva, Israel) developed the mini-dish approach adopted by SolFocus.2 The first-generation system from SolFocus has a primary mirror that collects and focuses sunlight onto a secondary mirror, which reflects the concentrated sunlight onto a non-imaging optic located directly over the solar cell; a honeycomb arrangement of mini-dishes makes up the solar module. The professors are also pioneering the development of unfolded dual-mirror aplanats.3 These folded-mirror optics reduce the number of hot spots compared to other optical designs, enabling the option of coated polymeric reflectors that reduce mass and cost.
Another mirror-based approach uses micro-optoelectromechanical systems (MOEMS) based on micromechanical mirror arrays for light guiding, steering, and concentration.4 The arrays can be electrostatically tuned in two directions with a voltage of under 100 V to track the sun's position, while offering mass-production compatibility, long lifetime, and low cost. These micromirror designs are also the subject of research at the University of Kassel (Kassel, Germany), where lithographically patterned micromirror arrays can be applied to CPV applications.5 Currently they exist as a feasibility study with a size of around 10 cm2. Upscaling to large areas, fill factor optimization, and encapsulation of the micromirror modules will be challenging for future applications.
Efficiency and output— not a slam dunk
"When we decided to move beyond our semiconductor roots at OPEL, we decided to manufacture a CPV system including both the concentrator optics and the solar cell," says Middleton. "Even though the principle behind CPV is straightforward, implementation is tricky."
Indeed, CPV systems require a well-engineered "package" that incorporates optics, semiconductor material, and—common to all CPV systems—solar tracker hardware to maximize output. This requirement for trackers is the reason CPV manufacturers target utility-scale installations: Trackers preclude cost-effective installation for residential applications. OPEL Solar offers both small single-axis trackers (42 modules for a 3800 W output) and utility-scale dual-axis trackers (100 modules for a 9000 W output) that can also be used to increase the output of a PV system by 40%. Each roughly 11 × 62 in. OPEL module consists of six optical elements focused on six solar cells, with a rated output of 90 W ± 3% at 900 W/m2 solar irradiance. Even though the definition of a "module" differs for each supplier, a quantitative comparison of various optical designs can be formulated, assuming a linear relationship between solar irradiance values (see table)."All watts are not created equal," Middleton explains. Even though an analysis of power output (W) versus physical area (m2) for CPV modules can give a ballpark indication of which technologies provide the best "concentration" factor in terms of optical design and chosen PV material for the solar cell, nearly every company I spoke with rightly explained that the numbers are not straightforward. "A CPV system is more than the optics and solar cell: The contributions of tracking precision, module lifetime, solar irradiance/site temperature, and inverter/electronics, all need to be considered," says Middleton. "This is also true when comparing CPV to, say, thin-film or silicon systems: Even though silicon may be running at $2 per watt, and thin film $1 per watt, thin-film systems are more costly to install on a per-watt basis and require a much larger installation area to achieve the same output due to their reduced conversion efficiencies."
Concentrix Solar also emphasizes the reliability mantra. "Because our lenses and solar cells are smaller than in typical Fresnel-based CPV systems, the heat load is very small, and system reliability is improved," says Gombert. The Concentrix Solar module has an active area of approximately 80 × 40 cm composed of 200 single lenses (40 × 40 mm) focused on 200 solar cells, each with a 2.3 mm active area (see Fig. 3). This point-focusing module offers a 500× concentration factor, with an output of 75 W measured at an irradiance of 850 W/m2.CPV vs. traditional PV
A major advantage of CPV systems over crystalline-silicon solutions is superior performance in geographical regions with high solar irradiance (high temperature). "When temperatures reach 40°C, a crystalline silicon solar panel rated at 100 W will put out just 75 W due to the temperature coefficient of silicon," says Middleton, "However, our solar panel will produce 94 to 96 W." For high-solar-irradiance regions, CPV systems perform better than traditional silicon, taking up less physical area per watt than either crystalline silicon or thin-film solutions. In fact, Gombert says that in sunny locations, electricity production costs are 10% to 20% lower for FLATCON CPV systems compared to conventional flat-plate modules. However, unlike traditional flat-plate PV, CPV systems will not function on cloudy days as the optics cannot focus diffuse illumination.
In today's competitive solar market, optical-component designers are eager to partner with CPV manufacturers to benefit from the high growth rates for this technology. For example, OPEL Solar collaborates on CPV optics with the National Research Council (NRC; Ottawa, ON, Canada) on a project-by-project basis and has a formal relationship with the University of Connecticut on semiconductor developments, while Concentrix Solar partners with the Fraunhofer Institute for Solar Energy Systems (Freiburg, Germany) on concentrating optics and reliability testing for its CPV system.
But despite the importance of optics in improving module efficiency for CPV systems, the limiting cost for CPV installations is ultimately the hardware. "To reach grid parity, you need to make sure that the 'variable' cost of your optics and solar cells is much smaller than the 'fixed' cost of hardware such as mounting frames, trackers, and inverters," says Gombert. "Then, you need to make sure that your CPV system is ultrareliable and leaves no lifetime questions in the minds of your customers." OPEL Solar agrees: "With risk-averse utility companies as the primary solar-energy adopters, crystalline silicon is still the design of choice," says Middleton. "However, CPV is just now emerging and will make its mark in high-average-temperature locations once its reliability, like silicon, is proven in the marketplace."
REFERENCES
- Concentrated Photovoltaic and Solar Photovoltaic Global Markets (2009-2014), Markets and Markets (Wilmington, DE), Report Code: EP 1015 (December 2009).
- E.A. Gunther, "SolFocus vs. Concentrix Solar: Battle of the Solar Concentrator PhotoVoltaic (CPV) start-ups," blog entry at guntherport folio.blogspot.com (Aug. 23, 2006).
- J.M. Gordon et al., Optics Lett. 33, p. 1114 (2008).
- J. Ackermann et al., Proc. SPIE, p. 6993 (April 25, 2008).
- V. Viereck et al., Photonik International 2009(2), p. 48 (February 2009).
About the Author
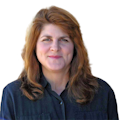
Gail Overton
Senior Editor (2004-2020)
Gail has more than 30 years of engineering, marketing, product management, and editorial experience in the photonics and optical communications industry. Before joining the staff at Laser Focus World in 2004, she held many product management and product marketing roles in the fiber-optics industry, most notably at Hughes (El Segundo, CA), GTE Labs (Waltham, MA), Corning (Corning, NY), Photon Kinetics (Beaverton, OR), and Newport Corporation (Irvine, CA). During her marketing career, Gail published articles in WDM Solutions and Sensors magazine and traveled internationally to conduct product and sales training. Gail received her BS degree in physics, with an emphasis in optics, from San Diego State University in San Diego, CA in May 1986.